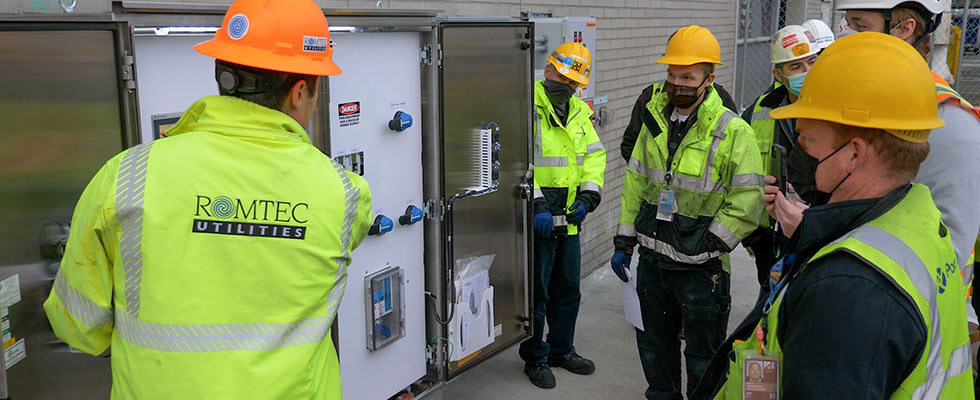
All pumping systems have structural and mechanical aspects that drive the design of each individual system. Considerations should also be made for electrical aspects and their related control and communication during the design of the structural and mechanical. After all, the control panel is the gateway between the operators and the pumping system. It is the first thing any operator touches and the first thing they admit they do not understand. For years, control panel configurations, functionality and related ease of operation have been based on what some technologically advanced designers wanted the operators to understand as opposed to what they do understand. Control panels and the current and future capabilities of the operators will always be somewhat at odds. Of course, the operators can learn more, and they can all become more technically savvy, but until they are all packing laptops and can diagnose the source of every alarm, there is still a case for simpler design.
The fundamental intent of this writing is to help others recognize pumping systems and their control and communication must be based on the real-world skills and understanding of current and future operators. The most sophisticated panel design may or may not be part of the plan, but without design continuity, both owners and operators face the impossible task of dealing with multiple systems that all operate differently.
All pumping system control panels, regardless of their sophistication, must have the following:
- a method of control
- some type of instrumentation
- an operator interface
- some type of telemetry
Remember, everyone sees controls differently, and there is no right or wrong way. Regardless of how high the flow and total dynamic head (TDHP) are, one can have either a good, simple control panel or a good, complex control panel. It is up to the user to decide which is appropriate.
Simple vs. Complex
A. Levels of redundancy equals more complex
a. Two different types of level sensing with two independent types of control equals more complex.
b. More information available at the site equals more complex.
c. Remote monitoring and control capability equals more complex.
d. Method of motor starting i.e., across the line versus soft starters, variable frequency drives (VFDs) or any combination, equals more complex.
e. Monitoring of ancillary devices like generators, flow meters, proximity switches, intrusions switches, odor control, etc., equals more complex.
The irony here is that the most complex control and communication configurations are not necessarily the best for everyone and in other ways are the least complex. The key to it all is matching the control and communication configurations with the ability and understanding of the operators.
How Much Information Is Needed, & How Should It Be Presented?
Let’s break down panels from the most basic to most complex.
Level 1: Most simple
One of the simplest examples is an alternator with floats. Red, yellow and green lights indicate pump operations, and it includes a “hand, off, auto” switch. This is a simple and effective true panel configuration.
Positives – This configuration is user friendly for just about everyone. It is easy to understand and easy to troubleshoot. They are made with available parts, and replacements are easy to find.
Negatives – This type of panel conveys only the essential information to the operator. It also, potentially, has little or no redundancy and provides limited remote capability.
Level 2: The first step up
This panel will have all the basics of Level 1 and adds some type of analog instrumentation and control. For example, a proprietary controller.
This configuration is typical with many different brands of proprietary controllers. In other words, the main step up referenced here is to take the most basic configuration and add a brand name, proprietary pump station controller. This addition typically provides more information and control via an analog signal coming from a level-sensing device like an ultrasonic transducer, radar detector or a submersible pressure transducer. When one adds any of these devices, they also add complexity and additional points that could fail. Thus, this type of configuration is also typically paired with a redundant (secondary) level and control configuration. When a user adds an analog signal for control (i.e., pressure transducer, ultrasonic, bubbler or radar), that device should be paired with a simple hardware-based system, like relays or floats, to provide a level of redundancy.
Different types of water and different applications compel the pumping systems and control system designer to employ various levels of redundancy. For example, sewers typically require redundant pumps, controls, power and panel hardware. The simplest solution is not appropriate when redundancy is required.
Level 3: The next step up
While the virtues of the simple control panel design should be lauded as it requires the lowest level of operator understanding, its limitations must also be accepted. Something as simple as adding redundancy or the need for a digitally displayed level pushes into things like proprietary controllers. Therefore, what is the problem with added redundancy and backup?
It turns out that proprietary controllers also have limitations. As the operator’s knowledge and understanding grows, the proprietary controller’s capability does not, and a problem begins to develop as additional functionality or information is desired. It should be easy to understand there is no way to grow in a variety of modern pumping system operations with any proprietary controller. Most know proprietary controllers are not known for being the toughest and most reliable. That title has always belonged to the programmable logic controllers (PLCs) with a human machine interface (HMI).
However, there are a couple of problems with PLCs in both on-site and remote operations. One must find a pumping system supplier who provides the appropriate code along with the appropriate PLC with the appropriate displays. There are few companies who will provide a PLC/HMI control panel configuration with custom code at no extra charge.
The good news is now users can have complete control of their current and future pumping systems. The bad news, ironically, is the same.
This is the world of flexibility with major (open architecture) brands of PLCs. A basic to advanced level of understanding of code writing is required. Users are in control of present and future operations of their one, or many, pumping systems. This is a real commitment that can be easy or be more than the user’s team can handle. Though it may be the best, most reliable and most flexible pumping system control panel configuration possible, it may not be necessary for the application or could be an inappropriate match for the capabilities of the owning entity. What is appropriate or best should now be considered. For example, the entity with only one pumping system versus the entity with many. If a user only has one pumping system, and it is not necessary to base the one pumping system around existing standards for PLC control and communication. For just one system, a PLC/HMI configuration is probably not the best configuration for the owner/operator.
However, for the entity with many pumping systems seeking to develop long-term standards of operation and control that can grow with them, the PLC/HMI control panel configuration with custom operating code may be just what is needed for current and future operating standards.
Another factor is proximity and the real need for remote control. American sewer collection systems typically involve numerous pumping systems. The command center for the collection system is often the sewer treatment plant. It is helpful and desirable if someone can operate or control all those systems from the treatment plant or from their laptop. The distance from the command center to the furthest pumping system can also be a problem. Not only does it take longer to get there as the water level rises, it is also possible the sewer event could be affecting multiple pumping systems at the same time.
The reality is many entities, who in the past never dreamed of owning a pumping system, now must have one. One example of this is stormwater and stormwater treatment. In many states, any new construction on undisturbed ground now requires stormwater collection and treatment prior to the release of that treated stormwater back to existing water bodies. This requirement often affects individual commercial, industrial and residential development with individual pumping that must be owned and operated by the hotel, truck stop, coffee shop, etc.
In these cases, a simple control panel is a must. In some of these cases, the owner can and/or will attempt to operate and maintain the system themselves. In other cases, they will outsource the operation and maintenance to a local pumping system service company. Regardless, it is almost always best to configure the control and communication to be as simple as possible.
Urban growth, time and the typical common independent civil engineering design methodology has delivered a predictable outcome for those entities who have always had multiple pumping systems. Sewer districts are a good example, as many of the pumping systems were designed by different engineers. Over time, each one brought their own latest and greatest ideas to the system configuration and operation. This approach results in a vast matrix of pumping systems that are often controlled by different proprietary controllers from different vendors. Together, these controllers make it increasingly difficult to evolve the control and communication methodology multiple system owner/operators need.
A solution to this problem is to retrofit or replace all the existing control panels with PLC based systems that can be programmed to operate in a common way. This circumstance is quite common in sewer and stormwater collection districts across the nation. Control and communication systems required for multiple pumping systems are quite different than what is best when someone owns just one.
The owner/operator and their maintenance and operations staff must be the basis by which the control panel and its operations, communication and supervisory control and data acquisition (SCADA) is configured. Remember, a red light flashing and/or an audible alarm may be all the communication one needs. In other cases, for the multisystem operator with a defined command central and limited field staff, the PLC with custom code and wireless communication may be what is best.
There is no doubt millions of sophisticated pumping systems operate in the world today. These systems handle wastewater, stormwater, industrial process water and clean water. Their numbers are increasing and so are the people involved in their operation and maintenance. Most of the easy land that is gravity friendly or not susceptible to flooding, has been built on. Urban growth requires clean water to be delivered at acceptable pressure and for sewer water to be collected and delivered to treatment from further and further away.
There are pumping systems supporting one, two or a few houses and other systems that support thousands. Stormwater treatment is required at sites ranging from general construction to urban shopping, and each of these are controlled by individual control panels that also provide the operators with some sort of communication for their on-site or remote control.
In each case, the choice must be made as to how this system’s control and communication should or must be configured. It is important in this circumstance to think long term. Is this a lone system that is going to be operated by a maintenance staff with no experience in the world of pumping lots of water, or is it for a growing collection system that will always have multiple systems and multiple operators to take care of it?
These questions, considered in the long term, should help anyone faced with these circumstances make reasonable decisions and choices regarding the control and communication of pumping systems.