Second of Six Parts Because of new challenges in sewage transport and handling as described in Part 1 of this series (Pumps & Systems, November 2015, read it here), innovative solutions are needed to address the problem of modern sewage requirements. While pumps that cut or squeeze are often specified for difficult wastewater applications, users must consider the whole process and compare the different methods and options. Experience in drainage pressure systems over many years can indicate that cutter or grinder pumps in large collecting systems may have side effects. Some treatment plants claim that the fouling process is more likely to begin in the pipework if chopping or cutting processes are incorporated. If raw sewage is ground or chopped in the early stages, the loads will consist of small parts and the total surface area will be much larger than before. The organic parts will have this larger contact surface. This phenomenon causes the fouling process to begin in the pipework. Normally, treatment plants must have full control of the processes to recycle sewage. Fouling before treatment may greatly increase odor in the pipes and pumping stations. Biological treatment is a vital part of the process that produces the required water quality of the effluent. However, when substances that are normally filtered out by the screen become smaller, they have a much higher chance of passing through. Also, the specific weight of the materials is not high enough for them to settle down later in the precipitation tank. What happens if non-biological waste makes it to the biological treatment process? If all equipment is well-designed and the processes are running normally, the activated sludge is similar to water but with a brown mass of bacteria. The dry substance content, also called the TS value, may be approximately 2 to 3, while the bacteria may be visible as fine brown substances.
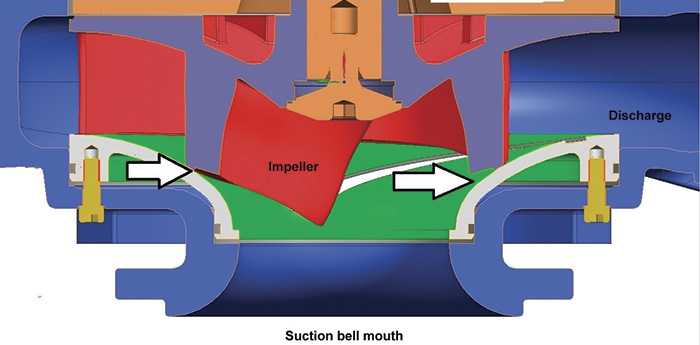
.jpg)
.jpg)
- high wear and tear on blades
- less efficiency from fast wear
- higher lifetime costs because of the need for spare parts
- higher expenses because of special hard materials against the additional wear
- more effort required for adjusting the impeller
- fouling in the pipework
- odor in the wastewater collection system
- small parts of synthetics passing the screen and reaching biological treatment, where the tank cannot get rid of it