Manufacturers of food and beverages, pharmaceuticals or cosmetics use components and make products that are among the most expensive in the world. Significant and immediate cost savings can be achieved by improving the volume of premium end-products and costly materials that are recovered from transfer lines. Given the value at hand, any potential for increased retention and recovery is worthy of exploration. Product waste is always the enemy of profitability, and even more so when the products have high cost. More than $120 billion of product goes to waste worldwide every year, according to the McKinsey Quarterly Food Waste Alliance. The Natural Resources Defense Council (NRDC) has also studied the issue and found that 40 percent of food in the United States is lost during handling and production.
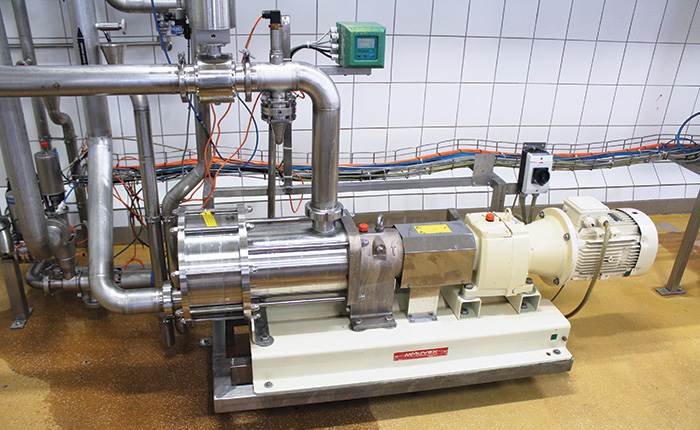
- increased water use for cleaning the lines
- additional cleaning and treatment chemicals to clean the lines
- chemicals to sanitize the lines
- energy to facilitate the cleaning process
- labor costs/hours to perform longer cleaning operations
- disposal costs of used water, chemicals and product
- water treatment costs and associated chemicals
A More Capable Pump
There is a better option. With the right transfer pump installed, manufacturers can recover the bulk of their product from the line and achieve considerable savings with every production cycle. This capability to clear lines varies among pump types. The lobe, external circumferential piston (ECP), twin screw, centrifugal, hose and progressive cavity-style pumps widely used in hygienic manufacturing lack the capability to adequately strip suction or discharge lines.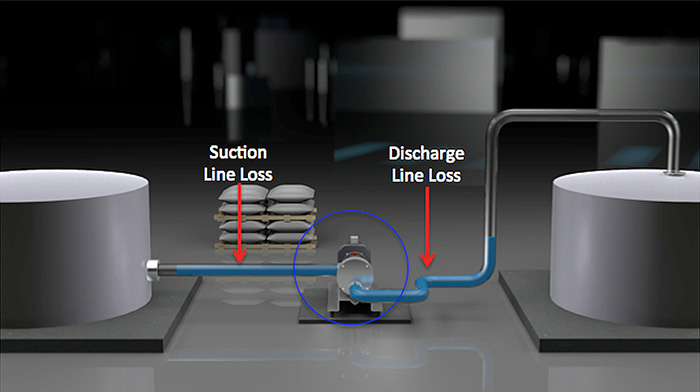
- A high-end cosmetic manufacturer recovered enough silicone-based product to pay back the cost of the pump within days.
- Two global yogurt companies with very long transfer lines recorded increases of 70 percent to 80 percent in product-recovery rates and quickly deployed an additional pump.
- An oral-care company upgraded from centrifugal pumps and quickly achieved the product-recovery targets for its low-viscosity products.
- A pharmaceutical company saved on its process for filling oral medicines, which involves frequent product changeovers.
- A large baked-goods company more effectively recovered the filling used in pastries and prevented the blockage of injection nozzles.
Design Advantage
Strong product recovery is possible with eccentric disc pumps because of their unique design. Each pump employs a disc that moves on an eccentric plane within a circular channel, creating the capability for non-pulsing, low-slip operation with high volumetric consistency. The operation of eccentric disc pumps allows flow rates to vary minimally despite changes in viscosity, temperature, system back-pressure and even component wear. Eccentric disc pumps can operate with such high efficiency that they can pump air when no fluid is present, which creates a vacuum effect on the suction side and a compressor effect on the discharge side of the pump. Once the product runs out in the feed tank, the eccentric disc technology continues to pump air in a very constant, non-abrupt, non-pulsating manner, so that the surface tension on any remaining fluid is not broken. This produces a plug effect, which pushes out the product “plug” as a whole..jpg)
- The pumps can recover product from tank bottoms as well as inlet and outlet lines.
- They can recover product from small lines where pigging is not possible.
- They can recover product through a line outfitted with ordinary valves, heat exchangers, magnetic traps, flow meters and other accessories.
- Product recovery is seamless, as no line interruptions will occur between normal production and the product-recovery phase.
- For the majority of the process, air mixing is not a concern, as most of the product recovered by an eccentric disc pump comes in the form of a product plug with no air mixed in. A simple flow switch can be used to shut down the pump before the air purge reaches the product’s destination.
Limitations of Other Pump Types
Compared to eccentric disc pumps, twin screw, lobe and ECP pumps lack line-cleaning capabilities, and manufacturers often have to use them in conjunction with pigging systems that use a projectile to push out the residual product. While well-installed pigging systems deliver the highest recovery rates, they can only be used in lines that are built without the interruptions of ancillary components, such as heat exchangers, valves, filters and flow meters. Operators must also take great care to ensure that purified compressed gas or air is used to push the pig, which can prove a challenge for maintaining product purity. Twin screw, lobe and ECP pumps also wear constantly, which increases their internal clearances over time, resulting in product slip that reduces flow capacity and volumetric efficiency as operating pressures and fluid viscosities change. These pump types are also designed with two shafts that have to be sealed, which doubles the number of areas where leaks can occur. Twin screw, lobe and ECP pumps are also not dry self-priming and can run dry for only a short period of time unless they have flushed double-mechanical seals. These pumps will also experience diminished performance when handling low-viscosity materials.The Direct Route to Savings
The use of eccentric disc pumps as a cost-saving measure is a breath of fresh air for managers and engineers at hygienic plants, who may have run into a cost-reduction wall. Many operators have pursued pump efficiency for cost savings, but there is very little room to improve motor efficiency with today’s designs.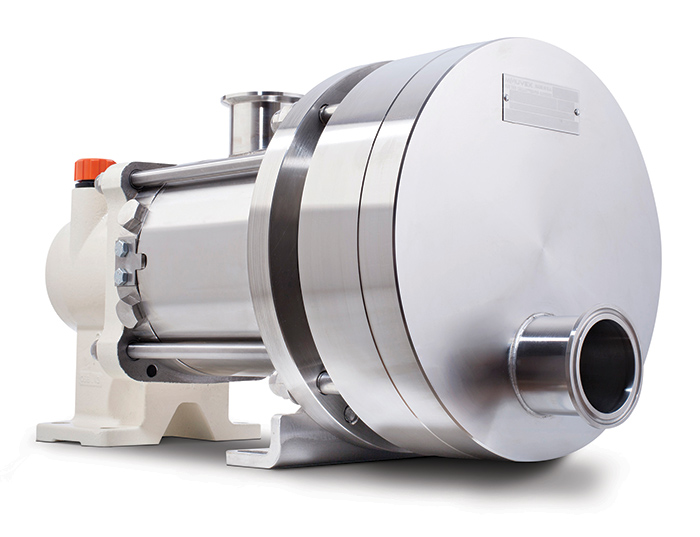
Example System
- Product per foot (2.5-inch line diameter): 0.23 gallons
- Weight per gallon: 8.3 pounds
- Discharge distance: 100 feet
- Total weight: 191 pounds
- Product recovered at 70% rate: 134 pounds
- Price per pound: $1.00
- Cost savings/day: $134
- Cost savings per week (5 days): $670
- Cost savings per month (4 weeks): $2,680
- Cost savings per year (12 months): $32,160