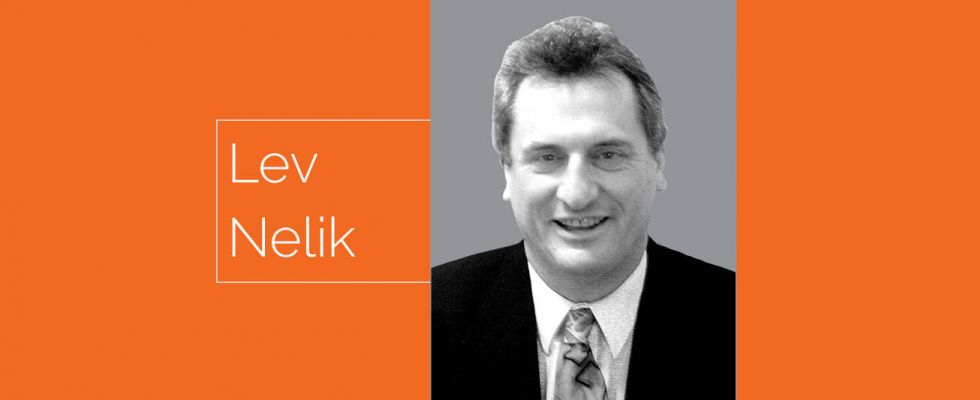
In the November 2021 issue, Part 1 of this column compared various pump types with a look at benefits or deficiencies regarding efficiency (energy savings) and reliability aspects. At first, we reviewed the effect of the number of stages in a vertical turbine pump (VTP) on efficiency and noticed a remarkable difference on a random pick of the same operating conditions (20,000 gallons per minute [gpm], 150 feet) at a given speed. We noticed that a selected speed also has a strong effect, and for a given speed, an increased number of stages (for those particular operating parameters) dropped efficiency from 84% with one stage, to 77% with two stages, to 71% with three stages and to 67% with four stages. The trend would continue if we continued with an increased number of stages. Why?
In Part 1, Image 1 was a reproduction of the Hydraulic Institute (HI) chart of efficiency as a function of flow and specific speed (Ns). Closely examining that chart, we see that at approximately Ns = 2,300, efficiency is at its maximum and drops both below and above this value. There are good hydraulic explanations for that phenomenon, which we will not be addressing now.
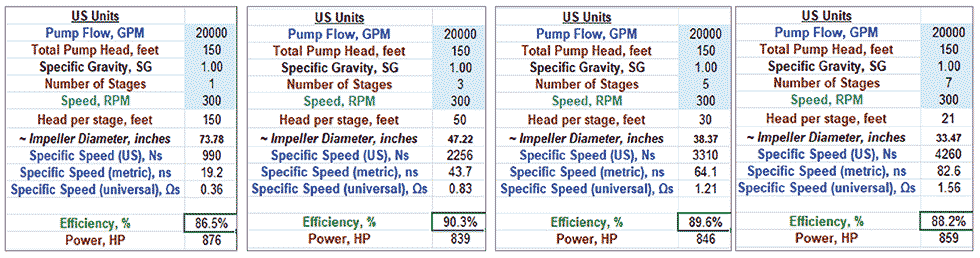
The HI chart has been programmed for a convenient way of calculating efficiency for a given set of conditions, and these charts were also presented in Part 1 for a selected speed of 1,800 rotations per minute (rpm). As an additional example, in Part 1 we investigated the effect of increased speed (3,600 rpm) and saw a difference. We also commented that while such high speed was theoretically possible, the selection of a 1,000-horsepower (hp) motor at 3,600 rpm would likely not be practical, and so we did not play with stage numbers for 3,600 rpm.
Now, let’s swing to another extreme by picking a 300-rpm motor (24 poles)—perhaps somewhat unusual for a 1,000-rpm motor, but let’s see how changing the stage number would affect the efficiency at 300 rpm. From Image 1 (above), we see that efficiency first rises, but then drops after passing through what appears to be an optimum number of around three stages (you can play with the program to more precisely determine if it might be closer to two or four stages).
Another observation is the size of the selected impeller depending on the number of selected stages—obviously, the more stages you choose (for the same flow, head and speed), the smaller the impeller diameter of a stage.
We now see a benefit of selecting a VTP—flexibility of stage number to optimize efficiency and, thus, potentially saving energy costs. An end suction or double suction pump would not give such flexibility in efficiency optimization during a pump selection process for a given desired set of operating conditions.
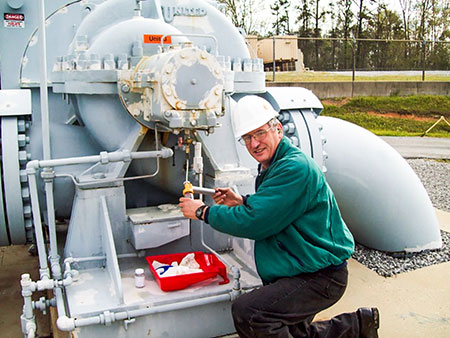
Using the program2, you can optimize your selection for a new application (or review the existing one), to see what the most achievable efficiency for a pump would be for a different number of stages and/or speed.
And so, from these two columns, we can arrive at Pump Selection Rule No. 1: Vertical pumps can have a benefit over other types (single stages) by their ability to achieve higher efficiency during a selection process by varying the number of stages.
In Part 3 of this column, we will swing from efficiency comparison to reliability aspects of VTPs versus double suction pumps.
References
Hydraulic Institute Standards
Vertical Pumps Repair Standard (VPRS): pump-magazine.com/pump_magazine/specifications/specifications.htm
Pump Efficiency Calculator: pump-magazine.com/pump_magazine/pump_magazine.htm