Each situation requires independent and thorough analysis for end users to make an educated decision
Versa-Matic Pumps
02/06/2017
Similar to housing rental markets, industrial rentals have seen a steady rise in recent years. Unpredictable economic conditions, political movements and federal regulations have challenged the housing market as well as the industrial segment, opening opportunities for the rental business in both areas.
.jpg)
1. What is the quantity of pumps considered for rent or purchase?
The first and likely greatest influencer in the decision would be the total cost of ownership of the product. When renting, end users have a lower initial investment, while buying is cheaper over the life of the equipment. End users and managers should ask themselves, “Does the return on investment outweigh the responsibility of maintaining the technology?” The ability to answer this question can be difficult without understanding the number of pumps the facility is utilizing and where they are applied. When researching, there are many points to consider. Keep in mind not only the number of pumps, but also an estimate of the mean time between failure at each installation. This should provide insight as to what the repair will entail and at what frequency.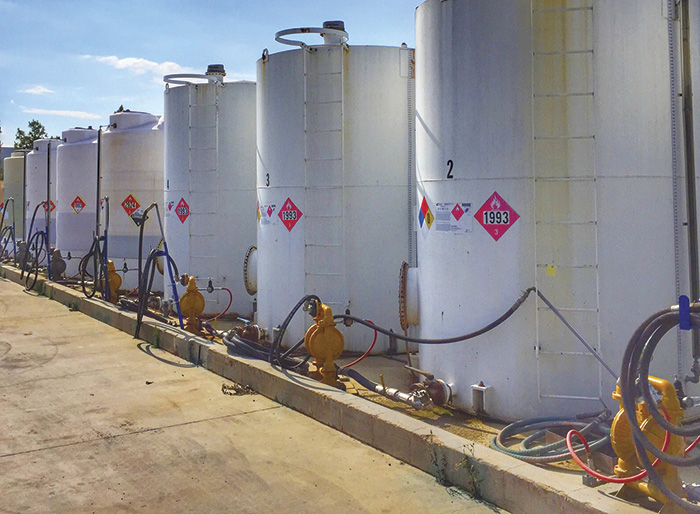