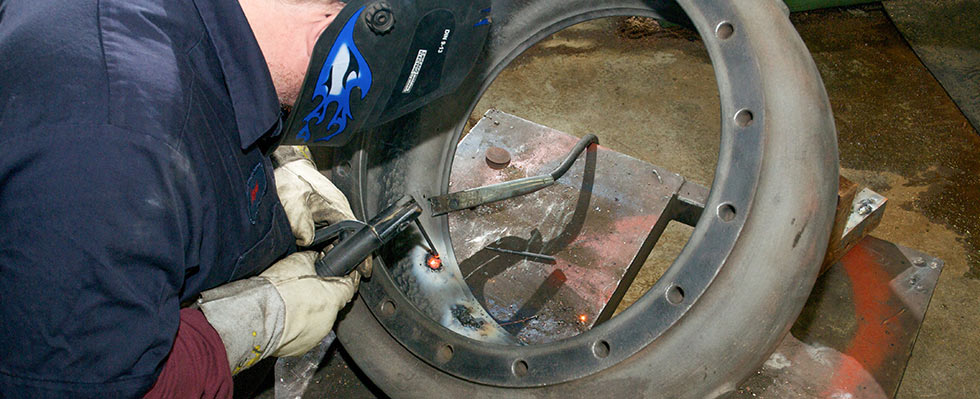
Corrosion and/or erosion damage is inevitable for some applications. Pumps received for repair with major damage may look like a candidate for the junk bin, but with proper repair techniques, they can often be restored to original performance
or better. Damage from corrosion and erosion can occur on stationary pump components as well as on the rotating impeller. Note: Cavitation damage is a form of erosion damage.
1. Coating Repairs
Repairing damage falls in three general categories: coating repairs, machining repairs and welding repairs. Of course, many repairs involve a combination of these three. Of the three approaches, coating repairs are the most direct and often the easiest to implement (Image 2). There are numerous vendors and a variety of products designed specifically for the purpose. Image 1 from the EASA Fundamentals of Pump Repair manual lists just a few of those.
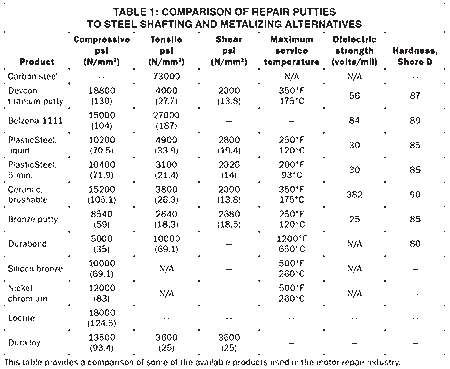
The application of these products varies, and it is important to follow the manufacturer’s instructions exactly. Surface preparation is critical; most products require a clean but rough (sandblasted) surface. Some products specify a “3 mil anchor profile,” which is a rough surface. Surfaces must be thoroughly cleaned of any grease, oil, dirt or contaminants before the final roughing up of the surface. The products that work best for repair of extensive damage are a paste consistency, sometimes referred to as trowelable products. When applying these, it is important to achieve the approximate final finish dimensions. Some products set up extremely hard, too hard for machining, and must be ground to remove product.
For example, a wear ring mounting bore of a split case pump was deeply eroded. Repair metal epoxy was used to fill the void, and the wear ring was inserted with a release agent between it and the epoxy. When the epoxy had cured, the wear ring was released from the epoxy, and the proper fit had been achieved. If the situation is such that machining of the repair metal epoxy will be necessary, select a product that is designed for that use. Of course, carefully mask off any machined surfaces adjacent to the repair area to prevent contact with the repair compound.
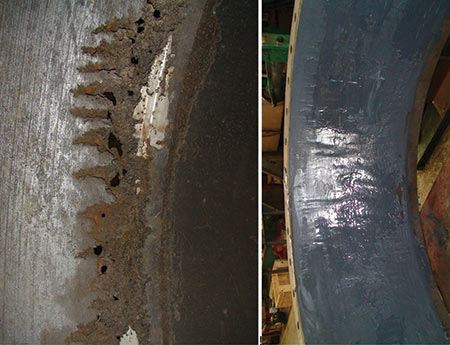
If the pump application dictates that damage is inherent, a hard-top coating can be applied over the base repair to reduce the damage rate in future use. Some applications have benefited from a contrasting color topcoat. Visual inspection with a borescope showed when the topcoat had been penetrated, and repair-recoating was scheduled before more extensive damage to the substrate occurred. Properly applied coatings have the added advantage of providing a slick, low-friction finish. Some compounds, designed with that in mind, will improve the efficiency of the pump.
2. Machining Repairs
Machining repairs are most common when rabbet surfaces have been damaged. Since the alignment of pump components is affected by machining the rabbet surfaces, proper engineering is necessary to ensure the pump goes back together correctly. Of course, maintaining concentricity and perpendicularity of surfaces is essential. In addition, when a rabbet face is machined to remove damage, it alters the axial position of mating and related components.
If the axial position of a bearing, seal, wear ring or other precision component will be affected, it will be necessary to make accommodations to the position of related components, such as adjusting the location of a shoulder on the shaft that locates a bearing. If a vertical turbine pump has impellers mounted with annular shaft keys, machining the rabbet faces of stationary components may require machining a new shaft with adjusted annular key locations.
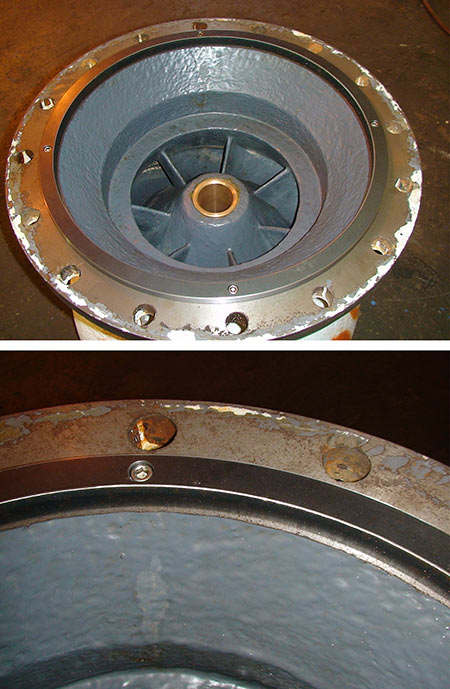
When the inside diameter (ID) or outside diameter (OD) of a critical fit is damaged, a repair ring often must be fabricated to repair the damage. In the common instance of casing or impeller wear rings, it is often possible to machine away the damaged surface and fabricate a new wear ring with an ID or OD to fit the new dimension. If the ID or OD of a rabbet fit must be repaired, it is possible to machine away the damage to the female ID and machine the mating male component to mirror the female ID. A repair ring is then fabricated to fit both new female ID bores. The repair ring can be bolted in place effectively forming a new, male rabbet (Image 3).
When the bore for the stationary element of a mechanical seal is damaged, a bore and sleeve is a common repair. In some instances, the metal repair epoxy method has also been used.
3. Welding Repair
Welding repair (Image 4) is the least desirable method. Cast pump components (impeller and stationary components) can be difficult to weld. A brazed weld may be successful, but the component must be heated evenly, and even then, distortion can result. Significant welding on a component may require reworking all machined surfaces to ensure the effects of distortion are eliminated.
One instance is repair of the mating surfaces of split case pump casings used in common water service. If the mating casing surfaces are damaged, a few thousandths (microns) can be machined off to achieve a new flat surface. To achieve a proper fit after machining, a thicker casing gasket can be fitted to compensate for the removed material. However, this is not a suitable repair for high-energy pumps. Repair of these high-energy pumps is outside the scope of this article.
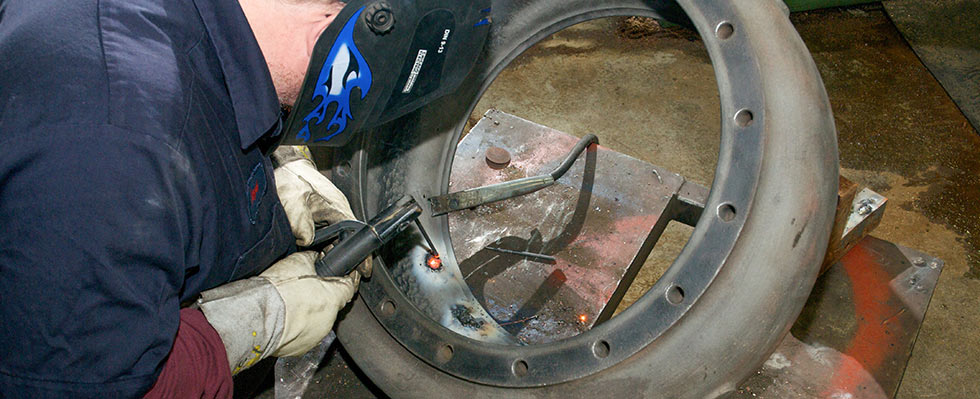
Repairing the corrosion and erosion damage inherent to many pump applications is an important element of pump repair. If damaged surfaces are left unrepaired, damage will progress more rapidly due to the increased turbulence on the rough surface. The methods described here should be helpful in addressing most of the common instances of damage.