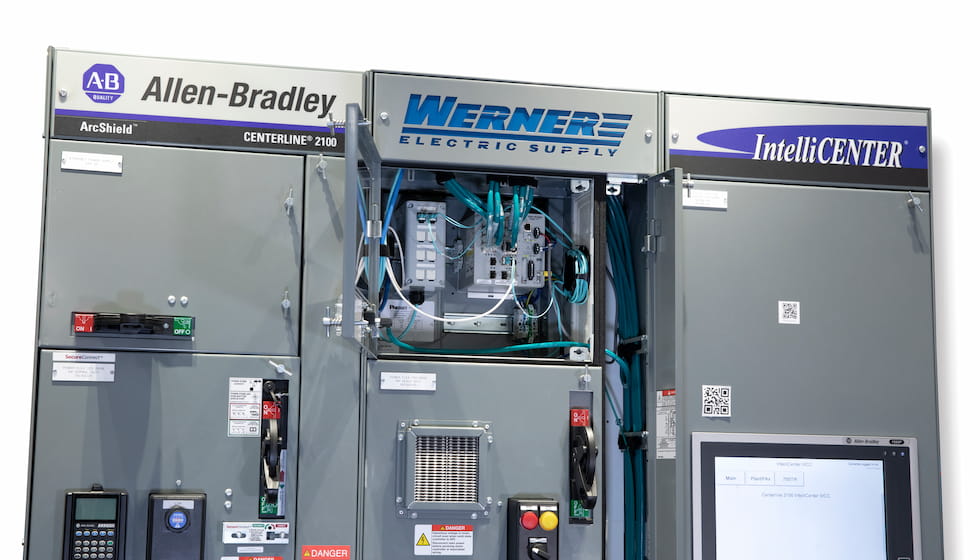
How is the facility’s motor control center (MCC) working? If a facility has been operating with the same MCC for several years, chances are it is missing out on some advances in electrical technology. But that does not mean the whole system needs to be replaced in order to bring the facility up to speed. Retrofitting is one solution.
What Is Retrofitting?
Retrofitting means to add a component or accessory to a piece of equipment that it did not have when originally manufactured. Retrofitting is sometimes an easier and more practical solution to extend the longevity of a machine versus a full replacement of the machine.
For example, an older MCC on a manufacturing plant floor might not be capable of communicating with tablets through the internet of things (IoT). A retrofitted solution could make that machine capable of connecting to the IoT, and users will be able to monitor the machine and make adjustments or provide predictive maintenance before something goes wrong. For this reason, not only can retrofitting be cheaper on the front end, it also saves companies time and money because they can prevent machine shutdowns and plant floor downtime.
With a few well-selected upgrades to the current system, users can incorporate smart technology without the hassle and expense of gutting and rebuilding the entire electrical hub. This allows modernization of legacy components strategically, at a user’s own pace, enjoying the efficiencies of new upgrades while avoiding downtime and future maintenance costs.
Why Upgrade?
First, today’s smart technology does not just work better, it predicts future problems. Many smart units can generate data on how well the parts are functioning, which components may be at risk of overload, and when it is time to consider replacing a piece of the overall system. Think of it like a laptop printer app, which indicates when the ink is running low. With predictive maintenance, parts can be ordered before they are needed—without surprise downtime or an excess of inventory on hand—to help keep the entire operation running smoothly.
Second, newer technology can be more reliable than old machinery, which means it requires less frequent maintenance. Simply by upgrading a few key components of the MCC, the company could be spared thousands of dollars in repair fees and lost productivity.
And third, upgraded technology can be safer. Switching from old drives or machinery to more modern components can prevent safety issues such as worn cables, malfunctioning units, current overload and more.
How to Retrofit the MCC
New technologies have entered the marketplace recently, which make retrofitting a practical option. In fact, an MCC retrofit conversion can make an outdated MCC as capable and reliable as a brand-new MCC. Users can choose which individual buckets to upgrade (drive, starter, overloads, etc.), pull the old piece out and install the new one. Replacing an outdated drive can essentially turn an old MCC into a modern piece of technology.
On average, a drive’s technological life span is about eight years before a design with newer enhancements is developed.
With some industrial drives as old as 30 or more years still in operation, customers have fallen behind in technology and will have a more difficult time migrating to a newer drive. Widespread downtime can accrue if an obsolete drive fails. Because the drive is the “brains” of the motor, an upgrade can introduce advanced functions without replacing parts or other hardware.
With advanced drive power, some technologies allow users to connect a retrofitted MCC to automation and process control systems via an installed Converged Plantwide Ethernet (CPwE) network. This allows remote monitoring of critical assets via cellphone, tablets or laptops. Imagine being able to oversee all vital data, warnings and alerts on the go.
Retrofitting is also a great option for components outside the MCC, such as replacing a DeviceNet or ControlNet cabling with high-performance Ethernet cables. It takes one cable from the new Ethernet-ready component, to the Ethernet switch bucket in the MCC or an external Ethernet switch to connect to the drive without hardwiring.
Ethernet as a whole has undergone massive increases in speed. In the last few years, speeds are reflected at 100 gigabits per second (Gbps) over a 15-meter run. Industrial applications of Ethernet are seeing increases, but at a slower rate with current speeds measuring around 100 megabits per second (Mbps). Ethernet capability can transfer internet data as well as connect to other computer systems within the facility and the IoT.
This makes the control center highly mobile and flexible.
Cost of Retrofitting
Costs vary depending on what components are replaced, but in general, retrofit solutions can save companies approximately half the cost of replacing an entire MCC. Many electrical component manufacturers and distributors offer migration paths, outlining which products users should upgrade to and when, based on the existing technology. This can help with planning and budgeting. Overall, expect upgrades to save users the cost of future maintenance and repairs at the least, as well as cost savings in productivity due to decreased downtime.
More good news is that smart technology is getting less expensive. As smart devices become the norm, these components are more readily available and cost effective.
And retrofitting—rather than a complete MCC overhaul—allows facilities to migrate slowly, pulling and replacing one bucket at a time rather than spending their budget all at once on a capital expenditure.
What Does the Future Hold?
MCC upgrades can provide increased efficiency and cost savings. But there is another reason to upgrade—the workforce is changing.
Today’s young employees are trained on Ethernet technology and other advancements, and their education rarely includes training on older systems such as DeviceNet or ControlNet machines.
That means the veteran workforce holds all of the tribal knowledge of the aging MCC equipment, and those older workers are reaching retirement age. Many companies spend money to delay retirement in order to keep this knowledge in-house. But what will happen when the only people who understand these older systems are no longer working for the company?
Training the younger workforce to maintain older systems is one solution, however, training for this is not readily available.
But retrofitting equipment to handle newer technology is another option. Not only will the entire company benefit from more efficient systems, but there will be an ample pool of workers who understand and can manage the modern technology.
Consider retrofitting to be an investment in not just current productivity, but the company’s future as well.
Options to Retrofit
Talk with an electrical supply partner about options for retrofitting the MCC with updated technology. The solutions are as vast and varied with the company’s needs. A supplier will ask questions such as:
- How will the technology be used?
- What is the existing voltage, current and sizing specs? What do you hope to be able to do with the MCC that it is not capable of doing now?
- Then discuss together how the right upgrades can make the greatest impact for the smartest investment of time and money. Retrofitting is one solution to bridge the gap between old technology and new.