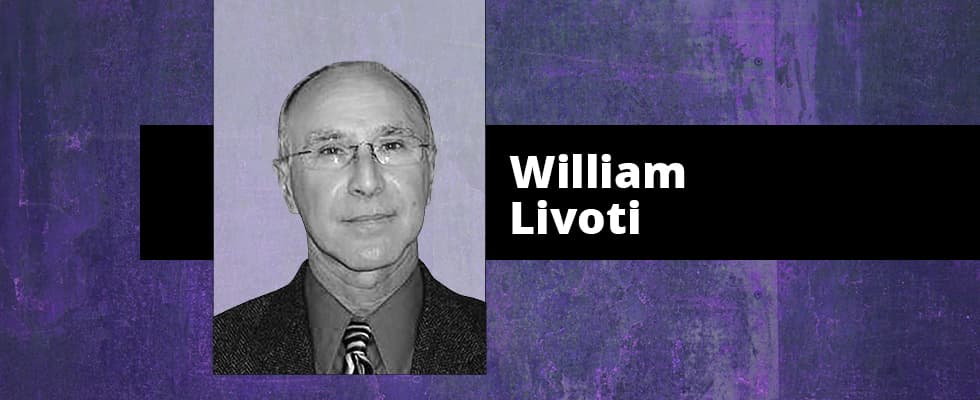
I thought it would be appropriate to write a series of articles on failure analysis since the general scope document (GSD) series that concluded with a case study was an excellent lead-in to root cause failure analysis (RCFA).
Those of you that followed my series of articles on the GSD will appreciate how a solid GSD can mitigate, or at the least, minimize the risk of failures during startup and commissioning of a pumping system, as well as provide optimum reliability.
That being said, for the next 12 issues I will discuss the RCFA process as well as various methodologies for performing
an RCFA.
What Is RCFA?
An RCFA means identifying the source of an equipment or system failure. Let me emphasize source (root cause). Now, let’s muddy the water a bit. There may be multiple sources to said failure—we call these contributing factors, meaning they played a role in the failure.
I’m sure many of you have been involved with a failure analysis at one time or another. My question to you, the reader,
is: Was it a painful process? Was there finger-pointing, arguments or temper
flare-ups? My guess is most likely yes. Could the process have been handled in a more diplomatic, calm or constructive manner? Absolutely.
As I mentioned in the December 2019 article “Case Study,” I’m typically called in to the process when the end user has reached the end of their patience. I’m walking into the proverbial hornet’s nest. This is not a good place to be, but it can be defused if handled correctly. This is another topic or strategy we will cover in this series.
You do not want to wait until the issue—the failure—becomes controversial as the case can be in many situations.
RCFA can be used in a positive, team-building manner if handled correctly and if all parties with a vested interest are willing to work as a team.
Sound familiar?
Teamwork
Again, those of you who followed my GSD series may recall my emphasis on teamwork. RCFA is no exception—teamwork is key. If all parties with a vested interest in the system in question aren’t on board, you will have limited success in determining the root cause.
Here’s the rub, and if I’m stepping on a few toes, so be it. OEMs tend to shy away from liability, so the OEM will most likely say they meet the specification. Engineering firms stick to the scope of the work per the specification (that they wrote). The contractor installs the system based on the engineering firm’s specification. So, where does that leave the end user when the equipment fails?
Have I made my point?
This series of articles will address subject matters that few people are willing to acknowledge—that is, why do new pump systems fail? As an additional topic, we will also discuss RCFA of existing systems.
In Case You Missed It
In the 2019 Pump System Standards column, columnist William Livoti addressed each of the 11 components of a General Scope Document (GSD)—listed at right—in detail. Livoti recommends following this process when preparing a scope document for any project, not just pump systems. For more information about how to prepare and use a GSD, read the entire series at pumpsandsystems.com/generalscopedocument.
1. Purpose and justification of the project
2. Scope description
3. High level project requirements
4. Project boundaries
5. Project strategy
6. Project deliverables
7. Acceptance criteria (owner)
8. Project constraints
9. Project assumptions
10. Cost estimates
11. Cost benefit analysis
Read more Pump System Standards by William Livoti here.