Organic contaminants in water serve as nutrients or shelters for microorganisms. Water disinfection removes or deactivates these contaminants. Water contamination typically comes from human activities. Human waste or pharmaceutical pollutants make their way into water sources through sewers. Industrial process water used by manufacturing, chemical plants, the energy industry and other applications gets discharged back into rivers and streams. Agriculture fosters natural nutrient enhancement, which increases the volume of nitrates and phosphates in water and encourages algae growth. All of these activities bring an array of bacteria, acids, salts, toxic metals, nitrates and suspended sediment into the water supply. Steps to treat water (on both a municipal and industrial level) include screening debris, odor control, filtering sedimentation, pH control, coagulation and flocculation, disinfection and other steps including fluoridation. This article focuses on disinfection, which is primarily accomplished using chemicals such as sodium hypochlorite. It identifies the strengths and weaknesses of the disinfectant, and it highlights some of the challenges that pumping equipment must address to effectively handle sodium hypochlorite.
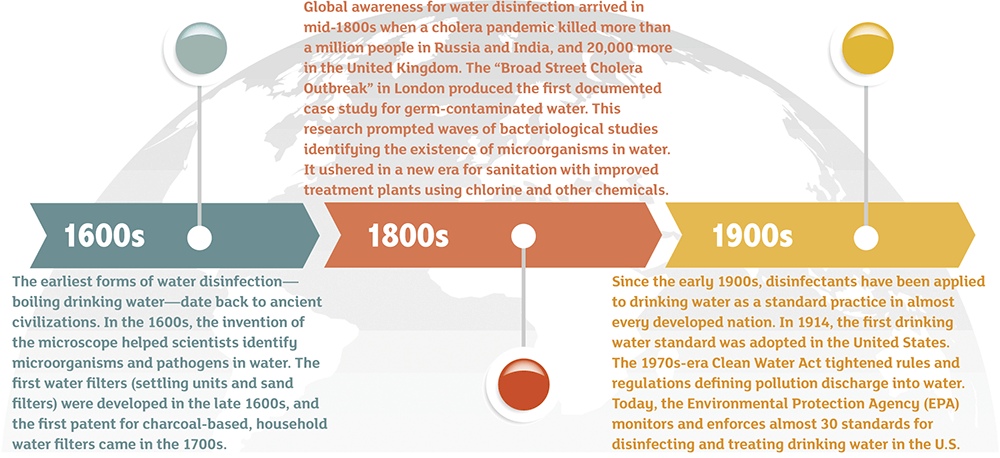
A Look at Sodium Hypochlorite
Discovered in the late 1700s, sodium hypochlorite (NaOCl) is widely used for water purification, odor removal and water disinfection. Among the many alternatives used for water disinfection (hydrogen peroxide, chlorine, bromine and other halogens) NaOCl appears to offer a reliable mix of low cost, ease of use, safety and effectiveness in areas where water is not excessively turbid. It is a clear, slightly yellowish oxidizing agent with a characteristic odor. To kill germs, NaOCl oxidizes molecules in the cells of the bacteria. It breaks down the cell walls of most germs and makes their cells unable to function. When NaOCl dissolves in water, two substances form: hypochlorous acid (HOCl), which plays a role in oxidation, and the hypochlorite ion (OCl-), which is the key to disinfection. The pH, which is an indicator of the acid or alkaline condition of water, is an important variable to control in disinfection processes. The pH is measured on a scale of 0 to 14. Acidic conditions have a pH less than 7. Alkaline (or base) conditions are greater than 7. The pH balance is present when the fluid hits the neutral number for the specific application (and each treatment plant’s applications vary depending on the water being treated). Commonly used chemicals for neutralization include NaOCl, sodium hydroxide, sulfuric acid and sodium bisulfate, among others. The oxidizing aspect of NaOCl generates oxygen bubbles at ambient temperatures. These bubbles can accumulate in pump suction lines and cause a loss of prime, which causes numerous issues including vapor locking in some pumps.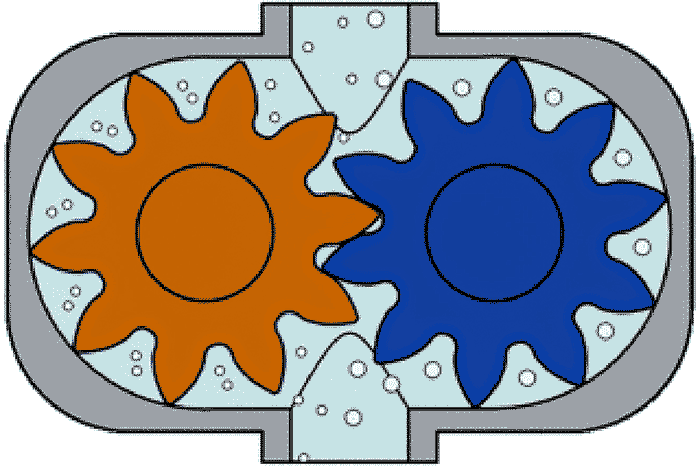
Pumping Requirements for Sodium Hypochlorite
More than 90 percent of water disinfection applications require low pressure pumps, typically in the 30 to 50 psi range. Disinfection applications do not require extreme accuracy, and pumps that can deliver within 2 to 3 percent accuracy are sufficient. Flow ranges for pumps follow the volume of water to be disinfected in the plant, as well as the characteristics of the local water. Typically, a range of 5 to 10 milliliters of NaOCl dosed for every 20 liters of water is sufficient to disinfect disease-causing organisms. Pressure, accuracy and flow capacity do not present unique challenges for sodium hypochlorite applications. The key issue for pumps is the ability to address vapor locking.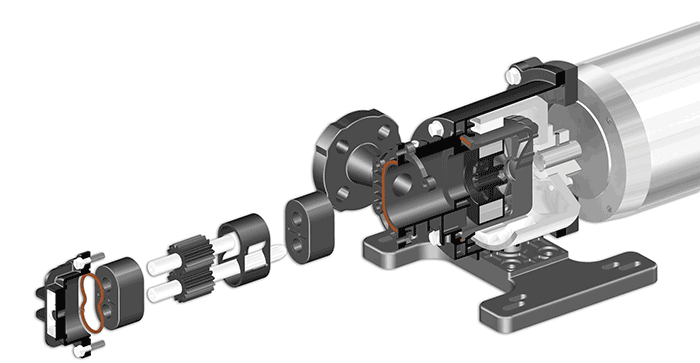
.jpg)
Consider Maintenance Issues
One of the strengths of a rotary gear pump is its simple design. The design seeks to provide reliability over a longer life while balancing the anticipated cost of repairs. Rotary pumps feature sealless designs that are easy to maintain, because there is no leak point for the harsh chemicals, providing safety for people and surrounding equipment. Spare parts should be considered when selecting a pump because it is important to maintain a ready inventory of gears, shafts, O-rings and bearings. When tied to proper design, parts should be easy to install. Self-aligning parts and piloted fits can ensure proper assembly every time. This eliminates mistakes and keeps repair time to a minimum. Municipal and industrial plants can minimize parts changes to every three to five years, on average, when using a properly designed pump. Access to the inner workings of a pump is another important design feature that streamlines maintenance. If the pump’s gears are not readily accessible, then engineers should decouple the motor and remove the pump from the piping at both the suction and discharge ports. But pumps that feature an accessible front pullout design can be repaired in place. This minimizes downtime by eliminating the need to move the pump to the repair shop.The Importance of Safety & Reliability
When used for disinfection, NaOCl is typically metered in concentrations that are 10 to 15 times the strength of household bleach. If a pump leaks during the process, the chemical is harsh enough to corrode parts of the system. It is a pulmonary irritant that can cause respiratory issues for plant workers, and any contact with skin or eyes will cause extreme irritation. NaOCl reacts with flammable compounds, so these characteristics must be kept in mind for usage, transport and storage. When it comes to pumping NaOCl, leaks cause a variety of issues. Beyond worker safety, cleanup efforts on the shop floor are problematic and time-consuming. For pumping infrastructure, reliability is critical, because avoiding plant downtime is paramount. Some environments dosing NaOCl for disinfection (such as refineries or petrochemical plants) require API pumps. For these environments, diaphragm “hypo pumps” offer a safe and highly reliable alternative for NaOCl applications. Peristaltic pumps are on the other end of the price spectrum. Although peristaltic pumps provide a cost-effective option, their design is suited for applications that are less-harsh in nature. To prevent slippage or leaks, a peristaltic pump relies on rollers providing a full and complete squeeze on the hose/tubing. This presents an inherent weakness in the design when it comes to some NaOCl applications because the very thing required (a firm squeeze) to deliver performance is also what ultimately destroys the tube and causes problems for the pump. If peristaltic pumps are used in NaOCl applications, then diligent maintenance schedules must be planned and strictly adhered to. It is not a matter of “if” a hose or tubes fails, but “when” that failure will occur.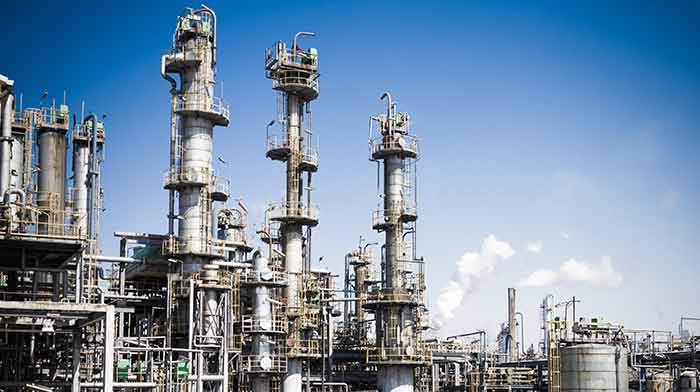
Balance of Functionality & Reliability
There are many reasons why NaOCl is a preferred chemical for disinfection applications. It is highly effective at killing germs and eliminating odors. It can be produced on-site, and it can be safely stored. When it comes to pumping NaOCl, various pump types can do the job, and each design has strengths and weaknesses. When the requirements for NaOCl applications are evaluated consider: the ability to deal with off-gassing- low pressure (30 to 50 psi)
- 2 to 3 percent accuracy
- reliability to eliminate leaks
- construction materials that hold up to the harsh nature of the chemicals
- simple, easy maintenance
- lengthy mean time between maintenance intervals
- total cost of ownership.