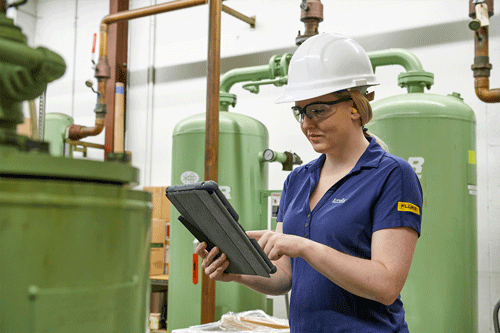
Of all the electricity generated in the world, it is estimated that about half goes into powering motor-driven systems, ranging from pumps and fans to conveyors, compressors and more. That is likely no surprise to those in the manufacturing industry, as motors are often responsible for most of a company’s monthly energy bill.
The good news is that by employing a relatively straightforward motor management policy, users can drastically cut down on energy costs related to running those motors.
The Basics of Motor Management
When considering a new motor purchase, it is important to understand the initial cost pales in comparison to the total electricity cost users will spend to power that motor over its life. In fact, on average, the purchase cost of a motor accounts for just 2% of its total lifetime cost, with energy costs responsible for nearly all the remaining 98%.
Despite the enormous cost of a motor’s energy consumption over time, not all decision makers consider energy costs when making motor maintenance, repair or replacement decisions. That results in both wasted time and money.
There are three main components of a successful motor management policy: purchasing, operations and maintenance and repair and replacement. Here are important things to remember for each.
Purchasing: Develop standardized guidelines for purchasers to review before buying a motor. Beyond considering the specs needed to meet a particular application, these guidelines should consider total asset life cycle cost instead of just initial cost, prequalify reliable retailers and include purchasing spares for motors most critical to the user’s facility’s success.
Operations and maintenance: To ensure motors operate as efficiently as possible, it is important to perform routine preventive maintenance. This includes ensuring proper shaft alignment and lubrication and carrying out vibration analysis and temperature testing. Be sure to prioritize the most mission-critical motors first.
Repair or replace: A successful motor management program sets predefined repair breakpoints that take into account both cost of repair and risk of failure. When identifying a motor issue that requires outside repairs, don’t skimp; use a certified motor repair shop. Users want to be confident in quality repairs that improve motor reliability and reduce costs over the long run. If a user opts for a certified shop, they will also likely receive documentation detailing the motor history and exact repair specifications the shop followed.
No matter which stage of the motor management process a user is in, keeping accurate and complete records will make everyone’s lives easier.
By maintaining detailed records of things like motor failure incidents, motor energy costs and repair histories, users
and their organizations can continually update and improve their motor management policies.
The benefits of employing a comprehensive motor management strategy include increased productivity, less downtime and lower operating and maintenance costs. In addition, when everyone knows what to do if a motor fails, there is less stress, confusion and frustration across the board.
Energy Savings Opportunities
As previously mentioned, when assessing a motor’s total life cycle cost, the upfront cost is trivial compared to the energy costs over time. So, how are potential energy savings opportunities recognized?
An organization may not have the power to negotiate electricity prices, which can range from roughly $0.05 to $0.15 per kilowatt-hour for industrials, depending on the region. However, users do have the ability to improve the efficiency of motors, either by making more informed purchasing decisions or by deploying efficiency improvements, such as variable frequency drives (VFDs).
There are several other measures users can take to ensure they are saving money on energy costs associated with motor usage. These include upgrading older and less efficient motors with newer designs that use modern technology to achieve higher efficiency, as well as making sure to use cogged V-belts on any belt-driven motors.
Right off the bat, users will want to focus on energy-saving measures that require little to no effort and will result in immediate returns. These might include simple preventive maintenance tasks, such as monitoring bearings and ensuring proper lubrication. Once potential areas for improvement are identified, users will want to collect data to back up their proposed plan to others in their organization, perhaps by carrying out a simple payback analysis.
After implementing a change, continue collecting data, as this will reveal how effective the plan was. Whether the results are positive or negative, they will help improve future motor management strategies.
Variable Frequency Drives
Perhaps the most common energy conservation measure related to motors is adding a VFD. These devices connect between the power grid and a motor, enabling a motor to function at both variable speed and variable torque, depending on the task required. In essence, VFDs are used to throttle an electric motor so it only meets the demands of the task at hand, saving energy in the process; however, they are not the right choice in every situation.
VFDs are most valuable when used with motors that use centrifugal loads, such as pumps, blowers and fans. To maximize cost savings related to energy efficiency, users will also want to focus on using them with the largest motors in their facility, as well as those that are running the most hours per year. A good rule of thumb is to consider VFDs for all centrifugal-load motors with operating times greater than 4,000 hours per year.
Another important factor to consider when deciding whether to employ a VFD is the motor’s load cycle profile. Essentially, if a motor is usually operating at near its maximum rated load (from about 80% to 100%), it is likely a poor candidate for a VFD. That is because VFDs require additional energy to power their internal electrical components, so if a motor is operating at near-full capacity, adding a VFD will actually increase your total electricity usage.
Instead, VFDs are better suited for motors with lower load cycle profiles. Motors that operate primarily in the 55% to 85% range are good candidates, but ones that spend most of their time from about 35% to 75% load are even better.
No matter what measures users take to lower the maintenance and energy costs associated with their facility’s motors, establishing a formal motor management strategy is key to success. By prioritizing the efficiency of the most energy-consuming equipment, users not only stand to significantly save on their energy bills, but also ensure motors are performing at their peak for as long as possible, which reduces downtime, decreases costs and increases productivity.