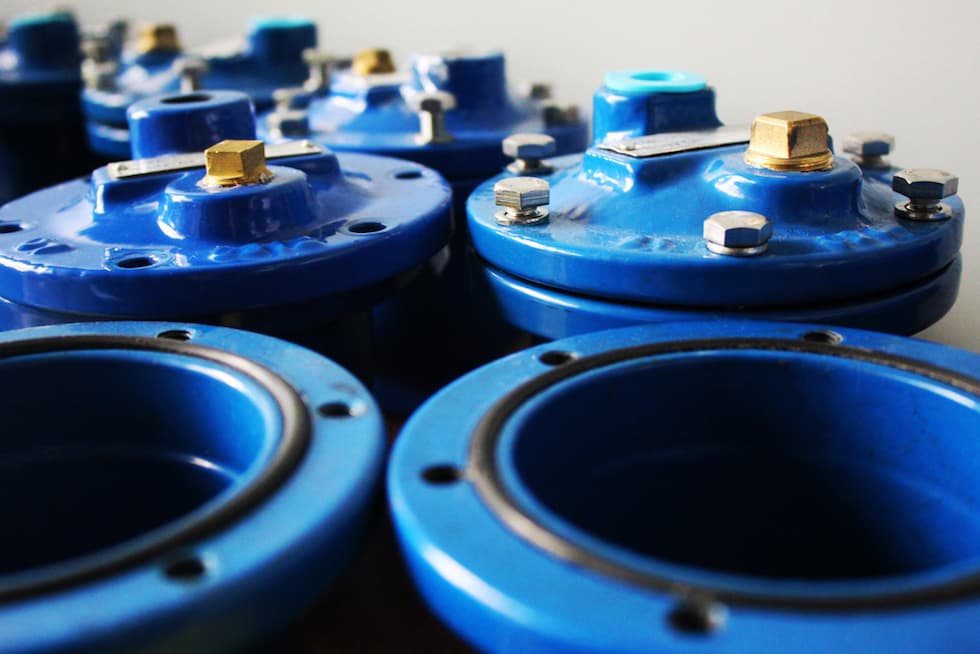
Buna, ethylene propylene diene monomer (EPDM) and Viton are all similar seal materials, but what makes them different? Choosing the right elastomer or polymer material is important for several reasons. While it may not seem like a major decision, the material chosen determines the quality, life span and performance of an application. From snapping to peeling to breaking, a seal material that is a poor fit for an application can lead to many issues down the road. Seal material has a long-term effect on an application’s capabilities.
What Does High Elasticity Mean?
The term high elasticity is known as the ability of an object to return to its shape once it no longer is attached to its source of stress. Rubber compounds represent a wide collection of materials—known as elastomers—which includes base elastomer, vulcanization agents, fillers and plasticizers, with their main feature being high elasticity. Therefore, rubber is widely considered the best seal material. Questions to consider when selecting the seal material for an application include:
- Will this application be exposed to water, oil, gas, harsh chemicals or other materials?
- What are the minimum and maximum temperature resistances?
- What is the required compression strength?
- Will this application be exposed to sunlight for hours at a time?
Whether you are choosing Buna (Nitrile), EPDM or Viton, it is important to compare and consider all key features and benefits.
Buna
When it comes down to abrasive, water and oil resistant and super-strength properties, Buna is a cost-effective elastomer. Buna, also referred to as Nitrile rubber, is commonly known as the industry’s most economical seal material. Buna is well known for its mechanical performance and is a top performer when it comes down to oil-based, petrochemical and chemical applications. The more Nitrile in a polymer means a higher resistance to chemicals, acids and other oils. Buna is widely used in the industry for crude oil, water, various alcohol, silicone grease and hydraulic fluid applications due to its inflexibility.
Buna is comprised of synthetic rubber copolymer that performs well in applications requiring metal adhesion and abrasion-resistant material. This chemical background makes it ideal for sealant applications. Designed with poor acid and mild alkali resistance, Buna can also withstand low temperatures. Buna is limited in extreme factors such as high temperatures, weather, sunlight and steam resistance applications. It is also not suitable with clean-in-place (CIP) sanitizing agents containing acids and peroxides, such as OXONIA.
Key advantages of Buna include:
- affordable
- strong and sturdy elongation
- good for oil and water resistance
- low compression set
- high abrasion resistance
- heavy duty strength
- wide range in temperature resistance
Disadvantages of Nitrile rubber include:
- limited extreme temperature resistance
- poor flame resistance
- not suitable for hydraulic liquids, brake fluids, ketones and acetates
- limited sunlight, weather and ozone resistance
Key applications for Nitrile rubber in the valve industry:
- sealants
- O-rings
- molded products
EPDM
When considering flexibility, strength, weather resistance and the ability to withstand extreme conditions, EPDM is a good option. EPDM is a type of synthetic rubber and a commonly used elastomeric material for automotive, construction and mechanical applications. More expensive than Buna, it can withstand a variety of thermal, weather and mechanical properties because of its long-lasting high tensile strength. It is ideal for applications involving water, chlorine, bleach and other alkaline materials. From waterproofing to HVAC, EPDM is used for a variety of applications because of its resistance to weathering, ozone and deionized water.
With elastic and adhesive properties, once stretched, EPDM returns to its original shape regardless of the temperature. EPDM is not recommended for petroleum oil, fluids, chlorinated hydrocarbon or hydrocarbon solvent applications.
Key advantages of EPDM include:
- wide operational temperature range
- suitable for extreme environments and cold materials
- ozone and sunlight resistant
- good compression set
- tear, abrasion and steam resistance
- high tolerance to sodium hydroxide solutions, diluted acids, ketones and alkalis
- versatile in applications such as HVAC
Disadvantages of EPDM include:
- easy to damage
- poor resistance to petroleum-based fuels
- difficult to adhere to
- incompatible with certain oils or acids
EPDM is used across a wide range of industrial applications, including:
- seals and O-rings
- tubing
- washers
Viton
Viton is the more expensive option, but it is a solution for applications exposed to extreme weather, ozone and chemical degradation. Viton is a long-lasting, high-performance, fluorinated, hydrocarbon rubber product most commonly used in O-Rings and seals. Resistant to ozone, oxidation and extreme weather conditions, including materials such as aliphatic and aromatic hydrocarbons, halogenated fluids and strong acid materials, Viton is one of the more robust fluoroelastomers. Designed to withstand extreme temperatures, Viton seals are the preferred option for the most challenging and demanding sealing needs.
Viton can provide support for a broad range of substances and features and has resistance to high temperatures and resilience capabilities.
Key advantages of Viton include:
- powerful when under pressure
- high-temperature performance
- compatible with chemicals and acids
- retains flexibility and elasticity in high-pressure applications
- excellent for sterilization
- high-heat resistance
- absorbs fluids quickly and efficiently
- longer life span
- environmentally-friendly
Disadvantages of Viton include:
- more expensive than Nitrile
- incompatible with ketones
- not as effective in lower temperatures
Reliable material for:
- O-Ring applications
- pumps and valves
- seal leaks
Choosing the correct polymer is important. While all seal materials are similar, each polymer serves a variety of purposes to meet any specific need.