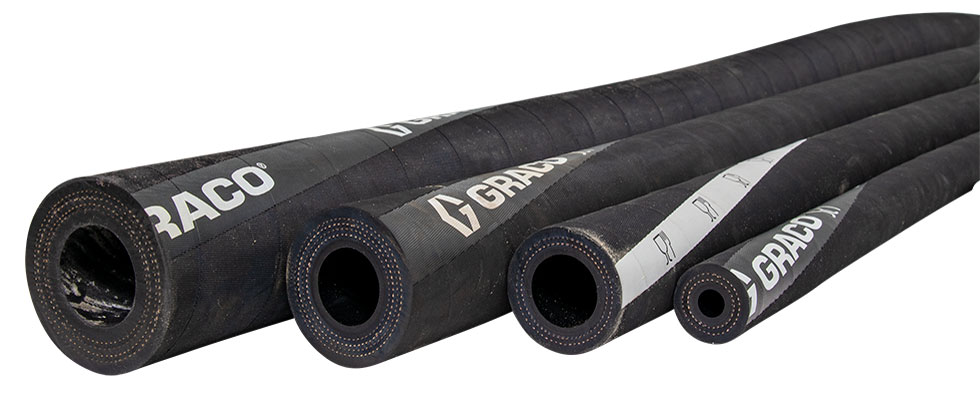
Every pump technology has a role to play in food and beverage, personal care and pharmaceutical processing. Centrifugal pumps provide high-volume transfer at a reasonable price point. Rotary lobe pumps—commonly called positive displacement (PD) pumps—transfer fluids at high-flow rates and high pressures, typically for higher viscosity fluids. Diaphragm pumps handle slurries and solids and are ideal for initial ingredient transfer or difficult ingredients.
A lesser-known technology for hygienic applications is peristaltic hose pumps. Like the pump types listed above, there are specific use cases where peristaltic pumps can improve operational efficiency. Hose pumps provide accurate dosing, are gentle on fluids and can handle particulates.
A peristaltic pump, also known as a hose pump, uses a rotating shoe or roller to squeeze fluid through a hose. These pumps operate on the peristalsis pumping principle: fluid is drawn into the pump and pushed through by compressing and releasing the hose. This pump design provides food processors the ability to improve production processes.
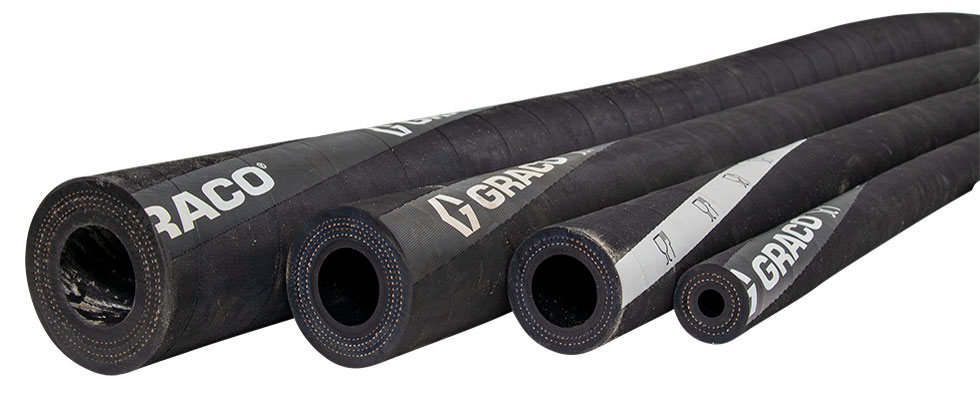
Metering & Dosing
Peristaltic pumps are ideal for accurately delivering a specific amount of fluids to an application. These pumps achieve an accuracy rate of +/- 1%. This is welcome in applications requiring specific amounts of flavorings or ingredients. An example of this comes from the beer, wine and alcohol industry. Today, flavorings are added to alcoholic beverages such as molasses into beer, peanut butter flavoring into whiskey and more.
Traditionally, these flavorings were measured out by hand from a large container to a small container, delivered to the mix and dumped in. This is labor- and time-intensive and relies on an accurate measurement by a laborer.
Solids & Slurries
In many food, beverage and personal care applications, solid or thick slurry-type materials are used. These ingredients can be difficult for other pump technologies to handle. When mechanical seals are used, solids and slurries can cause damage, leading to costly repairs. Peristaltic pumps do not use a check valve, so they can handle these materials well without damaging the product, clogging the process or damaging the pump.
Ice cream manufacturers use a large number of solids and slurry ingredients to add interesting tastes to their product. Fruit pieces, nut pieces, powdered flavorings, peanut butter, candies, etc., are all commonly used and are difficult to handle with other pumps, especially if product integrity is important. Hose pumps can work with these materials and little product degradation occurs during transfer.
Shear Sensitive Materials
Another difficult application in the hygienic space is shear sensitive materials. Most rotary-style pumps impart a large amount of shear on product, which can change the material consistency. This is not acceptable in many recipes in food, personal care or cosmetic manufacturing.
If you shear and damage the fluid, it can change the taste, flavor or consistency of the end product. Eggs and dairy products are examples of ingredients where rotary pumps can froth and shear products with negative outcomes for the end product.
Product shear in a pump typically results from low-efficiency pumps, meaning the ratio of fluid flowing into the pump is greater than the fluid leaving the pump. The longer fluid remains in the pump, the longer it is beat by impellers, diaphragms or shoes. Peristaltic pumps work well with shear-sensitive applications with high efficiency and gentle pumping action.
Sanitary/Hygienic Construction
The largest concern from manufacturers in this industry is material safety. Ensuring a pump meets food safe practices is paramount in deciding on the right pump for the process. Ensuring components do not introduce pathogens, degrade ingredients and can be cleaned are critically important. The pump component that will come into contact most frequently on this pump is the hose. Ensure the pump manufacturer is using hoses that meet government regulations such as U.S. Food & Drug Administration (FDA) and European Commission (EC) 1935. The pump barbs (or connectors) should be made of sanitary material such as stainless steel and should be easily cleaned.
Peristaltic pumps are a reliable technology but some failures do occur, usually at the hose. If a hose fails, the food, beverage, personal care or cosmetic ingredient will come into contact with the lubricant in the pump housing, and the lubricant could be introduced to the rest of the process. Ensure the lubricant used within the pump is food grade, like a glycerin-based lubricant.
Cleanability
Many manufacturers in this space prefer to use clean-in-place (CIP) equipment. CIP cleans equipment faster and is less labor intensive than dismantling and cleaning equipment manually. Peristaltic pumps can be cleaned in place. To ensure a proper CIP, maintenance operators need to ensure they cycle the pump during the cleaning process to allow the cleaning agent to flow through the entire pump. If the pump cannot cycle fast enough to CIP, the users would need to remove the compression on the hose and CIP direct through the pump. Removing the compression removes the only possible flow restriction in the line and allows users to get the velocity required to properly CIP the pump.
Spec & Build a Peristaltic Pump
The first thing to do when building out a peristaltic pump for an application is to determine the chemical compatibility. Check the compatibility of the hose and lubricant against both the pumped media and any cleaning solutions used. Next, select the hose and motor/gearbox size to deliver the required flow rates. Make sure the hose inside diameter is larger than the largest particulate to prevent clogging. Following these steps will ensure long hose life and optimal performance.
Materials with high viscosity and particulates are difficult to pump without degrading the ingredient for many pump technologies. Peristaltic pumps can handle the in-process fluid transfer in the food and beverage, personal care, cosmetic and pharmaceutical industries for metering, when solids and slurries are present or handling shear-sensitive ingredient materials.