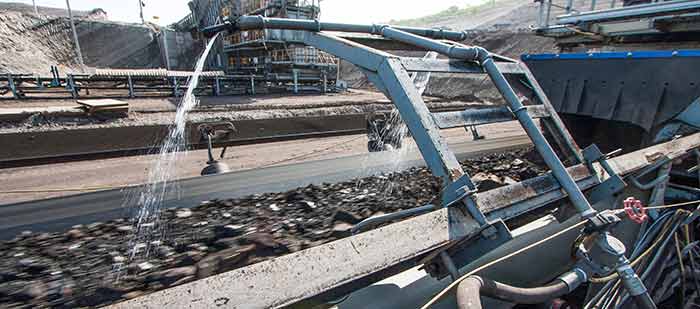
When a foreman calls a company and says, “I need a pump for my mine,” what comes to mind first? What kind of pump does the end user need? Is it slurry, submersible sump, gland water, metering, plant water supply, dewatering, a dust suppression pump or a booster pump? Obviously, there are many pump applications on nearly every mine site, and it will take homework to select the right one. The first question to ask is, “What type of mine is it?” Is it a coal, stone, precious metals mine, or perhaps a sand operation? Second, is it an underground mine, a surface mine or dredging operation? Where is the pumping application located in relation to the mine itself? Once that knowledge is in hand, it is time to focus on the details of the particular application. This, in turn, leads to another set of questions that must be answered in order to provide complete information about each pumping application within the mine.
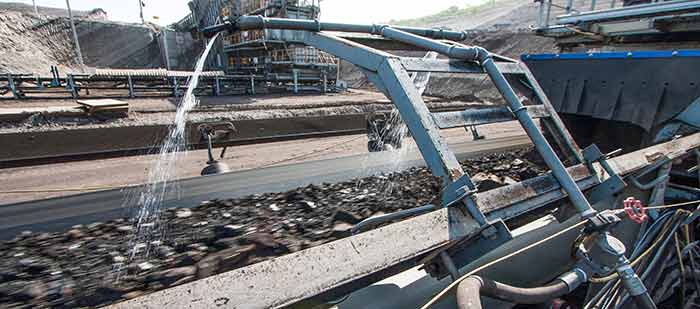
Considerations for Proper Mine Dewatering
This article focuses on mine dewatering. Proper mine dewatering is a critical component to every successful mining operation, regardless of the type of mining that is being done. If the pumps used for dewatering are too small or there is an insufficient number of them, there is a possibility of being flooded out and losing critical equipment and operational time. Conversely, if the selected dewatering pump is too large, the motor could burn on the pump because of too many starts per hour. The motor will not have time to cool off prior to starting again. Also, the pump could experience suction cavitation, which happens when it is starving for water. Either way, the result is costly repairs and/or replacements over time. Some of the most common pumps used for mine dewatering are submersible centrifugal pumps (pump and motor in one unit, all submerged underwater), submersible turbines (pump and motor installed in a well or cooling sleeve and submerged), and vertical turbines, either installed on a float in a pond/lake or in a well (pump end and column pipe submerged with motor mounted on a motor stool above ground/water). Additionally, there are engine-driven centrifugal pumps (mounted on a trailer or skid) or a self-priming centrifugal pump driven by an electric motor. There are pros and cons to each type of pump that must be considered to meet the different requirements for each application. There are several key factors to consider when selecting a pump for mine dewatering. First, determine the static head that needs to be overcome. If the pump cannot produce enough pressure to overcome the vertical distance, the needed flow will not be achieved. Second, what flow is needed to properly remove the amount of water in order to keep the mine dry, and what style of pump is most suited for the application? Would it be a self-priming, submersible or a vertical turbine? If self-priming, what is the length of suction line? This determines the friction loss and the height that can be pulled with a suction lift. The size and type of material of the suction line will need to be identified. The size of the suction line must be equal to or greater than the size of the suction or inlet port. This helps reduce the possibility of suction cavitation. The size, length and type of material of the discharge line must be taken into account, as well. All of these items factor into the total dynamic head, which is an important part of proper pump selection. Another important factor is the consideration of any solids in the water, as this decides what style of impeller and what strainer size to use. Will an agitator be required for the application? The pH of the water will determine the proper material of construction for the pump and seal.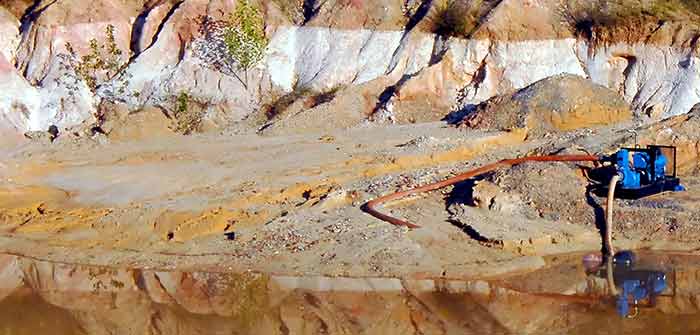