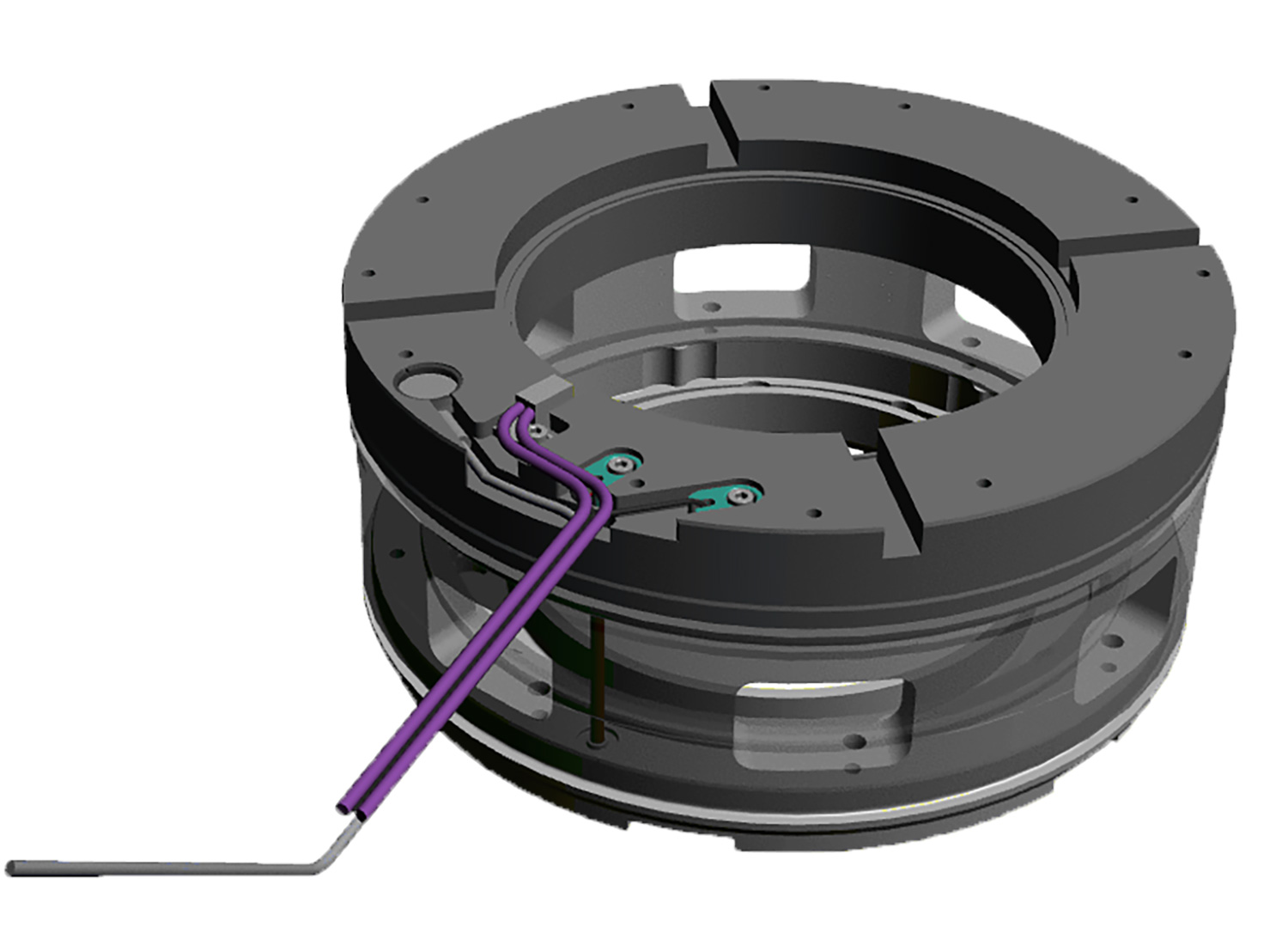
The reliability, performance and efficiency of gas compressors used in liquefied natural gas (LNG) trains have come a long way in recent years. Nonetheless, consistent turbomachinery maintenance and monitoring are needed to ensure LNG train reliability.
If a gas compressor goes down, costly and time-consuming engineering work is required to determine and fix the issue. Minimizing the associated downtime and potential gas flaring are top priorities at an LNG plant. In some cases, a backup train is available to pick up the slack. In others, production is reduced or stopped. In any case, minimizing the impact on the bottom line—millions of dollars per day—depends on quickly getting the LNG train back online.
Issues that affect compressor reliability can happen anywhere throughout the process. Regardless of the origin, those negative conditions can affect the mechanical seal’s health. Until recently, visually checking for seal vent leakage was the primary way LNG plant operators could determine if a seal needed repair or replacement.
The remedy would require technicians to open the compressor casing, remove the seal and send it for repair. Ideally, the maintenance department would have a spare seal on hand. If not, extensive downtime could be expected.
Digital diagnostic technology that provides real-time information on the seal’s health is now available. Sensor data from smart seals can now be combined, processed and uploaded to process control and distributed control systems and sent to cloud servers.
Plant Downtime Issue
An LNG producer in South America was among the early adopters of a sensor-enabled dry gas seal. The company operates a four-train liquefaction facility and is one of the largest exporters of LNG in the world. The plant can produce up to 100,000 cubic meters of LNG per day that is shipped worldwide.
Approximately every six months, excessive compressor vibration or other mechanical issues caused operators to shut down one of the trains to prevent a catastrophic compressor failure. A spare compressor staged to take over the duties during downtime was not feasible due to prohibitive costs and limited available space.
Like most turbomachinery operators, plant technicians relied on checking for seal vent leaks to determine if the seals were contributing to the problem. Vent leakage and traditional forms of monitoring provided some essential health information, but they did not give a complete view of the seal’s health.
While most of the events proved to be unrelated to a seal issue, each shutdown caused up to a week of lost production as the seal was removed and replaced with a spare as a precautionary measure. For example, when compressor vibration approached alarm levels, it was eventually tripped for high seal vent flow. After the compressor was restarted, vibration levels remained high. Even so, plant technicians continued to suspect the seal had been damaged because of these events.
The compressor continued to operate until a turnaround (TAR) was implemented, including a complete compressor inspection. During this planned maintenance cycle, production came to a complete stop. The plant’s electrical and instrumentation team performed compressor maintenance with the unit online but off-loaded (full recycle). The work included rapidly opening and closing a valve and putting the unit through a flow fluctuation between surge and choke. The technicians determined a controller issue caused an increase in speed and suction pressure.
When the compressor casing was opened for inspection, the only visible damage was to a labyrinth seal on one of the compressor stages. This potentially caused scoring and damage to the compressor shaft. The analyses provided the rotating equipment engineer with additional information related to issues with an anti-surge controller. The plant’s technicians did not perform additional data rotodynamic analyses, and the compressor returned to operation without other corrective activities.
Digital Health Monitoring
An engineered technology provider worked with the technical authority for rotating equipment at the facility to extend the compressor mean time between repair (MTBR) and improve the visibility into the dry gas seal’s health. The team installed two smart seals on both the drive and nondrive ends of the compressor.
Leveraging machine learning, the system allowed the operators to assess the health of the compressor’s dry gas seals installed in the turbomachinery and optimize the reliability and performance of the rotating equipment. By understanding the remaining useful life of the mechanical seals, the LNG plant could add months, if not years, to the time before the equipment’s next repair, reducing maintenance costs.
The system included sensors embedded in the dry gas seals, enabling health monitoring. In the event of a high alarm on transmitters (i.e., high leakage flow or vibration), the LNG company could proactively shut down the compressor before further damage occurred and potentially unmask a true root cause of
the problem.
The smart seal’s sensors collect data on conditions that impact seal health using a highly secure, four-step data flow process. The encrypted data from the various sensors is combined, processed and uploaded to the existing control systems and sent to the cloud for real-time processing and archiving. Real-time preset alerts and alarms are also sent to applicable devices.
To diagnose the problem further, the team performed a study of the information and analyses provided by the seals. Upon completing the study, engineers determined the high alarm recorded by the transmitters was not related to premature seal failure, and the recorded vibration did not have an adverse effect on normal seal operation or the seal’s life expectancy.
Millions Saved
The data collected on the conditions of the seals, including seal face contact, temperature and other parameters, allowed the provider to aggregate other data the LNG company collected from its panels. This gave insight into the conditions the seal had been through to provide a better understanding of the seal’s health.
In the end, the data collected from the smart seal showed that despite the vibration observed, there was no face contact or temperature rise, and the seal was functioning properly. When it was confirmed that the issue was not in the seals, it allowed the company to perform a deeper dive into the cause of the problem.
Following the installation, the LNG facility reported that the unplanned maintenance period was reduced by eight days, saving $4 million in lost production time. In addition, intervals between planned maintenance cycles were extended by more than 24 months.