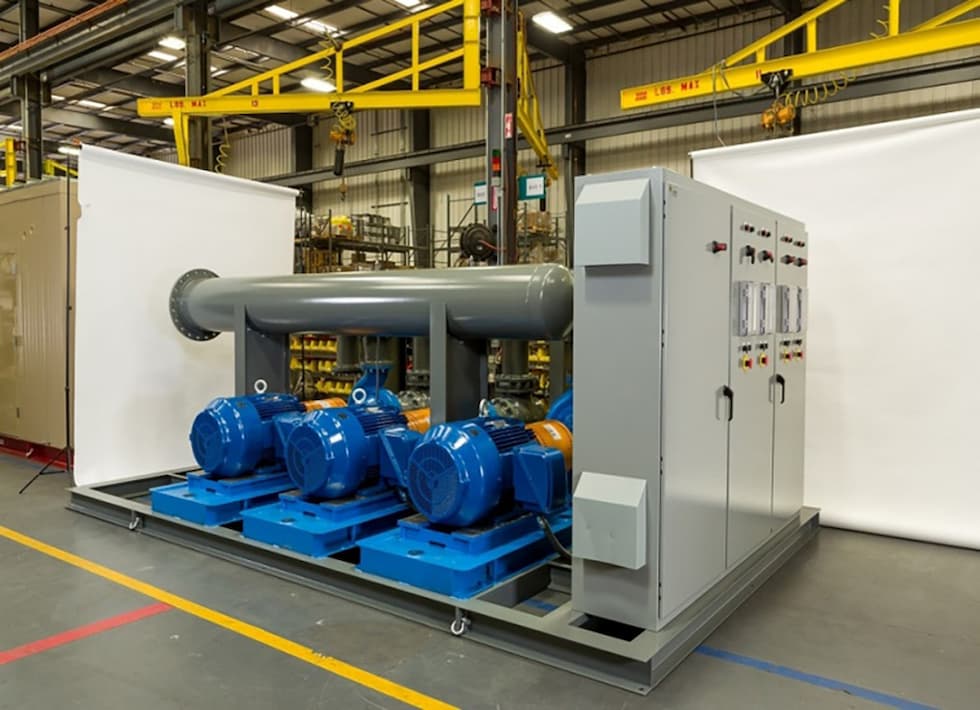
Process improvement is a tricky phrase.
In general, it refers to identifying and improving upon already existing business practices to meet new goals; however, identifying which practices need to be optimized is more complicated.
For industrial facilities, there are many competing priorities at play, ranging from recruitment to profit margins and safety. In today’s landscape, two of the top priorities that come up in discussions with facility managers are sustainability and decreasing costs. Fortunately, there is one practice that can be improved to address both these needs: the operation of fixed-speed pumps.
Historically, the process involved with pumping materials in an industrial facility has been manual and labor-intensive, resulting in a drain on resources and missed potential errors, such as cavitation and dry run. Making matters worse, the cumulative cost of wasting energy and time is nothing compared to the cost needed for repairs to fix bad performing pumps.
That is where variable frequency drives (VFDs) come into play. With the push of a button and input of the desired flow rate and other attributes, VFDs can provide the output needed while running at low energy.
Fixed-Speed Pumping
The most common method of running a pump is straightforward. The operator turns on the pump and sets it to run at full speed. To control the actual output of the pump, the operator will use a control valve on the pump discharge. When the valve is completely open, the result is the maximum possible flow and output; however, the operator can manually close the valve a certain amount to meet the desired output. If the valve is closed by 50%, the resulting flow will be affected at a level dependent on the design of the pump.
This process results in an efficiency loss and can result in serious issues with the pump. There are four problems with this strategy:
- The pump is still running at full speed, no matter how open or closed the control valve is. This means the same power supply is being used when the valve is completely open as when it is 50% closed, which would result in an output decrease of at least that much. This is a major waste of energy and money, and it results in a higher environmental impact. It is like pressing the gas pedal while using the brake to slow a car.
- Using a control valve generates a large pressure drop as the pumping material becomes discharged, which increases wear on nearly every component.
- The process of closing the control valve is analog. Usually, an operator will close the valve while watching the flow rate on the machine. As the flow rate approaches the desired output, the operator will stop closing the valve at the appropriate position. This is dependent on the human eye, and a difference of even 2% in valve position can have a major impact on output.
- Finally, there is no intelligence built into the pump that can locate and identify issues such as dry run, cavitation and dead head, the last of which refers to running a pump with the discharge valve fully closed. If the pump continues to run when these adverse conditions occur, it can result in serious issues and decrease the lifetime of the machine.
These issues can lead to efficiency loss, resulting in decreased pump performance and even failure.
VFDs & Smart Pumping
By varying the speed of the actual motor, VFDs can adjust the speed of the pump, removing the need for a control valve.
Installing a VFD is a simple process. On a standard fixed-speed pump with line voltage running to the motor, the user must make a connection from the line voltage to the drive. While not designed to be installed outdoors, VFDs can be installed in the motor control center and connected to the motor or placed in an enclosure to stay protected from the elements.
Once it is installed, the drive can run immediately. The operator will turn on the pump and determine the desired output, similar to the standard process. However, instead of manually adjusting the control valve, the user can type the desired flow rate, hit the start button and watch the drive do the rest.
In some cases, the drive can also be directed to maintain a minimum amount of discharge pressure. The machine can determine how high the demand is (for example, if there are three tankers waiting at the loading rack versus 10) and adjust the flow rate and the number of pumps being used.
This process has benefits, such as automating specific flow rate to improve overall efficiency. However, one important benefit is the ability to move the facility into smart pumping, a direct solution to issue No. 4 raised earlier.
Smart pumping refers to the ability to understand where the pump is operating to have it operate more efficiently throughout the equipment’s lifetime. It can refer to VFDs, which detect adverse conditions and calculate flow rate without a meter; remote machine health monitoring technology, which can detect vibration and pressure anomalies; and more. For example, cavitation is a serious issue that can cause impeller damage. A VFD would detect that a pump is experiencing cavitation and either slow down or turn off the pump accordingly.
Benefits of VFDs
The upfront cost of a VFD is the most frequent pushback to its implementation, as the price of the drive and installation must be accounted for. However, with a lifetime of multiple decades (up to 30-40 years for smaller drives), the drive can bring a return on investment before the expected lifetime is reached, both in energy savings and increased reliability, which results in less spending on replacement parts.
While organizations increasingly invest resources to improve sustainability initiatives, VFDs provide a simple way to access sustainability gains. It is an even simpler method than recycling. While recycling is important, it requires the participants to change their behavior and separate recyclable products. In comparison, all that is needed with a VFD is a one-time upgrade to reduce energy consumption during each run.
VFDs are another example of a technological improvement to existing processes that can no longer be ignored by industrial facilities. With a one-time payment and installation, plant managers can begin lowering overall energy consumption, improving plant reliability and decreasing wear to improve the lifecycles of essential equipment. By implementing technology that enables smart pumping, such as VFDs and remote machine health monitoring equipment, facilities make it easier for operators to manage output efficiently and future-proof their operations against a variety of adverse pumping conditions.