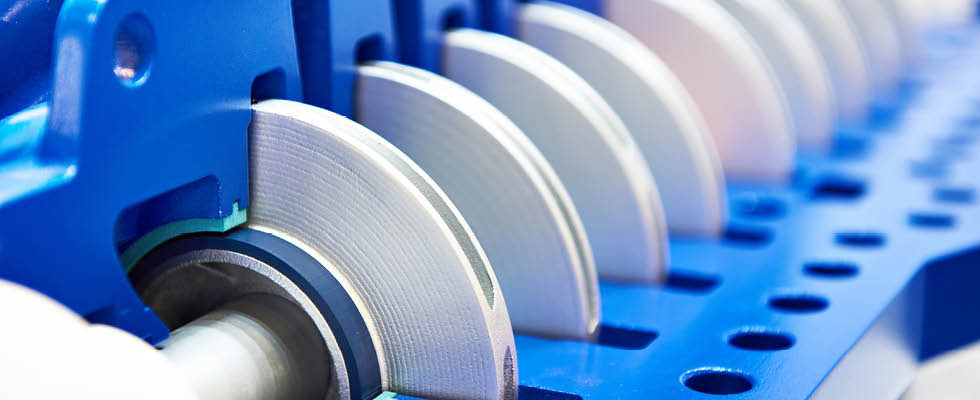
Hydraulic systems in food and beverage processing plants are now ubiquitous. How have H1 hydraulic fluids advanced over the years, and what is their current status in these critical food plant systems?
History of Food-Grade Hydraulic Fluids
Hydraulic systems have been common in food processing plants for decades, but it was not until the early 1980s that consideration and development occurred on true anti-wear, “food-grade” hydraulic fluids. The first of these were developed for fully automated corn cutting machinery, which was brand new to the vegetable processing industry and would be run primarily via hydraulic power. The OEM recognized the potential of system leakage which, if undetected, could pose a risk to consumers.
The governing agency then was the United States Department of Agriculture (USDA), which would designate lubricants approved for incidental food contact as USDA H1. These would be listed in the USDA White Book of nonfood compounds allowed for use in federally inspected processing plants. Achieving this designation was accomplished by formulating with Food and Drug Administration (FDA) approved or generally recognized as safe (GRAS) ingredients and then submitting formulation data, samples and labeling information to the USDA for final approval. USDA H1 accepted lubricants had already been in the market since the early 1960s, but they mostly consisted of white oils, greases and chain lubricants. Most were commonly used in the directly USDA inspected meat and poultry industries. Vegetables typically fall under state inspection programs, so the impetus to use H1 lubricants was driven by consumer safety and liability concerns more than federal regulatory oversight.
The first H1 hydraulic fluids were pharmaceutical white oil mineral oils formulated with recently FDA approved additives for anti-wear and rust and oxidation protection. They performed acceptably in bench tests for industry standard pump wear tests, but there were unforeseen issues in some field applications. The purity of these fluids could, in some instances, cause issues with elastomers. Typical industrial hydraulic fluids are formulated with mineral base oils that contain enough aromatic compounds to keep sensitive seals soft and pliable. Since the development of the new H1 hydraulic oils centered so much around matching industrial fluid pump and system wear protection, little thought was given to the fact that seal swell additives would have to be reintroduced to H1 fluids to regain the seal compatibility found in typical industrial products.
Today, all well formulated H1 approved hydraulic fluids should provide good seal compatibility. In addition, modern seal materials have undergone their own evolution over the last 40 years. The applications for H1 hydraulic fluids today can be generally boiled down to three categories with related types in those categories.
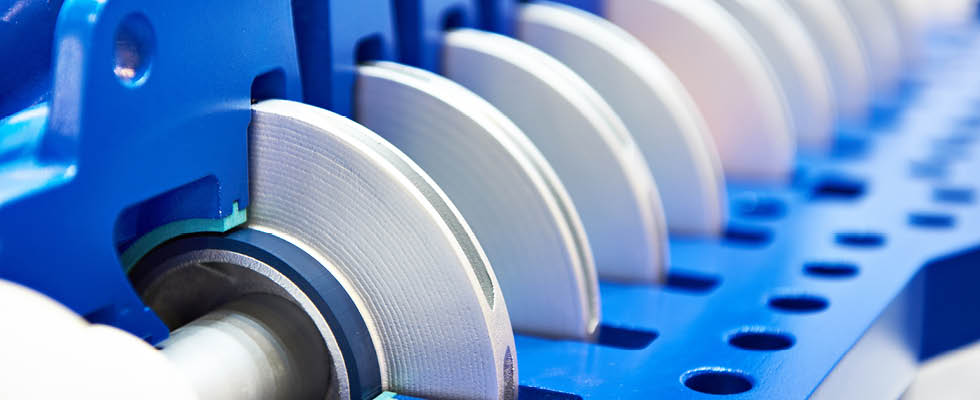
General Ambient Plant Systems
These systems are the load carrying gorillas of the typical plant. The hydraulic power packs can be large and numerous, running most of the major hydraulically operated equipment in the plant. The H1 hydraulic fluids used are primarily white mineral oil based with appropriate additive packages to protect components and comply with the guidelines for H1 approvable ingredients. The typical International Standards Organization (ISO) viscosity grades range from ISO 22 to ISO 100, with common applications using ISO VG 46 or 68 grades.
These systems should operate at best practice fluid temperatures between 120 and 130 F. They will handle higher system temperatures, but fluid life will be shortened as system temperatures rise. Used oil analysis is recommended for all mission critical systems to monitor water content, contaminants, viscosity changes and acid number increases. These are the four primary concerns of fluid condition analysis along with ongoing metals and particle analysis to track hydraulic pump condition.
Low Temperature Ambient Systems
In addition to the considerations given to ambient systems, low temperature systems will face some additional challenges. The main issue will be low temperature fluidity of the H1 fluid. In most of these cases, a mineral oil base solution will be too viscous at startup to run efficiently. There is a risk of pump cavitation and catastrophic failure should the system be starved of fluid while the pumps and motors are running. The solution is to run an H1 synthetic formula, which is usually based upon polyalphaolefin (PAO) synthetic fluids. Although costing three to four times as much, fluids based upon synthetic technology can be paramount in achieving desired cold temp performance.
The designated viscosity grades of these fluids will be typical to the ranges of the mineral based fluids, although synthetic fluids will have pour points 40 to 50 F lower than mineral oil comparable grades. This should be readily observed on the product data sheets in lower pour point temperatures and the higher viscosity index ratings. If there is doubt about the claims made by the lubricant supplier, a comparative pour point analysis done by an independent laboratory is easy and relatively inexpensive.
Properly formulated, these fluids should also provide good elastomer compatibility, but like white oils, PAOs do not contain the aromatic compounds to keep older technology elastomers pliable and must be formulated with performance additives to replace that characteristic.
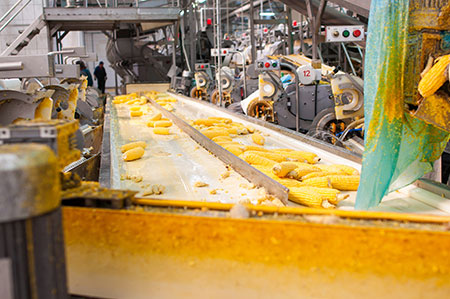
Fire-Resistant Application Systems
The requirement for these fluids stemmed from past, tragic fires in poultry plants where hot hydraulic fluids acted as accelerants and hampered fire mitigation efforts. Since that time, plant safety and insurance regulations have dictated the need for fire-resistant (FR) fluids. The recognized testing entity for approved fluids is FM Global. Fluids that have achieved an FR rating from FM Global are deemed acceptable for use in these plants.
The primary ignition hazards in these facilities are cooking processes at elevated temperatures which could, if exposed to the hydraulic fluids, cause an ignition event.
For many years, the only solution was to use a water-based H1 fluid, typically formulated with a blend of propylene or mixed glycols, thickening agents and deionized water. Although these fluids were safe and are still commonly used, they are difficult to maintain in chemical balance and require constant monitoring, testing and chemical adjusting. In addition, water-based fluids are typically deficient in providing good anti-wear protection for pumps and motors.
In the last 10 years, a new class of ester-based FR products has achieved H1 status. These FR fluids have been used in industrial applications for several decades with good known performance in terms of anti-wear, fluid life and system compatibility. With the advent of H1 versions, many plants can take advantage of the reduced maintenance costs provided by using this technology while still satisfying the FM Global fire-resistant requirements.
Although not compatible with the water glycol solutions, in many instances, the cost of a drain and flush procedure to change to H1 FR ester fluid technology will more than make up for itself in equipment and maintenance costs. A side benefit to most ester-based H1 FR fluids is that many are also classified as readily biodegradable, enhancing sustainability and adhering to environmental safety programs. As in the case of the other fluid classes covered in this article, care must be taken to operate hydraulic systems in optimum sump temperature conditions of 120 to 130 F. All fluids will suffer with shortened fluid life as their operating temperatures increase above this range. Routine laboratory fluid analysis for critical systems is a maintenance manager’s best ally in alerting their team to any impending
issues with their systems.
Additional Information
In most cases, the color of these fluids is water white. This can make leak detection and level sensing more difficult, as the fluid is difficult to see. Some OEMs offer FDA compliant dye solutions, which can either add color or ultraviolet (UV) detection capabilities. These are typically added at the user site.