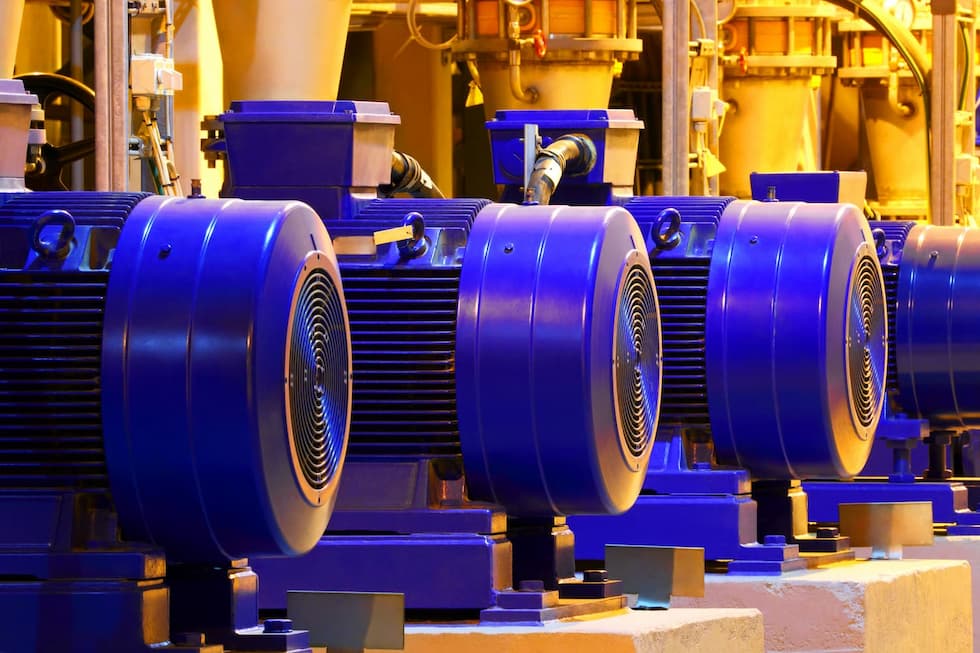
As the year 2021 nears its final quarter, the motors industry has seen some change as it dealt with the COVID-19 pandemic challenges and adjusted to some new trends. Bhavnesh Patel, vice president of business development for Infinitum Electric, recently answered questions in an interview with Pumps & Systems about the state of the motors industry and how it has dealt with the COVID-19 pandemic. Patel wrote this article on 3 Tips for Rethinking Your IoT Strategy in October 2020.
What are the biggest trends we are seeing today in the motors industry?
We’re seeing increased adoption and interest in a new generation of motor that is better for the planet, but also much more reliable and easier to use for pump OEMs.
These new motor designs use lightweight materials and modular design to generate the same power in half the size and weight, at a fraction of the carbon footprint and noise created by conventional motors. This pioneering approach to motors provides increased energy savings, while also improving reliability, productivity and making pump equipment smaller, lighter and quieter.
Motors are also delivering more value to pump manufacturers with integrated variable frequency drives and through more connectivity. Motors that leverage IoT (internet of things) and edge computing can take products into an era of continuous monitoring and control, allowing for the analysis of key operating data to optimize performance and predict potential preventative maintenance before critical failures occur. This significantly helps reduce long-term operating costs.
How has the industry recovered (or has it?) from the COVID-19 pandemic?
Overall the COVID-19 pandemic has not impacted our growth given the demand for more electrification and a lower-carbon economy, as well as the corporate interest in Environment, Social and Governance (ESG). After being introduced in 2020, our company’s motors have gained traction among leading commercial HVAC and industrial suppliers developing new products with environmental sustainability, efficiency and serviceability in mind.
Recently we’ve ramped up production after seeing increased demand in the commercial HVAC and industrial markets, as well as the growing interest from electric vehicle suppliers who see the potential a highly efficient, lightweight motor can deliver.
Analysts also expect the electric motors market in the U.S. to grow by $5.25 billion during 2021-2025, driven by the increase in demand for automated equipment in industrial premises and increasing demand for synchronous motors for energy efficiency.
What are the key standards users need to be aware of in the future?
We work closely with the National Electrical Manufacturers Association (NEMA), an ANSI-accredited standards developing organization made up of business leaders, electrical experts, engineers, scientists and technicians. This year NEMA launched a new strategic initiative called “Beyond Efficiency.” The organization's goal is to promote and advocate for technologies and policies that contribute to resiliency and sustainability, while delivering positive business outcomes for members.
Their vision, which pushes technologists to provide increased energy savings while also improving reliability and productivity, is an exciting and worthy goal for the electrical manufacturing industry as a whole. Their belief is that electrical manufacturers have always been innovators, and it’s time to move beyond efficiency as our next big challenge.
Are we seeing types of equipment or technology being used more these days?
We are seeing industry heavyweights like Rockwell Automation, which invested in Infinitum Electric, and government organizations, such as the U.S. General Services Agency recognize the value of integrated motors and variable frequency drives.
A variable frequency drive (VFD) allows you to control the power going into your motor and more precisely control the performance. VFDs also deliver significant energy savings. For instance, by cutting the speed of a motor in half, you can actually reduce energy by 80% in some applications.
A recent study on pump applications by the Cadeo Group verified the expected energy savings of variable speed systems and estimated energy savings between 19% and 55%, with variation due to workload.
Integrated motors and variable frequency drives can deliver even better performance and efficiency outcomes than separate motors and drives because they are purposely designed and configured to work together. Users do not have to purchase extra equipment and configure or tune them to work together, which significantly reduces costs.
What keeps you up at night?
The urgency and vast potential to help industry reduce its energy footprint with greater and more efficient electrification. Industrial applications consume more energy than any other sector. About 20% consists of electricity. Most of the electricity is used to drive machines that move things, such as pumps, robotic arms, and conveyor belts -- all areas where modern, ultra-high-efficiency motors running at variable speeds can reduce electricity use. With motors that are also easier to manufacture, use and maintain, we can also keep things out of landfills and help the industry make a big impact in cutting emissions and reducing its carbon footprint.