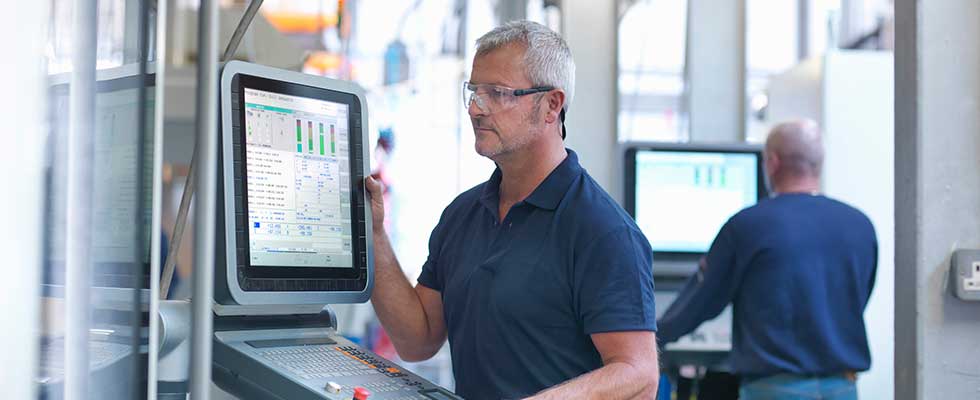
Successfully navigating Industry 4.0 will require maintenance and reliability executives who foster a data-driven mindset. Who will fill these positions? Do you have what it takes?
Being able to leverage and act on data will become the difference between assets reaching life expectancy and those costing organizations mightily in downtime and expenses. Data is now more available and accessible to extend the life of an asset. But only if data-driven leaders step up, champion data gathering, and make the data actionable.
Developing a data-driven mindset and organization is a process—a cultural shift that brings about a mature understanding that data can be transformative. Captured and analyzed effectively, it can drastically improve future equipment maintenance and reliability.
Organizations that recognize they need a leader to base decisions on the data they collect will achieve a crucial step-change all must eventually make.
Data & Machine Health
Actionable data enables better management of asset health, whether the equipment is 30-plus years old or brand new. The industrial internet of things (IIoT) technology enables devices such as sensors to give a voice to assets. The equipment can finally tell maintenance teams, “Hey, I’m not feeling well today.”
For instance, a remote vibration sensor attached to a piece of equipment can detect a change in condition, triggering a notification to be automatically sent to a technician and the maintenance manager alerting them of the issue. Suddenly, we hear the asset telling us about a problem. Instead of reacting chaotically, or not at all, real-time condition monitoring data is enabling maintenance and reliability (M&R) professionals time to plan and act.
Who Is This Data-Driven Leader?
In today’s world, data-driven leaders are not born—they evolve. They may come from anywhere in the M&R ranks, but they have worked with data and recognize the power of it.
The new data-driven leader’s job is to identify and prioritize data. He or she will work uniformly with data scientists and M&R teams to determine how data can be acted on and applied most effectively.
The data-driven leader:
- thinks data first and uses data daily
- understands how technology and data go hand-in-hand
- minimizes cultural gaps
- shares data with everyone
- spends less time looking back
- does not stop thinking about tomorrow
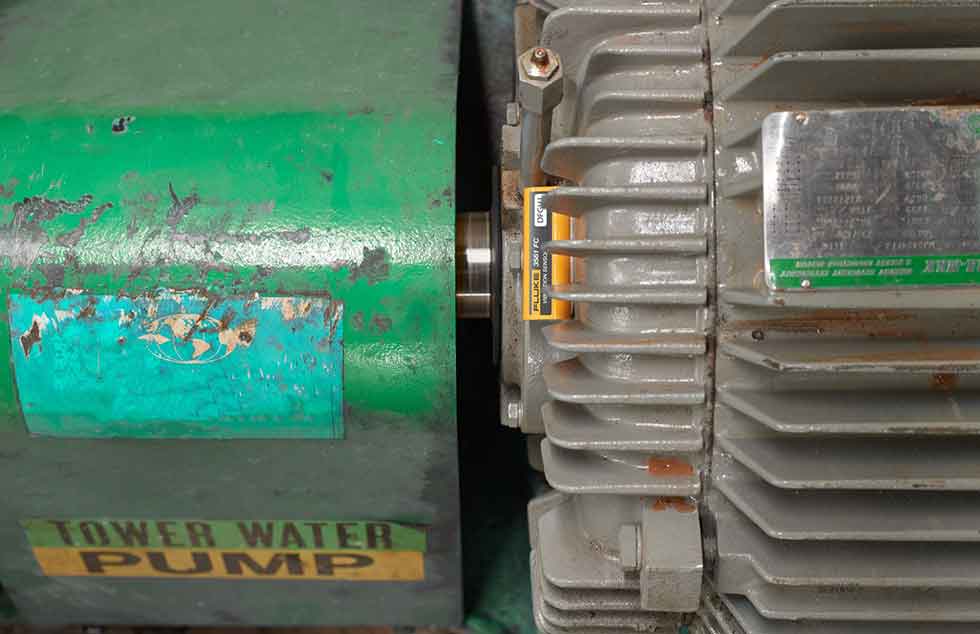
Creating a Data-Driven Organization
The data-driven leader does not sit in an office hoarding the data. He or she makes it visible so that everyone can learn and improve. M&R teams are impacted and buy in. They can see the results of how they kept machines up and running and also where they failed and why.
With each additional data-driven convert—whether it is an engineer, technician or maintenance manager—data begins to infuse itself into the organization. In a data-driven environment, everyone is accountable, but also supported by leadership.
Data Accuracy Is Critical
Unaccounted for spare parts and inventory discrepancies can cost maintenance operations and organizations thousands of dollars each year. The data-driven leader makes teams aware of these oversights and elicits accountability.
Every maintenance member realizes the importance of data integrity. Whether it is presented on a dashboard or in a report, team members know how they can personally affect the bottom line by incorrect or incomplete data.
Here are two examples:
- A technician checks two bearings out of inventory and only uses one but does not return the part back to the shelf. That oversight can bring significant cost to a maintenance operation. A worst-case scenario would be that the asset goes down, and inventory numbers show that the required bearing is not in stock. In fact, it is sitting at the technician’s work station. The asset stays inoperable until the part arrives, causing additional and costly unplanned downtime.
- A fellow technician forgets to track work order hours properly. Instead, he makes a guess, but the guess is wrong. When the maintenance manager compares the technician’s entry to previous completion times, it is clear the hours are off. A cascade of questions and investigations follow, wasting time and money and preventing accurate reporting.
Because mistakes become noticeable in a data-driven environment, team members recognize that they must work hard to avoid omissions.
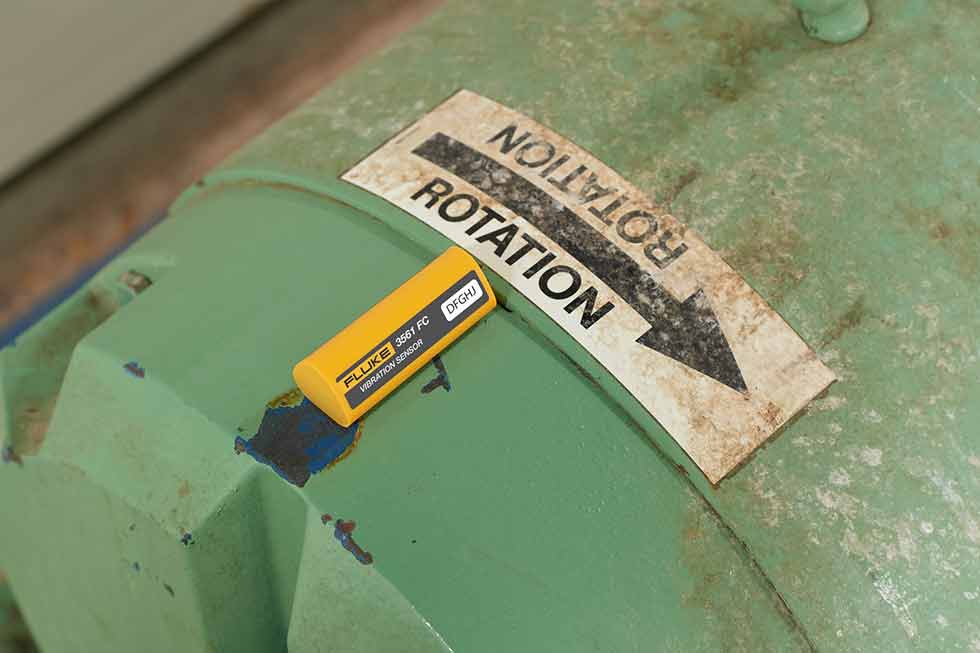
Data Requires Connectivity & People
Maintenance operations that use advanced technologies such as a computerized maintenance management system (CMMS), automation, or condition monitoring sensors are already capturing data that will put them ahead of the curve. To move further ahead, an organization needs to connect the data to the systems and people. A connected framework enables leaders to see a more complete picture of operations, asset performance and overall asset health. Tools for a successful framework include:
1. Comprehensive data capture:
This enables maintenance operations to aggregate data from multiple sources. Data is stored in one central location and can be seen from anywhere using a smart device.
2. End-to-end connectivity:
With systems connected, data can be received, delivered and viewed in seconds. This enables maintenance teams to forecast a potential asset failure early, so they have time to act to prevent it.
3. Empowered teams:
They understand the value of data and how they can negatively or positively affect the organization. They can say, “Because I completed a work order, I helped prevent an asset failure. I did a good job. I positively affected business.”
Data-driven leaders understand that people can make or break an organization’s technological evolution and future.They recognize that humans are an integral part of the framework that drives technology forward and clears the path to connected reliability. 5 Characteristics of a Data-Driven Organization A data-driven leader needs organizational support to fully maximize the benefits and competitive advantages data and new technologies offer. Data-driven organizations that successfully make the transition to technology have several factors in place: * view data as a critical business asset. * enlist data-driven leaders to leverage new technologies. * have effectively accomplished an organization-wide cultural shift to technology. * stay abreast of future technologies and continue to evolve. * provide education and training programs to keep pace with advancing technologies.