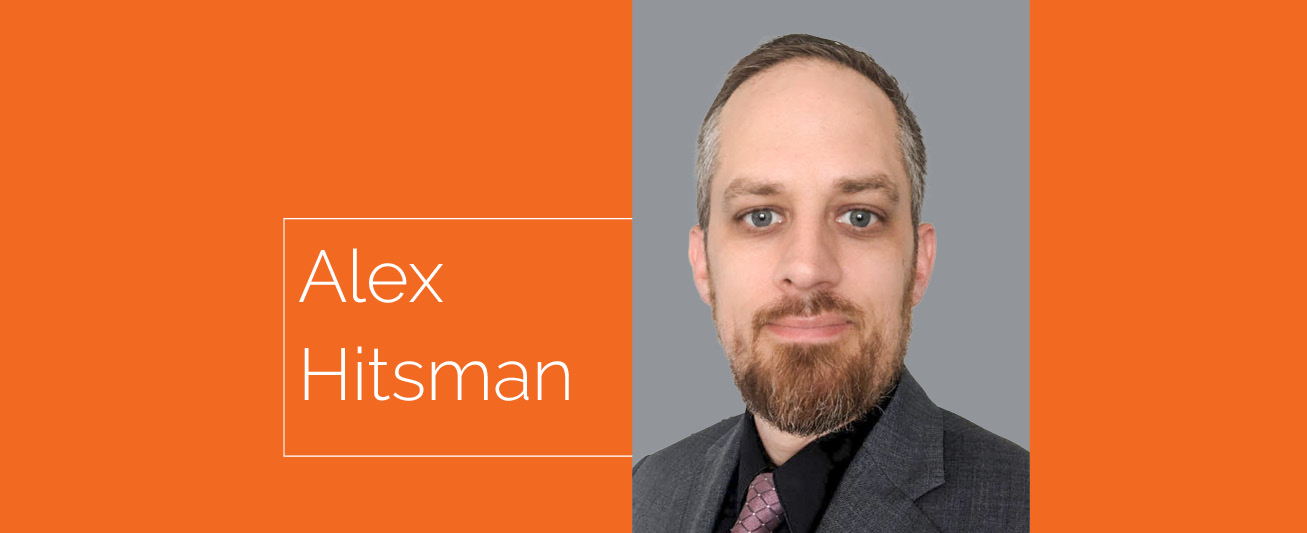
It is common for a pump distributor to receive a call that sounds something like this, “My pump just failed again, how quickly can you get me a new one?” When I receive these calls, I ask if I may come and discuss how many of these problems can be avoided or resolved by following proper installation, operation and maintenance procedures.
Pumps can be prone to various problems that affect their performance and reliability. Some common issues that pumps face include leaks, cavitation, corrosion, wear, vibration, noise and overheating. These issues can lead to reduced efficiency, increased energy consumption, premature failure and costly repairs or replacements.
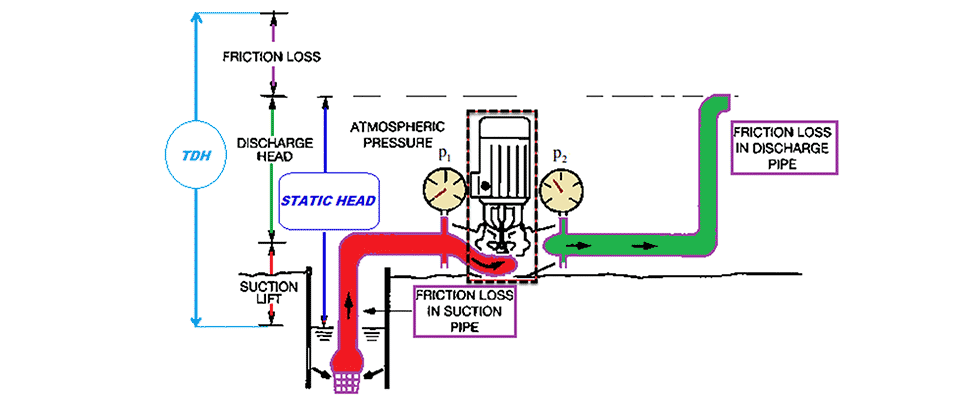
When I first meet with end users to troubleshoot a problem pump, I like to take a moment and explain the reason we primarily see system problems that look like pump problems is that they have the most moving parts and the greatest opportunity for failure.
Standard practices are not always enough to diagnose and fix the root cause of the issue. In such cases, it is necessary to apply a more creative and systematic approach to troubleshooting that goes beyond the obvious and conventional solutions. This approach is what we call troubleshooting outside the box.
Troubleshooting outside the box means putting an imaginary box over the pump, looking at all the other pieces in the system one at a time and asking yourself if they are functioning correctly. By examining each part of the system, we can gain a deeper understanding of the nature and origin of the problem and find the most effective and efficient way to solve it.
One of the benefits of troubleshooting outside the box is that it can help us save time and money by finding and fixing the problem before it escalates or causes further damage. It can also help us improve the performance and reliability of our pumps by eliminating or reducing the factors that contribute to the problem. Moreover, troubleshooting outside the box can help us enhance our skills and knowledge as pump technicians by exposing us to new and different techniques and solutions for troubleshooting.
Some of the principles of troubleshooting outside the box are:
Think holistically: Consider the pump as part of a larger system that includes pipes, valves, fittings, tanks, motors, controllers, sensors, atmospheric pressure, altitude, etc. Any of these components can affect or be affected by the pump problem.
Think analytically: Use logic and reasoning to identify and test possible causes and solutions. Use data and evidence to support your conclusions and decisions.
Think creatively: Explore alternative and unconventional ways to solve the problem. Use your imagination and intuition to generate new ideas and insights.
Think critically: Evaluate the pros and cons of each solution. Consider the
risks and benefits of each action. Choose the best option based on your criteria and goals.
Some of the tools and techniques that can help us troubleshoot outside the box are:
Pressure gauges: These are instruments that measure the pressure of fluids in pipes or vessels. They can help us detect leaks, blockages, restrictions or unbalances in the pump system.
Flow meters: These are devices that measure the rate or volume of fluid flowing through a pipe or channel. They can help us determine if the pump is delivering enough or too much fluid to meet the demand
or specifications.
Thermometers: These are instruments that measure the temperature of fluids or surfaces. They can help us monitor if the pump is overheating or undercooling due to friction, cavitation or other factors.
Vibration analyzers: These are devices that measure the frequency and amplitude of vibrations in machines or structures. They can help us identify if the pump is misaligned, unbalanced, loose, worn or damaged.
Sound meters: These are instruments that measure the intensity or level of sound or noise. They can help us detect if the pump is cavitating, leaking, rubbing or knocking.
To illustrate how troubleshooting outside the box works in practice, here’s an example of how I’ve seen it used to solve some difficult pump problems.
Case Study
A positive displacement pump was experiencing frequent seal failures due to excessive pressure in the system. The pump was failing a seal every three months, and my team was struggling to figure out why. All signs pointed to high pressure, but the system only ran at 25 pounds per square inch (psi). They changed the seal elastomers, seal faces and seal types (component to the cartridge), and it still happened.
After a year and a half of trying everything with the seal, we started looking at the system. This user had supervisory control and data acquisition (SCADA), so we were able to trend the pressure history and found that when one product was running, the programming was wrong. The valve was closing before the filling valve on a tank was opening, causing a short, failure-inducing pressure spike.
Remember, troubleshooting outside the box involves looking for problems in the entire pump system, not just the pump itself. It involves using various tools and instrumentation to detect and measure the symptoms and parameters of the problem. By doing this, you can gain a deeper understanding of the nature or root cause of the issue and find the most effective and efficient way to prevent future failures.