The closed loop differential pump uses linear drives that can offer accuracy in control and reliability.
Voith
08/08/2019
Hydraulics have long been the go-to solution where mechanical advantage is needed and where an appropriate amount of space is available. However, hydraulics pose a number of challenges that users have historically accepted as a trade-off for the relative simplicity of operation and servicing. Some of these challenges have to do with the nature of the hydraulic fluids, the required supporting system components and setup, and the failure modes associated with the systems. To address these issues as well as the growing need to decrease size, improve accuracy and deliver high reliability, a new approach has been created.
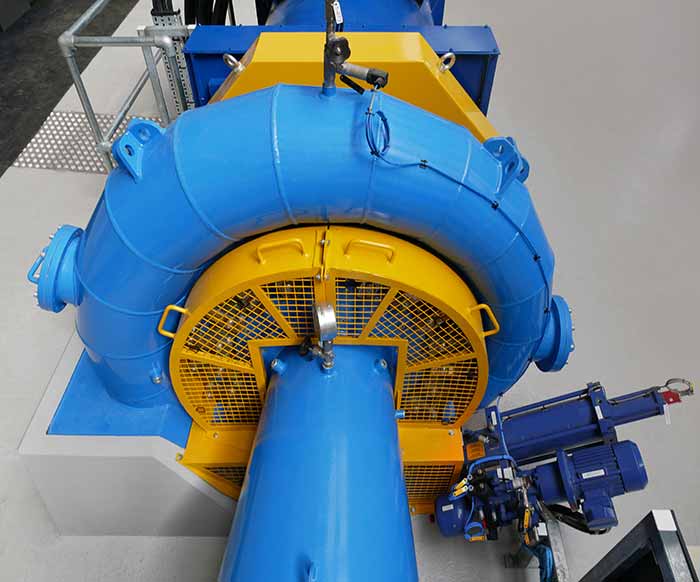
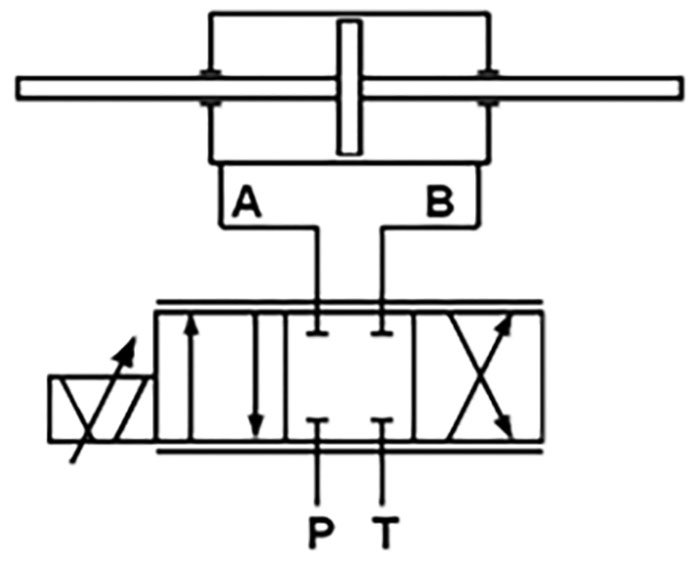
Configurations
Traditionally, turbine governors regulate water on the principle of interconnected valves, and they require large systems that take up valuable plant floor space. Today, a hydraulic axis control typically consists of a cylinder, a servo valve, electronics and a separate hydraulic unit. These components may be considered plug-and-play in terms of the electronics but not plug-and-play with regard to the system, making the installation and commissioning more time-consuming and complex. Using a CLDP, a turbine governor can regulate water flow by adjusting the turbine guide vanes. This design results in a more compact unit. The hydraulic regulation is largely environmentally friendly and energy efficient. The drive unit leverages the principles of a servo-hydraulic linear drive CLDP, which can be successful in a wide range of applications. Due to low wear and long service life in continuous-use applications, this design is also used in sectors such as the food industry, test rigs and laboratory machines.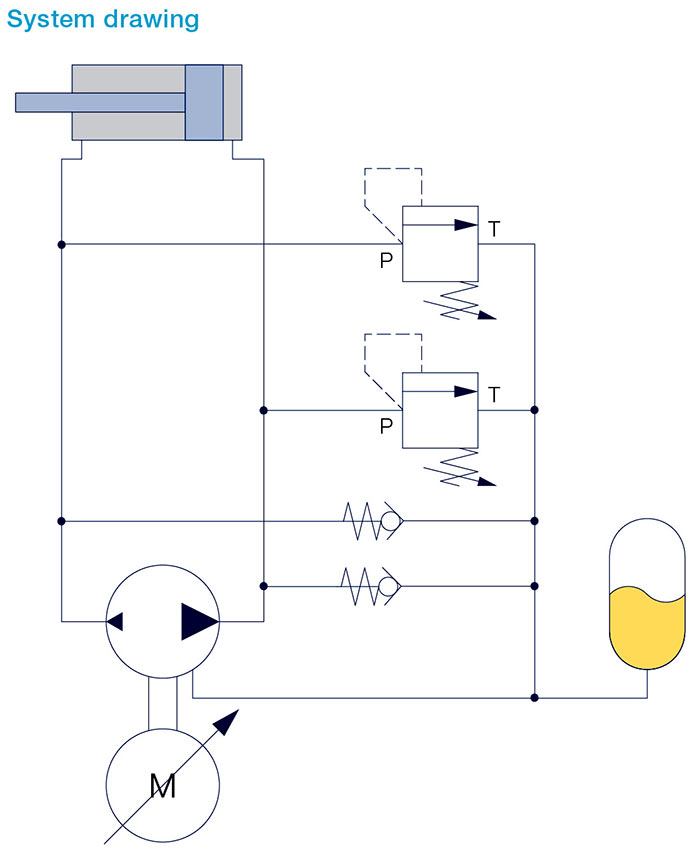
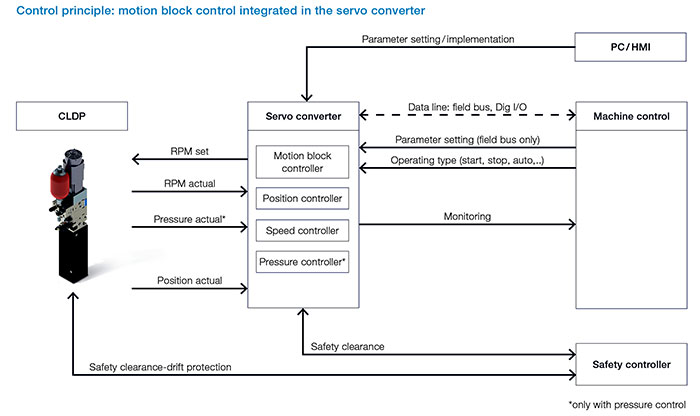
- power density
- flexibility and configurability
- compact size
- energy efficiency
- resiliency
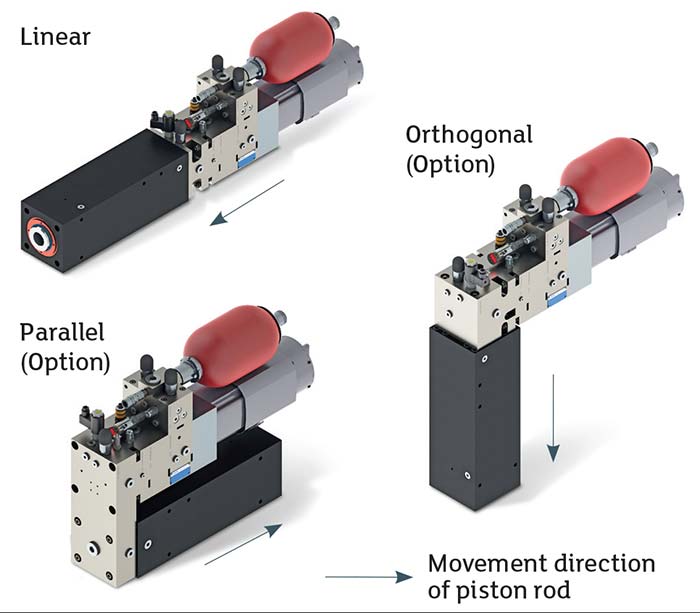
Operation, Safety & Reliability
Depending on the space and configuration of equipment, the CLDP-based equipment can be arranged in a number of ways, as depicted in Image 5 on page 37. One hydropower station on a remote island that has a CLDP-based turbine governor installed offers a capacity of approximately 2 megawatts (MW) and is equipped with two turbines. As part of an extensive upgrade, the power plant installed two new turbines, each fitted with a control unit. The CLDP-based equipment allowed it to be readily integrated into existing systems, even where space was tight. The self-contained system of the autonomous compact drive did not require additional piping, the control unit did not require an additional accumulator and it works with a low volume of hydraulic fluid. These factors allow for safer operation without fluid losses, making it environmentally friendly. Regular checks and inspections could be discontinued. In remote facilities, these features represented cost savings along with enhanced service. The system was preassembled at the manufacturer, so the installation and commissioning at the site was kept to a minimum.Connectivity, Monitoring & Optimization
As part of the CLDP equipment, controllers and sensors are provided for position, pressure and other parameters that provide feedback for proper, accurate and responsive control. Additionally, other sensing equipment can be combined to provide a holistic view of the operation of the equipment both on-site and off-site. This information can provide real-time information, alerts and alarms should any of the equipment begin to trend outside of normal operating condition—indicating a potential issue. When connected for remote monitoring, computing capabilities—such as those in the cloud—can perform advanced analytics, machine learning, predictive algorithms and anomaly detection, providing information about the current operation and potential set points or remedies for improved efficiencies or to avert catastrophic failures. Ultimately, information from the turbine governor and other systems can provide a comprehensive operational picture for the facility or enterprise and enable options to more automatically shift loads, adjust to market demands and provide greater insights.Conclusion
Some possible additional benefits of the CLDP-based approach include:- flexibility for conversion ratios
- functionality like a wear-free gearbox
- precision-improved accuracy and control
- overload protection
- integration of the volume compensator