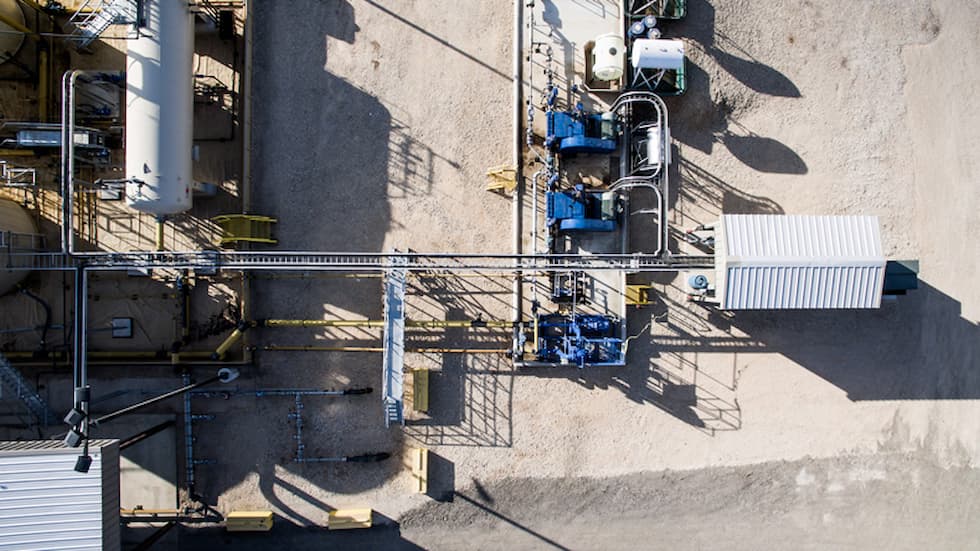
Automation, control and monitoring solutions for pumps have been available for decades. The technology and value provided today far exceed what was available even 20 years ago, yet many oil and gas producers have been resistant to advanced digital solutions.
Hard-wired supervisory control and data acquisition (SCADA) systems have been around since the 1970s, while wireless and remote technology accessed by cellular modems came about in the early 2000s. By the mid-2000s, remote and advanced control technology was available for production well sites. Operators, however, have not prioritized these solutions. Remote capabilities have become second nature in other industries, especially in business to consumer markets—such as smart home devices and self-driving cars. Automation, control and monitoring solutions can offer similar value to operators, however, the lag in the industry is a real challenge to overcome. But there is hope.
Industry Adoption
This shift would not take anything away from operators. An ever-increasing number of production well sites means there are fewer people for more operations, and there will always be an abundance of tasks to perform. Operators are working on profitability goals with fewer people than ever seen before in the industry. Five to 10 years ago, a production or field engineer may have overseen 20 to 30 wells. This same person may be managing up to 100 wells in today’s resource-constrained environment. Greater efficiency is needed to manage the increased workload.
The evolving market strives to help operators manage tasks and run businesses more efficiently. With integrated remote capabilities for pumping systems comes increased visibility and notifications, informing and empowering users to make adjustments on the fly. This facilitates the overall improvement of their equipment and overall production site processes. Despite this, the market has not fully allowed users to change their philosophy and invest in this technology.
In some ways, the industry is more open to automation, control and monitoring; still, challenges associated with such an industry-wide mindset change exist.
These include budget and planning challenges, operation in remote locations with harsh environments, and leadership not native to digital technology. And younger generations, who are often digital natives, not only desire but expect the added benefits of the latest digital advancements.
As oil prices rise, the industry is witnessing financial gains. At the same time, there has been brain drain from early retirements and attrition. However, automation, control and digital solutions can make up for the lost knowledge and expertise of those who have left the industry. This practical knowledge can feed the automation and control systems to develop parameters to support industry leaders.
Quick Wins & Long-Term Advantages
Once users introduce automation, control and monitoring into their pumping systems, they can experience both immediate and long-term advantages.
For example, without full visibility into their system performance, operators could be making decisions blindly, spending valuable time investigating and troubleshooting without critical information. Monitoring can help to solve this dilemma. Added control can also bring safety benefits with fewer people at the well site, vehicle and insurance costs decrease due to operators not having to drive from site to site, and reaction time is diminished so that processes can continue on time.
If failures can be accurately predicted on production sites through analytics, there could be environmental advantages that would improve sustainability efforts. Remote visibility and autonomous systems allow users to run systems at more efficient energy levels, which is better for operational costs and emissions management, making them environmental, social and governance (ESG) friendly. If users monitor equipment health, various operational challenges that could impair production or even damage the environment can be prevented. Inventory and uptime can be improved as unforeseen incidents are eliminated and every step of operations is predicted.
For example, a user was running their progressive cavity pump too fast, which was drawing the fluid level down at a high rate. A digital solutions provider was able to visualize the issue and automatically adjust to regulate the pressure. Using a variable frequency drive pump controller and monitoring technology, the provider saved the user the cost of a new pump, kept the well running and production continued.
An Evolving Market & the Future of Pump Packages
The future of oil and gas production will vary by operator and geography. However, as millennials continue to advance in their roles, they will expect a connected well site. While fully autonomous production is not something that will have widespread adoption anytime soon, there are expectations to see prototypes and pilots within the next 20 years.
The value of integrated remote capabilities for pumps is quantifiable today. A cost-benefit analysis can be performed at a well site to understand how a user’s bottom line would benefit from introducing new automation and control technology.
Users can prevent shutdowns and provide alerts when preventative maintenance is needed. What cannot be seen cannot be fixed, and the better processes are understood, the better they become.