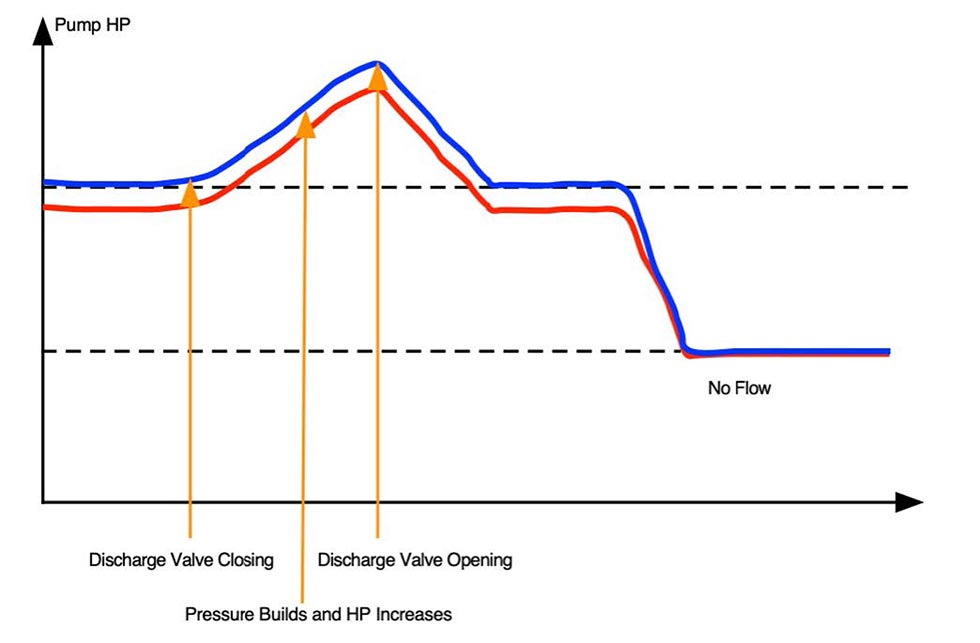
Smart pump managers have long known the benefits of power sensing for protecting their investment. Power sensors can be fast, economical, maintenance-free and provide feedback on the status of production.
The ability to monitor power gives insight into changes in pumping workloads; unexpected variations in power can trigger shutdowns before expensive overheating, impeller breakage and spillage can occur.
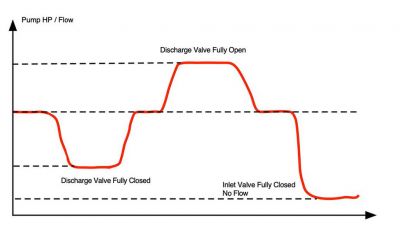
Two benefits of monitoring power are the ability to improve predictive maintenance programs and track power consumption. These two factors are among the largest expenses of owning and operating pumps.
The global market for pumps is more than $60 billion and is expected to continue growing 6 percent into the future. This investment is exceeded by budgets for running and maintaining these pumps over time. Pumps used for industrial applications represent one of the world’s largest consumers of electrical power.
According to the Hydraulic Institute, pumping systems account for 20 to 25 percent of the energy usage in industrial plant operations. Similarly, studies have shown that preventative maintenance may run more than 30 percent of the total cost of pump ownership.
By viewing power data over time, users can glean important insights into efficiency and looming maintenance concerns.
Capturing this data and viewing it analytically can indicate efficiency concerns such as bearing wear, shaft misalignment and increased energy bills. This article will cover how power measurement works, the impact on predictive maintenance, energy efficiency and how to get started putting this information to work for an operation.
How Power Monitoring Works
At the heart of nearly all industrial pumps are three-phase induction motors. The three-phase power creates a rotating field in the stator which induces the rotor to rotate. To measure three-phase power, use the formula in Equation 1.
Power Factor
Let’s explain the role of power factor in Equation 1. Think of power factor as electrical inefficiency: current is flowing to the induction motor to charge the magnetic portion of the circuit, but it is not doing useful work. For a lightly loaded pump motor, the power factor can be as low as 0.1. As the load increases, the power factor improves and is typically 0.9 for a fully loaded motor. Using current alone will lead to potentially misleading results, and the inability to discern differences between light loads, dry running and cavitation.
The benefit of this formula is that a user can draw a straight line between work the pumps are performing and the power required. Image 1 shows a typical centrifugal pump’s power curve through a production cycle, and two error conditions when discharge is blocked and dry running. Pump power horsepower (hp) requirements will increase with an increasing delivered flow rate.
Preventative Maintenance Insights
Knowing this power cycle allows pumps to be rapidly shut down if error conditions are encountered. But this curve can also be monitored over time.
Bearing wear, shaft misalignment and other potential maintenance requirements affect the pump hp level proportionally. The more power the pump will pull to accomplish the same amount of work, the higher the measured hp. Valve conditions will behave as previously illustrated, but the entire curve will be offset by the change in power measured due to the maintenance concern, as shown in Image 2 in blue.
Monitoring the vertical shift over time showing the increase in hp can provide insight into process efficiency and the potential need for proactive maintenance.
Monitoring Energy Consumption
Image 3 shows a positive displacement pump power curve. With the discharge valve starting to close, the hp starts to increase with pressure in the pump. When the valve again opens, the hp drops back down to the normal pumping power.
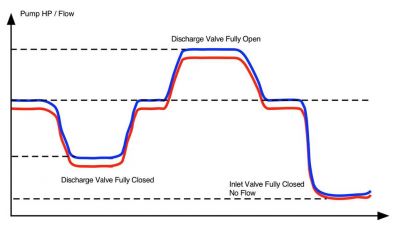
Each point along this curve reflects an instantaneous power measurement. When viewed in total, the area under this curve represents the pump’s power consumption. One kilowatt of power, measured for an hour, is the kilowatt hour the user is billed for. A vertical rise in this curve will be reflected in a larger energy expense, so the ability to monitor and investigate trends over time can be a key strategy to controlling expenses.
The electrical utility may also impose a “power factor” surcharge. This is the energy the power utility has to produce and deliver (the full amount of amps on the motor nameplate). But since they can only bill for the real work or power part, when power factor remains low across a plant, a low power factor surcharge is applied to the bill to enable the utility to recoup this difference.
Comparing power curves to the nameplate hp capacity can indicate where pumps may potentially be oversized and power factor surcharges are likely to impact the financial bottom line.
Getting Started
Options for analyzing this data range from the simple to complex. Important factors to weigh are data acquisition, analytics alternatives, information security and retention policies. Starting with the simplest alternative, the data logger may provide important insights and offer keys for where further analysis is necessary.
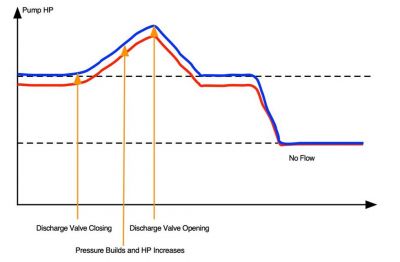
Graphing pump power readings over time allows trends to be spotted and before/after comparisons to be conducted. With power sensors connected to programmable logic controllers (PLCs), data acquisition systems can capture data for graphing, spreadsheet analysis and deeper analytics.
Moving data to the cloud allows detection tools to spot trends. An experienced cloud migration specialist can assist with this project, offering data security best practices and recommendations for data retention that provide access while minimizing costs.
Power monitoring can be an important element of a well-managed pump subsystem. Knowing pump motor power status and consumption provides valuable input about process variables such as feeds, flows, pressure and viscosity, process efficiency and the changes to the pumping subsystem over time.
In addition to protecting pumps, this information can provide valuable insights into potential maintenance needs and energy cost savings.