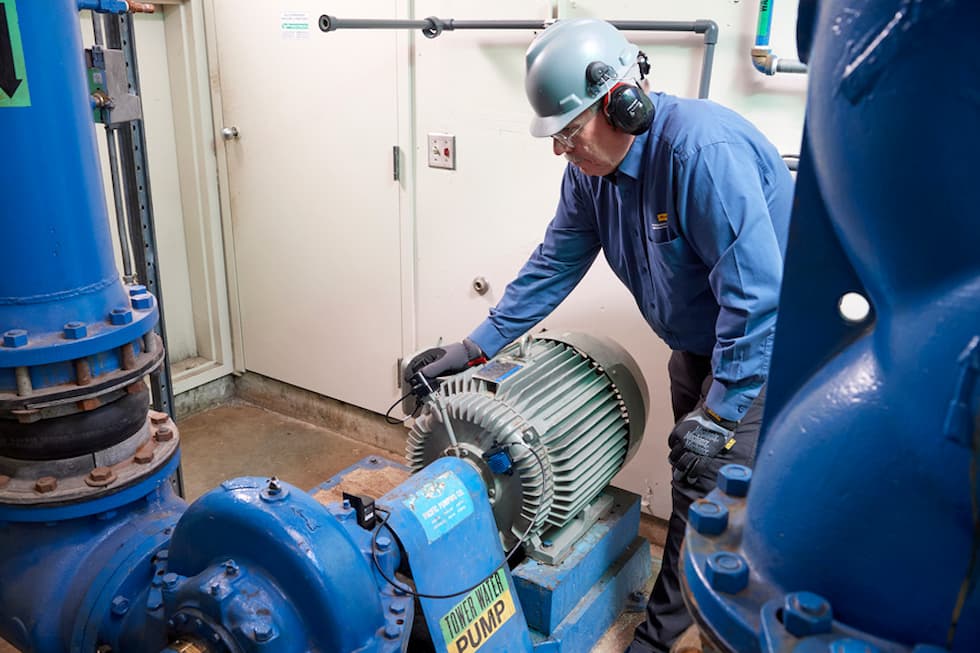
Pumps are great candidates for condition monitoring programs. Early detection of potential faults through condition monitoring means that action can be taken before failures or unplanned downtime occur. Condition monitoring leads to two types of savings. One is going to be from the reduction of emergency repairs: machines are going to be running longer, no loss of production, no emergency repairs and reduced safety issues. Second, once users know the condition of their machines, they can reduce or eliminate unnecessary planned maintenance.
Pumps often run under the same conditions for long periods. While some things, such as high-speed precision tools, wear rapidly, pumps are more predictable. Faults can be detected months in advance. By looking at factors such as vibration and temperature, users can see trends that can be used to screen for potential problems and provide insight into a pump’s condition.
Using Vibration Measurement Data
There are some variables in pumps; for example, sometimes the process can change. But in most modern condition monitoring programs, it is possible to filter out or ignore extraneous factors and focus on things that would be indicators of faults. By looking at patterns in the pump’s vibration, users can find known faults and set up algorithms and templates that follow and track these faults. The vibration patterns are well-known and established and they track easily, so it is simple to identify a fault and its severity—and to know what to do about it and how soon.
Modern vibration measurement and vibration analysis tools have been designed and tested over many years. They have proven to be trustworthy in that they make it simple to screen out what is working and what is not just by looking at the overall vibration in the low frequency range.
A user can be taught to screen vibration data from a portable hand-held vibration tool or a wireless remote sensor. There are also portable and wireless tools and sensors that are more sophisticated. They can be used to set up narrow band alarms.
Think about overall vibration as a broad band alarm—that is, users can set a band over a large band of frequency and then look at all of the vibration data.
To know what a specific fault pattern is, users need narrow band alarms, which look at smaller frequency ranges. By knowing where the frequency is and whether that fault is showing up on the motor or the pump, a user does not have to be an expert to find the four most common faults: imbalance, misalignment, bearings and looseness.
Tools can give an alarm when one of those frequency bands is exceeded, meaning a fault has been detected. That is why pumps are prime candidates for condition monitoring and particularly pilot programs: they follow predictable patterns.
Launching a Condition Monitoring Pilot Program
Many maintenance teams want to start condition monitoring programs by choosing complex, production-critical machines. But to realize the benefits, it is better to start with the machines that are predictable before the more complicated machines that have more variables.
When deciding which vibration monitoring tools to use, there are a couple of factors to consider. One is the accessibility of the machine. Another is the resources of the team—both in terms of staff and the budget available.
Portable tools can be beneficial because one tool can be used among hundreds of machines. The downside is that users might not have access to the bearings
of the machines or the necessary labor hours available.
Another option is wireless vibration sensors. With these sensors, there is a cost. While each one may cost less than a portable vibration tool, depending on the number of machines, a facility may need dozens to hundreds of sensors.
There are benefits to using wireless vibration sensors. Users will not have to worry about machines being remote or inaccessible or the labor involved in doing rounds, like with a portable tool. And with wireless vibration sensors mounted directly on machinery, users can receive more data more often. With around-the-clock asset condition data, users can focus their attention on the machines that need it and prioritize the team’s time and efforts.
Most teams find they want to use a combination of both types of tools. In general, it is recommended to begin a pilot program by choosing a few machines that are easy to access with a portable tool and then choosing a few hard-to-access machines for installation of wireless sensors.
Advancing Maintenance Programs
Over time, users can transition from run-to-failure and planned maintenance to a program that has almost all condition-based maintenance with few planned maintenance and corrective maintenance.
Part of this process is learning which machines need a condition monitoring program. Not every machine in a plant warrants condition monitoring. The transition period is when users can evaluate the machines to put on the program.
As users learn the benefits and see success, they can build a return on investment case to get more budget and expand the program. Users are already busy with keeping the plant up and running, so they can set their team up for success by starting small with a pilot program.