Solution allows property managers to monitor data continuously.
05/28/2019
When the seals fail on 5-year-old pumps, the conventional approach is to arrange for repair. But one property management group decided to replace the pumps completely. Following a recent scheduled shutdown of the air-condition system in a west Toronto condominium building (13 floors, housing 303 owners), the system would not restart. An investigation revealed that both pumps were leaking badly, and it was not the first time there had been issues.
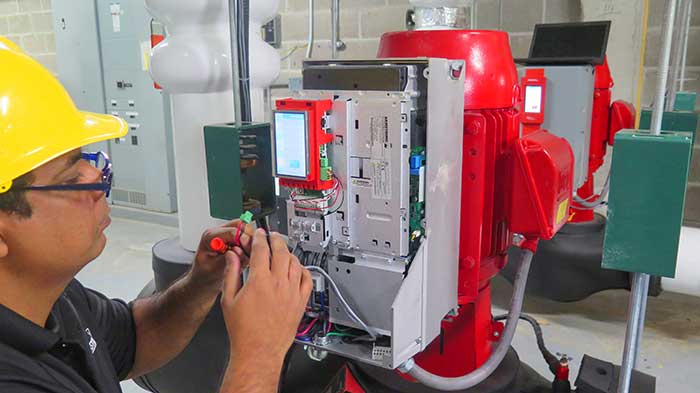