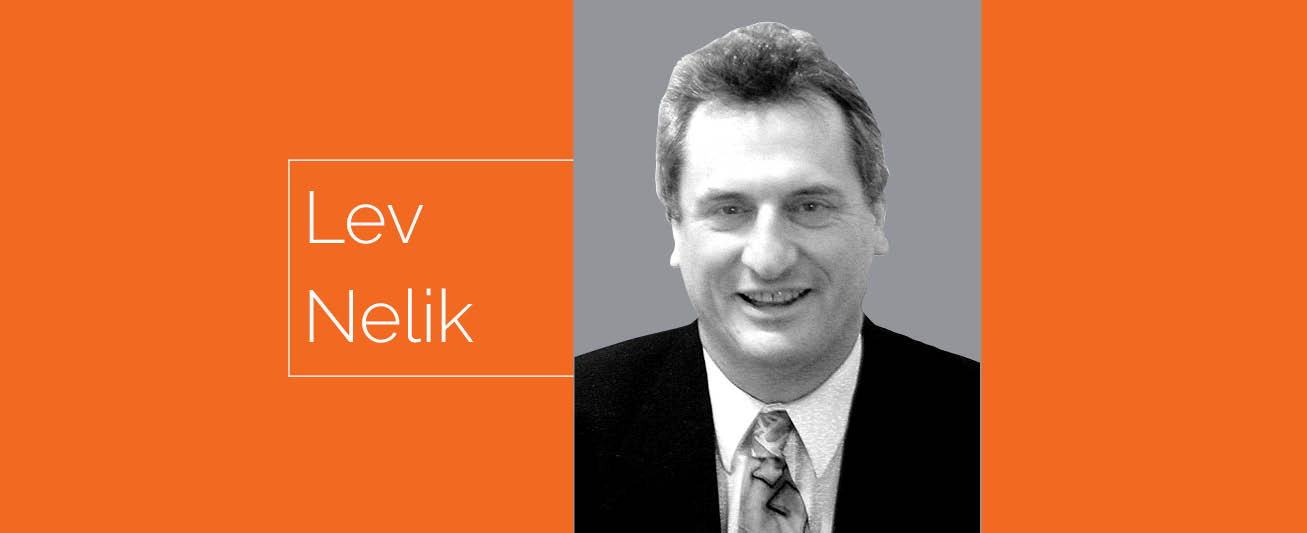
In the September issue of Pumps & Systems, I included an excerpt from the VPRS Standard presenting one such interaction that may shed more light on actual live examples of how such decisions are made (or not made), with quantifying analysis with numbers, to substantiate and balance technical aspects of reliability versus the economics of choosing a path forward. This will be published in two consecutive issues of Pumps & Systems to allow reader feedback and to present the process in a logical sequence.
(Names of companies and individuals have been changed, but the case is real. The language and format of the narrative have been left largely unedited to show a real interaction of a real-life case.)
For the first part of the email exchange, look to my September column. Parts one and two of this series can be found in my March and June columns.
DR. PUMP:
Very interesting, TR.
So, as you noted, the damage might have occurred only initially (as your operators seem to think), as you might have had the highly acidic situation. Let’s say that short time (perhaps several weeks or months) did the damage we see in the photos. Then, the liquid became “nice,” and further damage was not done, other than that which was caused by the initial short period. That would be the first scenario.
Interestingly enough, we are using two separate methods to address the damage for the rebuilds. Due to lead time issues, the first pumps utilized the same bronze impellers initially installed except with a nickel coating. The remaining pumps were rebuilt with 316 stainless steel (SS) impellers. Despite the claims from the electrocoating facility, the thickness of
the coating applied to the impellers ranged between 0.001 inches and 0.009 inches, so we had to set the clearances with new bowl rings.
TR:
Dr. Nelik,
Nice to talk to you today. I looked up some prices for reference for these repairs.
The first repair, which had the nickel coating, ordered new impellers at around $1,700, with an additional $900 per impeller for coating, for a total of $2,600 per impeller (three-stage pump).
The next two repairs both had a 316 SS impeller installed for around $4,000 each (again, three-stage pump).
Hope this helps.
Best Regards,
TR
Sales Engineer, RT Company
DR. PUMP:
TR—I just returned to my office in Israel from a trip to the U.S. It was nice chatting with you while I was there.
From the numbers you show, it is interesting to note that “going fancy” is not always the solution. While technical issues are an initial (and important) aspect, economics must be considered.
In your case, albeit with some simplifications due to real-life data, it is a marginal situation. We can roughly deduce the following:
- Pump life varies between 15 to 25 years, with 20 years being a typical lifetime—during which, practically speaking, something breaks to a point a pump needs to be replaced. This can depend on many factors—the nature of pumpage, abuse, wear and whatnot. Regardless of the problematic component (seals, bearings, bushings, impellers, etc.), by the end of 25 years, a new pump must normally be installed.
- In your case, the Achilles heel is the impeller, and the pump’s life drops to 12 years. Once the pump is pulled, not only are the impellers are replaced, but also the bearings, shafts, etc. Therefore, nothing is left of the old pump, so regardless of if it is rebuilt or replaced, it is essentially a new pump.
Bronze impellers – the cost (as would need to incur after 12 years) of new impellers is $1,700 x 3 stages = $5,100. The cost of pulling the pump, inspecting it, etc., is (I am guessing) another $5,000. So, the total cost is about $12,000, incurred roughly one time during the lifetime of
20 years. The added cost over the 20 years is about $10,000.
Coated impellers – if installed originally, would add $900 x 3 = $2,700 to the initial pump cost and would last, let’s assume,
the max lifetime of ~20 years. Therefore, the added max life of 20 years’ cost is
about $3,000.
316 SS impellers – if installed initially, would cost $4,000 x 3 = $12,000. After subtracting the cost of the bronze impellers, the added cost would be about $7,000.
Thus, the coated bronze options wins, given the rough assumptions and some unknowns. For example, we assumed coated bronze would also last at least
20 years, just as 316 SS—otherwise we would recalibrate our logic. Each case, of course, would have its own economics, but yours is just one example and is perhaps good food for thought for our VPRS Specification readers and users.
Dr. Lev Nelik, P.E.
TR:
Lev,
Sorry for the delayed response. We have been very busy lately.
I agree with everything you said below with the caveat that it would only apply to a water treatment pump, i.e., fairly light-duty, low-wear service. The chemical attack in the pumps we have discussed is very different from erosion. We have quite a few customers who pump from rivers and get one, two or five years from their pumps. We find that these pumps are very largely river dependent. That is, some rivers are just that much dirtier (sand, silt, etc.) than others. We know if it is installed by our river, it will come out much sooner than at another location.
I am picking up an old snowmaking pump at a ski resort this week, and the user is a pretty good friend of mine. I think it might make for a good “example repair” case for the VPRS. The pump is an 8-inch, 10-stage pump (curve attached). This pump also comes with an awesome picture. There was for some reason a weird, natural, biological phenomenon in this river with fish travel where they all entered the pump station at once, and every pump strainer became clogged with fish. The fish were just the perfect size such that their heads would fit in the strainer basket but could not make it all the way through, and they completely starved the pump by clogging the strainer.
If you would like to work on this repair together as an example case for the VPRS, let me know and we can discuss how we should handle it.
Best Regards,
TR
Answers Below
1. How many of these pumps do you have? When were they first installed? (12 years ago?) These four pumps were all installed 12 years ago and have not been out of service until now. We have the last pump in our shop now. The other three have all been here in the last six months.
2. How many pumps came to the shop in 12 years? Have they been coming relatively periodically, or are they starting to come only now (after 12 years in service)? All four pumps came into our shop between the fall of 2021 and spring of 2022. They were all duplicate pumps, and this was first time out of service
for all four.
3. When and how many impellers have you coated and installed, and how are these doing? The first two pumps were rebuilt with standard bronze impellers (as were installed originally) but with a nickel coating. Once those two pumps were back in service, the remaining two pumps were able to be removed from service to be rebuilt with the 316 SS impellers. The 316 SS impellers had a very long lead time, so we ordered them in fall 2021 for the repair in spring 2022.
4. Same as above for 316 SS
Covered above.
Feel free to give me a call if you think it would be beneficial.
Best Regards
References
- “The Downside of Perfection in Vertical Turbine Pumps Repair,” P&S, May 2009, pp. 8-9
- “Finding the Root Cause of Failure,” P&S, April 2009, pp. 10-11
- Pumps Reliability and Efficiency/Energy Monitoring System (PREMS-2A): pumpingmachinery.com/consulting/PREMS-2A/prems-2a.htm
- “Pumps and Pumping Systems Made Easy and Fun” (with VPRS Standard Manual), 4 Volumes, Nelik, L., The World of Ideas publisher, via Amazon