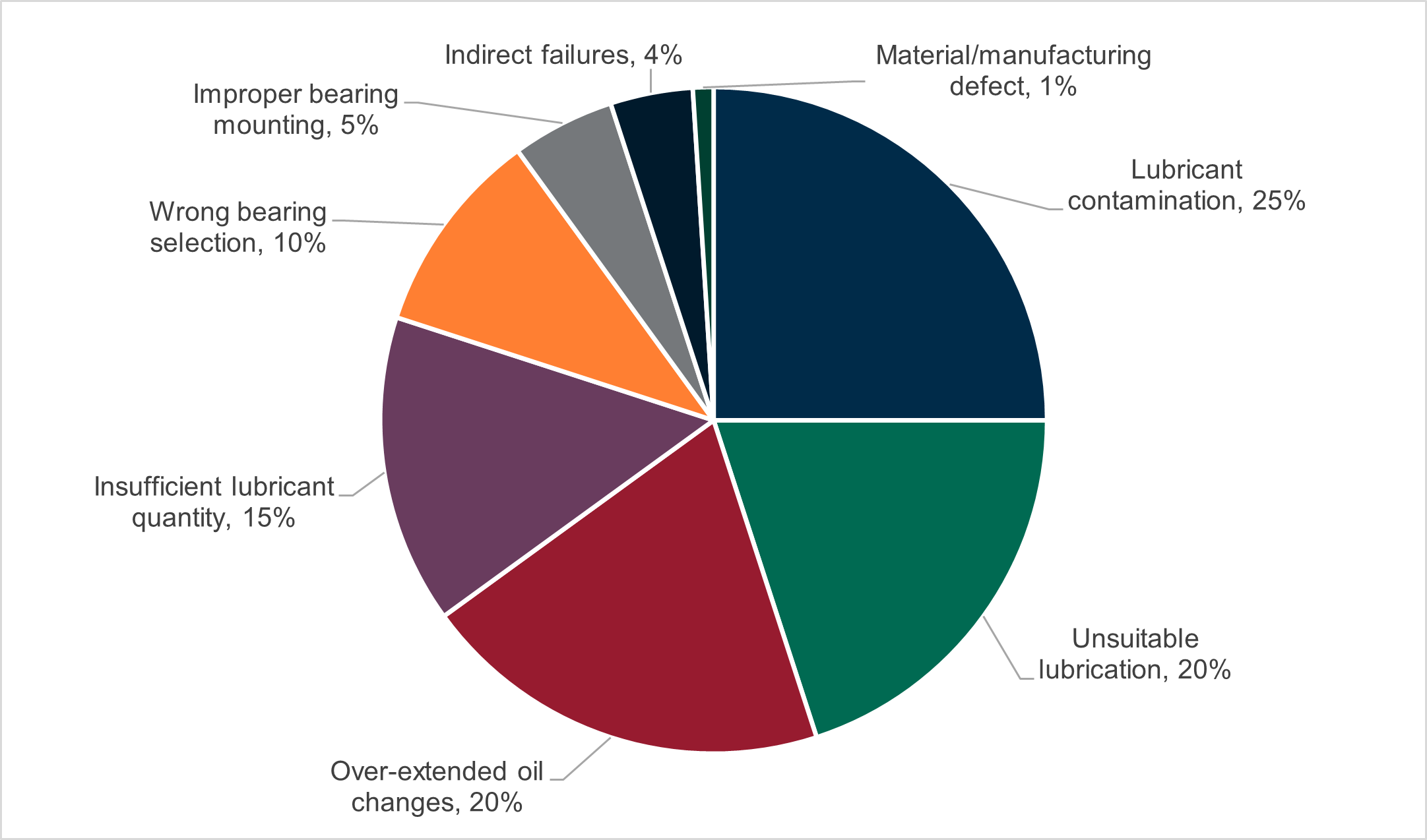
While there are many reasons why centrifugal pumps fail, a large percentage can be attributed to bearing failure caused by lubrication issues. In fact, according to a leading bearing manufacturer, lubrication accounts for as much as 80% of all bearing failures (Top Image). Key factors that induce tribological failures include contamination, insufficient lubricant quantity, unsuitable lubricant and overextending relubrication intervals, all of which are preventable. Pump life could be extended by as much as 30% to 50% by focusing on these four factors.
1. Proper Lubrication
Proper lubrication entails more than selecting the right oil or grease for the application. Lubrication refers to how lubricant is maintained in a clean, healthy state within the pump.
Users cannot simply fill a pump full of oil and expect reliability—they need to continuously monitor lubricant health, oil level and contamination to avoid unnecessary failures.
One way to do this is through oil analysis. However, for many smaller pumps, the size of the oil sump coupled with an inability to extract a representative oil sample often means that the oil in many pumps remains unmonitored. To overcome this limitation, it is recommended to implement daily or weekly visual inspections, executed by operators, lubrication technicians or mechanics. To be effective, inspection should include visual clues to help determine the health, cleanliness and overall oil level in the pump. Inspection check sheets should be developed that ask simple questions with binary answers such as:
- Is the oil clean and clear?
- Is the oil level halfway up the sight glass?
Done correctly, visual inspections can pick up 80% to 90% of all lubrication problems before they become catastrophic and should be mandated whenever operator rounds are used.
Unfortunately, many process pumps are not set up for visual inspections and must be modified to include simple hardware to permit key lubrication issues to be detected. The top image illustrates some simple, inexpensive hardware additions that greatly enhance the “inspectability” of a small centrifugal pump.
Once suitably modified for visual inspections, inspection routes and check sheets should be developed to check for the following:
Oil level
Proper bearing lubrication requires that the oil level be maintained halfway up the rolling element in the oil sump (Image 4). If it is too low, lubrication starvation can occur. If it is too high and churning, increase in temperature and aeration can occur. For smaller pumps, this can be a challenge since some ball bearings can be as small as a half-inch, meaning controlling oil level to within ±1 inch. Most pumps are equipped with a level plug at the correct level or a flat-face bullseye. Flat-face bullseyes work well when the pump is new and in good lighting conditions. However, over time, flat-face bullseyes can become stained or opaque, making oil level checks challenging. Instead, pumps should be equipped with a 3D bullseye that can be viewed more easily and is less prone to staining. Under no circumstances should a constant level bottle oiler be used to gauge if the pump is properly filled. The feed tube from the oiler to the pump can become plugged such that the bottle oiler can sometimes be full of oil while the pump is running on empty.
2. Bottom Sediment & Water Bowls
Water and process fluid contamination is a constant issue in some industries. Whenever water enters the bearing housing, it will either become emulsified with the oil or will settle on the bottom of the oil sump. Either way, water can impair lubrication performance. A pump running with an emulsified oil-water mixture will see as much as 50% to 75% reduction in bearing life.
A simple way to detect the presence of water is to install a bottom sediment and water (BS&W) bowl. This simple device should be installed in the drain of the pump, ideally below the lowest point in the oil sump. Because water is heavier than oil, it will naturally settle to the lowest point in the bearing housing. By installing the BS&W bowl at the lowest point, water can often be observed before it contaminates the oil that is lubricating the bearings (Image 3).
The inclusion of a BS&W bowl has been added to the latest version of the American Petroleum Institute (API) 610 centrifugal pump standard used by the refining, petrochemical and natural gas industries.
3. Oil Color
Whenever oil degrades, the color and clarity of the oil can change. While a change in oil color is not always indicative of a serious issue, a sudden change as shown in Image 5 should be reason enough to further investigate with oil analysis. BS&W bowls and 3D oil sight glasses are both great ways to visually observe and record oil color.
4. Desiccant Breather Inspections
In a previous Pumps & Systems article (“The Impact of Water on Pump Bearing Life,” August 2021), the author discussed the importance of controlling headspace humidity inside the bearing housing using a desiccant breather. However, a desiccant breather is more than just a means of preventing water from getting into the pump. It can also serve as another visual inspection point. Because of the way air flows through a desiccant breather, the color indicator, which turns from blue to pink when saturated with moisture, will change color from the bottom up or top down, depending on circumstance. A color change from the top down indicates that water is present inside the bearing housing, likely from seal failure (Image 6).
Like most rotating assets, pump life is closely aligned with lubricant health and cleanliness. By adding a few simple visual inspections to daily operators’ rounds, early warning signs of impending lubrication failures can be found before functional failure occurs.