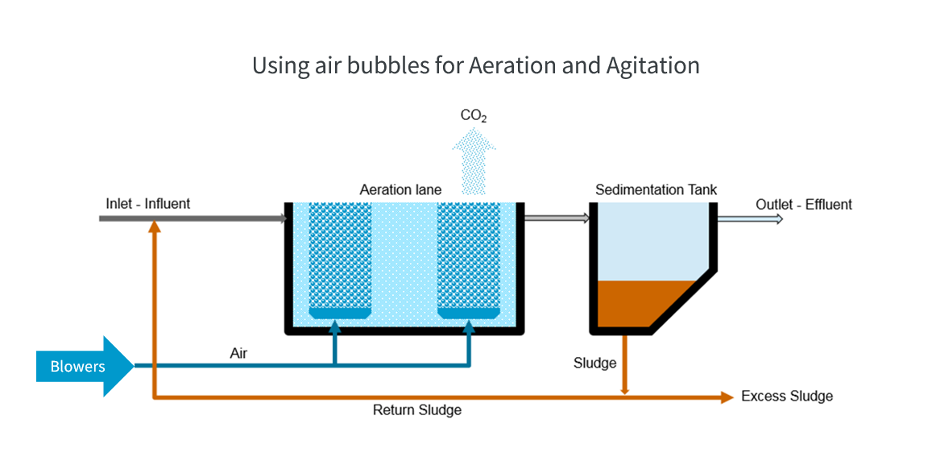
From food and beverage to textiles, wastewater treatment provides users the ability to reverse the damage done to one of the most cherished natural resources. Water is a vital resource, and due to its inherent properties, it offers one of the best methods for conveying waste products in both municipal and industrial processes.
The goal of wastewater treatment is to enhance processes that occur naturally and return the water to a desired purity level. In municipalities, the treated wastewater is released back into a natural waterway. For industries, once the water is treated, it can be reused internally within the company, directed into a municipal wastewater system for further processing, or released back into a natural waterway.
There are two basic stages in the treatment of wastewater: primary and secondary. The primary phase acts as a clarifier that allows wastewater time to suspend out greases and oils at the top and solids at the bottom. Then, water is sent into an aeration tank to begin phase two. The secondary stage uses biological processes to further purify wastewater. Sometimes there is a tertiary phase when additional chemical treatment may occur.
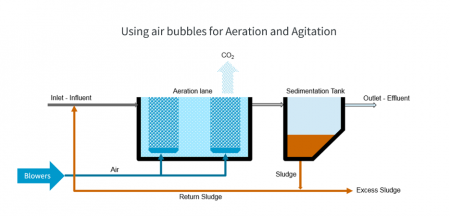
Where Do Blowers Fit Into That Process?
Blowers are mostly used in the secondary phase of treatment to create air bubbles which serve two main processes: aeration and agitation.
The primary function of aeration is to provide usable oxygen for the aforementioned biological processes. This allows a much higher concentration of microorganisms (the agent that removes the waste from the water) to be maintained than what would naturally occur.
Agitation is a stirring action that takes place in the water, keeping the waste materials suspended throughout and making them available to the microorganisms so they can make use of them and remove them from the water stream.
While the science of wastewater treatment is the same, there is rarely a single right answer to blower selection in wastewater treatment design. Different factors may influence user needs, from required flow and system pressure to space available and ambient conditions. Further, due to the critical nature of oxygen in wastewater treatment systems, the redundancy in the system is notably important.
Positive displacement and centrifugal technologies are two major designs for blowers. Positive displacement technologies use screw elements and lobe elements to physically move air.
Centrifugal technologies, on the other hand, feature a dual process where an impeller speeds up the air and a diffuser is used to raise the air’s pressure. Achieving the final flow and pressure is either achieved by sending the air through multiple stages of impellers or through a single high-speed impeller. The single impeller can achieve this high speed through either a direct drive, or using a set of integral gears.
Design Considerations
When determining a suitable wastewater-blower, the first step is to identify the system's required flow. That is determined based on the demand of microorganisms for oxygen in the treatment system. The metabolism of the organic material, the efficiency of oxygen exchange in the tank and the site conditions all play a role in the oxygen required in the wastewater stream.
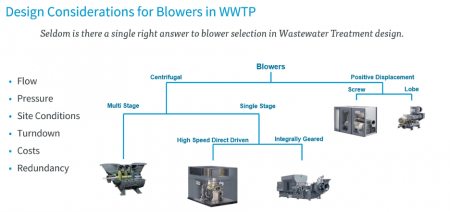
The metabolism of the organic material uses the waste, microorganisms and oxygen (O2) to create carbon dioxide (CO2), ammonia and the energy needed to produce more microorganisms. In a second reaction the ammonia, microorganisms, and O2 is converted into nitrous oxide, water and more microorganisms.
By taking samples and employing an engineering calculation based on the biological oxygen demand, ammonia levels and oxygen transfer efficiency, a standard cubic feet per minute (SCFM) requirement for the system can be determined.
When looking at SCFM, remember this is a mass flow, and it will vary with ambient temperature and pressure. For example, hot air has less oxygen than colder air per cubic foot. What this means is that to calculate real flow rates for the product and application, these calculations should at a minimum consider the site’s elevation, and the high and low ambient temperatures.
A second consideration of the blower sizing will be the anticipated pressure of the system. If a blower has a rating of 17 pounds per square inch (psi), that is really a rating of the maximum amount of system backpressure the blower can overcome. This is a function of the blower’s motor power; the more powerful the motor, the more pressure users can typically get into the pipe.
FUN FACT: A blower actually does not create system pressure. Unlike a compressor, which does create system pressure, blowers create flow. The pressure really comes from the backpressure in the system, which is a function of the static pressure in the system related to tank depth, as well as pressure losses or friction from piping or diffuser pads.
Site conditions will also play a big role in blower selection. High speed turbos and integrally geared centrifugal units are traditionally more suitable for indoor or cleaner applications, where multistage centrifugal and positive displacement units tend to be better suited for harsher environments and outdoor use.
Another big factor is turndown. Rarely is anything within wastewater treatment in a steady state, so utilizing a single fixed-speed blower to provide steady airflow will not accommodate a wastewater treatment facility efficiently. There are peaks and valleys for influx and an efficiently designed system will be able to adjust to meet these changes.
Energy cost is consistently the largest portion of the overall cost of ownership for blowers in wastewater treatment. To provide energy savings, the blower should match the flow to demand. It is not uncommon to see a ratio of maximum to minimum flow of 10:1 or higher in a wastewater treatment facility.
Often, a dissolved oxygen sensor will be used in a wastewater treatment facility’s tanks to monitor the level of oxygen, and it will feed back into a control system that will allow the flow from the blowers to be changed to make sure it stays within a desired range for bacteria growth.
Redundancy Plays a Part
Aeration levels in wastewater treatment are typically five to seven times higher than would naturally occur. If suddenly that oxygen level is not there, the microorganisms will quickly begin to die. Wastewater treatment systems can take days or weeks to get into balance, so system operators cannot take that risk. As a result, wastewater treatment systems typically have multiple blowers to provide a degree of redundancy that enables the process to continue in the event a blower needs maintenance or repair.
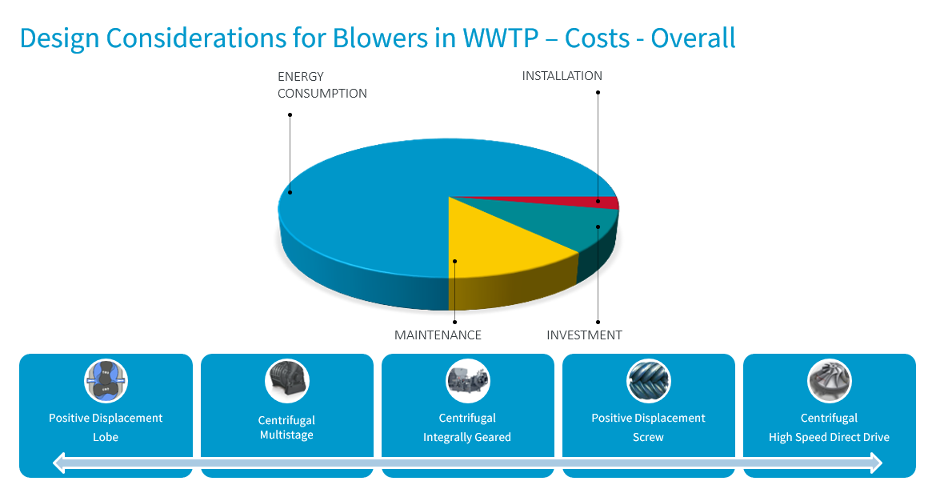
Often, operators split systems into multiple machines. For example, a three-plus-one system would have three units capable of a 1/3 of the maximum flow, plus a machine in standby. With that, operators are able to adjust the flow to maximize system efficiency, providing energy savings and allowing for redundancy to be maintained via a backup machine. Systems like these will often require a smaller investment than one machine capable of 100% of the flow and a backup unit.
Additionally, operators will often use load balancing, where either a controller or a manual approach is used to switch the machines’ roles between primary, secondary and redundancy. So, over time, all machines experience the same amount of run hours, helping with maintenance and life cycle.
Determining equipment needs for wastewater-treatment applications can involve a number of variables, and choosing the right setup can have huge impacts on system efficiency and effectiveness.