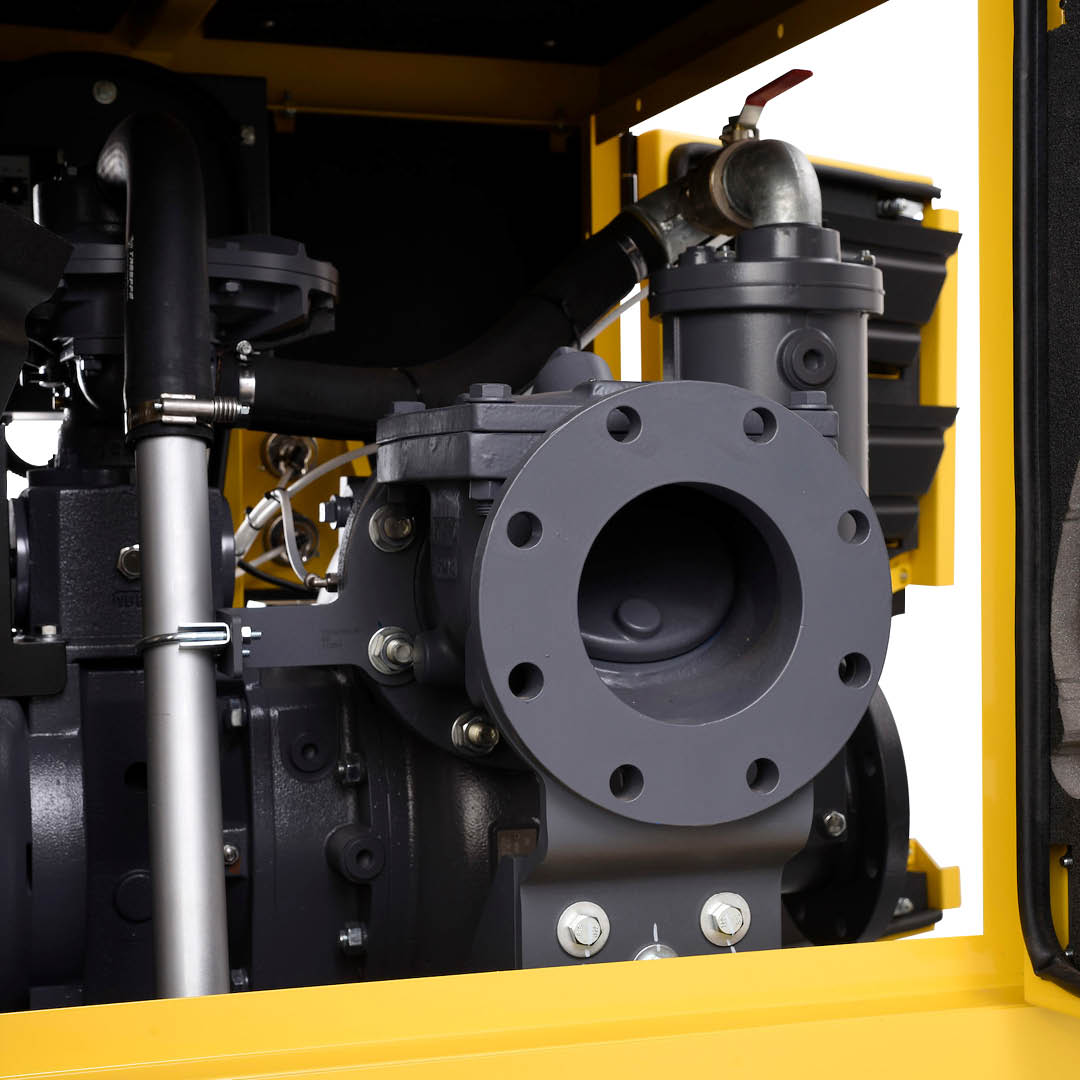
A corrosive liquid is a fluid that will attack and destroy the materials with which it comes in contact. Metals, stone, glass and even some types of plastics can be susceptible to corrosion from corrosive liquids or chemicals, which broadly fall into six categories: strong acids, weak acids, strong bases, weak bases, dehydrating agents and oxidizing agents. Some chemicals can belong to more than one category. For example, sulfuric acid is a strong acid, a dehydrating agent and an oxidizer. Corrosive materials can also belong to other hazard categories such as toxicity (poisonous) or flammability.
If corrosive liquids can destroy materials such as glass and metal, they are obviously dangerous to humans. The United States Occupational Safety and Health Administration (OSHA) recognizes the health risks posed by these substances, defining them as “a chemical that produces destruction of skin tissue, namely, visible necrosis through the epidermis and into the dermis, in at least one of three tested animals after exposure up to four-hour duration. Corrosive reactions are typified by ulcers, bleeding, bloody scabs and, at the end of 14 days of observation, discoloration due to blanching of the skin, complete areas of alopecia and scars.”
When a pump is used to transfer hazardous liquids in oil and gas dewatering—such as flammable, combustible, toxic and corrosive chemicals—it is essential that several factors are considered. These considerations are critical to selecting the proper pump for the job.
Considerations
First, the fluid characteristics. What type of fluid will be pumped? What are the characteristics of that fluid? This information can be found in the fluid’s safety data sheet (SDS, formerly known as the material safety data sheet, or MSDS).
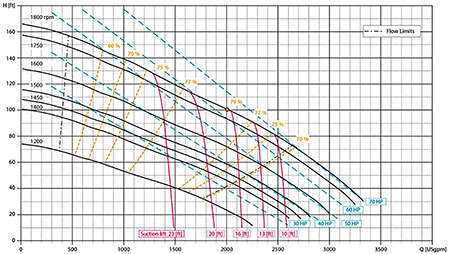
According to an OSHA brief on the SDS, “HCS 29 CFR 1910.1200(g) requires that the chemical manufacturer, distributor or importer provide SDSs for each hazardous chemical to downstream users to communicate information on these hazards … such as the properties of each chemical; the physical, health and environmental health hazards; protective measures; and safety precautions for handling, storing and transporting the chemical.” The fluid’s SDS provides critical data such as concentration, specific gravity, resistance by temperature, viscosity, flammability (if any) and specifics on the content of solids.
Application Requirements
To ensure the pump is properly sized, users must also consider the pump manufacturer’s head-capacity curve. A pump curve (also called a pump selection curve, pump efficiency curve or pump performance curve) gives the information needed to determine a pump’s ability to produce flow under the conditions that affect the machine’s performance.
Reading pump curves accurately—or consulting a pump professional who can—ensures users are getting the right pump based on application variables such as: head (as the energy required to discharge water from a pump to an equivalent height expressed in feet or meters); flow (the volume of liquid to move in a given time period, i.e., gallons per minute [gpm] or cubic meters per hour [m3/h]); rotations per minute (rpm); impeller size, as related to pump performance; power; efficiency; and net positive suction head (NPSH).
The Proper Pump for an Application
The most used equipment for transferring corrosive oil and gas fluids is the centrifugal pump. Centrifugal pumps are energy efficient, available in both standard flooded suction or self-priming, and come in a wide range of sizes that are designed to pump from a few gpm to thousands of gpm.
When pumping corrosive liquids, centrifugal pumps offer another advantage—mechanical seals. These seals will prevent leakage where the internal rotating shaft protrudes through the stationary pump housing. This is similar to how an automobile’s water pump uses a mechanical seal to prevent coolant leakage from the pump. A mechanical seal uses carefully machined flat rings of a durable material—such as ceramic carbon or silicon carbide—where one rotates with the shaft and the other is stationary. The fluid being pumped moves between the seal faces and provides a lubricating film. If the pump is operated without liquid (dry run), the friction causes the seal faces to rapidly heat up, resulting in seal failure.
If a mechanical seal should fail as a result of dry running, liquid will leak from the pump. If the liquid being pumped is water, this may just be an inconvenience. With corrosive fluids, a leak can result in harm to humans, potentially causing extensive damage to the surrounding infrastructure, and possibly creating an environment where users are no longer in compliance with regulatory agencies, such as OSHA. In addition, there are downtime and cost considerations (or mean time between failures [MTBF]) when a pump must be pulled from service and repaired.
Proper Materials of Construction
It is important to choose the proper pump construction materials. This is especially critical when moving corrosive liquids. Not doing so will lead to corrosion of the components that encounter the corrosive fluid—such as gaskets and O-rings—which can impact both the pump’s performance and length of service.
According to corrosionpedia.com, corrosion is defined as “the deterioration and loss of a material and its critical properties due to chemical, electrochemical and other reactions of the exposed material surface with the surrounding environment. Corrosion of metals and nonmetals takes place due to the gradual environmental interaction on the material surface.”
Now, corrosion by itself is usually not that big of a problem. The proper materials of construction—such as cast iron, bronze, manganese bronze, nickel-aluminum bronze, cast steel and stainless steel—are readily available and capable of handling most corrosive fluids safely and efficiently. It is important to understand the various types of corrosion, as well as the factors that contribute to the rate of corrosion, to select the appropriate materials.
It can be difficult to choose a material that can withstand corrosion and additional factors, such as erosion and cavitation. A general rule of thumb in choosing proper materials of construction is to first select materials that will withstand corrosion and then select the one with the most appropriate resistance to abrasion and/or cavitation. Here are a few examples of corrosion users can encounter when using a centrifugal pump to move corrosive fluids.
Abrasion-Corrosion
Abrasion, or abrasive wear, is the removal of metal caused by the mechanical cutting or abrading action of solids carried in a pumped liquid. When the corrosive liquid being pumped also contains abrasive solids (abrasion-corrosion), higher alloyed materials such as stainless steel are often required to ensure the performance and life of the pump. In centrifugal pumps, the impeller is particularly susceptible. Although the casing can be damaged by this, the bigger problem is usually the impeller, along with wearing rings.
Cavitation-Abrasion-Corrosion
Most often occurring with high-suction energy pumps, cavitation is the removal of metal because of high, localized stresses produced in the metal surface from the implosion of cavitation vapor bubbles. In an abrasive-cavitation and corrosive environment, the base material is eroded away as abrasive particles are accelerated toward the impeller surface by the implosive force of the cavitation bubbles, hastening the corrosion process.
Consult a Professional
While this is not a comprehensive guide to pump selection when transferring corrosive fluids, this will hopefully provide users with a snapshot of the challenges, as well as some of the critical factors to consider, when choosing a pump. There is much to consider, from the type of fluid being transported to the selection of proper pump construction materials.
Users should start by gathering information on the fluid to be pumped. Second, gather information on application requirements and environmental conditions. Then, consult a pump professional who can advise in selecting the proper pump for the job taking all of the above factors into consideration.