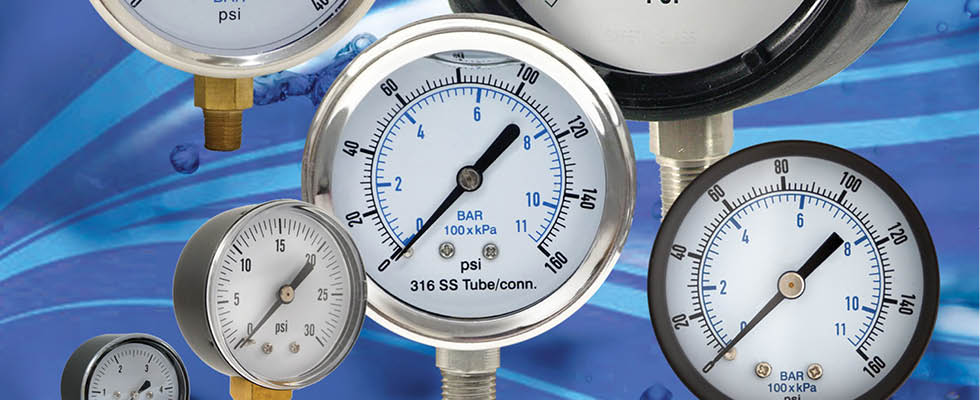
A pressure gauge is an instrument for measuring the intensity of pressure in pressure powered equipment. Whether the equipment operates using liquid, gas, water or steam pressure, systems are designed to operate within a specific desired pressure range, and it is important to ensure there are no leaks and to regulate and maintain optimal pressure levels. A malfunction in either scenario could adversely impact the system performance, as well as the safety of operation.
For more than 100 years, pressure gauges have been a necessity in the proper functioning of a variety of pressure systems and continue to evolve with newer and more complex systems. The type of pressure gauge used is dependent on the system in which it will be installed, with different materials, sizes and designs as required for specific applications with respect to usage, media type and desired method for measurement of pressure. The measurement of pressure is dependent upon the reference that a pressure reading is being measured against, either hydrostatic or mechanical pressure.
Hydrostatic & Mechanical Pressure
Hydrostatic pressure is the pressure exerted by a fluid at equilibrium at a given point within the fluid, due to the force of gravity. Hydrostatic pressure increases in proportion to depth measured from the surface because of the increasing weight of fluid exerting downward force from above. In simpler terms, hydrostatic pressure is generated by the weight of a liquid above a measurement point when the liquid is at rest.
The height of the liquid influences the hydrostatic pressure because of the increase in gravity of the volume/weight of the liquid above the measurement point. The hydrostatic properties of a liquid are not constant because they are influenced by the density and gravity of the liquid involved.
Mechanical pressure is measured using instruments that convert fluid pressure into force. These include a bellows, diaphragm or bourdon tube. It is important to consider other pressure dynamics which are absolute, gauge, atmospheric and differential, all of which are methods for measuring pressure.
Types of Pressure
Pressure gauges are used in a variety of applications and are constructed of various materials in different styles and sizes suitable to the needs of a given application. How a gauge is categorized or defined is dependent on usage, the type of media present and the desired or required method or type of pressure to be measured: absolute, gauge or differential.
Absolute pressure:
The measurement of pressure relative to a vacuum.
Gauge pressure:
The measurement of pressure relative to atmospheric pressure. When the measurement is above the atmospheric pressure, it is shown as positive, and when it is below the atmospheric pressure, it is shown as negative.
Differential pressure:
Measures the difference between two types of applied pressure. It does not have a reference but only measures the two applied pressures.
Types of Pressure Gauges
Absolute pressure gauges are not affected by changes in altitude, but function independent of the variability of atmospheric pressure. They are essential for use in heating, ventilation, and air conditioning (HVAC) systems, aeronautics and distillation processes. A diaphragm between the vacuum and media chambers warps into the vacuum chamber as pressure rises, which converts into a pressure value readout on the gauge face dial.
A capsule pressure gauge contains two thin, corrugated diaphragms that are tightly sealed together at the circumferences. One diaphragm has a hole in the center which allows the medium to enter. The diaphragms expand or contract when pressure is applied, which causes the face gauge dial pointer to move in correspondence with the change in pressure.
Diaphragm pressure gauges have an elastic component, or diaphragm, which is placed between two flanges and is used to ascertain the difference between applied and reference pressures. The diaphragm displaces when pressure is applied. This type of gauge is used for low-level pressure measurement.
Within a differential pressure gauge are two chambers separated by an element that moves in response to changes in applied pressure. An analog version has a pointer on the face of the gauge which moves in correlation with the movement of the element, while a digital version provides a digital display reading.
How Pressure Gauges Are Made
It would not be possible to describe the construction of each type of pressure gauge, as there are so many. This article will focus on the bourdon pressure gauge.
Case
Pressure gauge cases can be made of steel, brass, plastic or the most commonly used, stainless steel. The complexity of design and material used in construction determines gauge quality and pricing. Aggressive, harmful environments, such as those for chemical and petrochemical production, call for phenolic cases, which use a resin made from phenols
and aldehydes.
Cases may be filled with glycerin or silicone, both of which are used to prevent condensation, as well as protect against corrosive environments that could damage the internal mechanism. Rubber gauge covers are used when there is the need to protect the case from impact damage.
Socket
The first part of the pressure gauge the pressurized fluid comes in contact with is the socket. More expensive gauges have a threaded hole for inserting a restrictor orifice, which prevents particles from entering and jamming the gauge. Less expensive gauges have a hole drilled at the outlet connection.
Welding
One end of the bourdon tube is welded where the linkage is attached. In a less expensive gauge, a stamping or mechanical device is used to attach the linkage.
Pointers
Pointers vary depending on the pointer’s complexity and types of fine adjustments the pointer permits. More complex, refined pointers allow for changes in altitude or wear from pulsations and vibrations.
Display
Pressure gauge readings are displayed in analog, digital or dial fashion and vary depending on the type and design of the pressure gauge. The dial scale of the pressure gauge is calibrated to the design and type of pressure gauge, whereas the dial for the bourdon tube pressure gauge is calibrated to the bourdon tube.
Pressure gauges provide readings through either a dial fashion analog display or a digital readout. The choice of display is dependent on the specific type and design of the pressure gauge. The dial of a pressure gauge is calibrated to align with its unique design and type. In this case, the dial is calibrated to the bourdon tube.
Analog pressure gauges, also known as dial pressure gauges, exhibit a scale that is segmented into three sections. Among these sections, the first and third are comparatively less accurate, while the middle or second section boasts the highest degree of accuracy. When opting for an analog pressure gauge, it is preferable for the intended pressure range to coincide with the middle section of the dial.
While the middle part of the dial provides the most accurate pressure measurements, certain pressure gauges achieve high accuracy across the full scale of the dial at 1%.