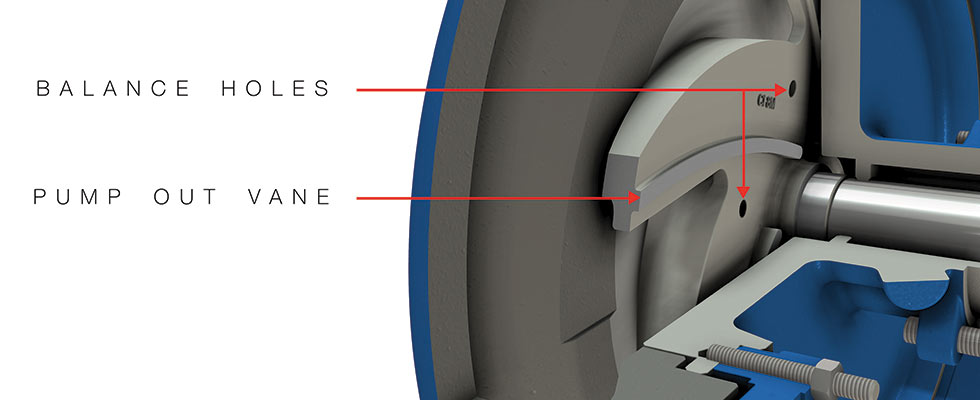
Here is where we left off from Part 2 of this column. Part 1 ran in the August issue, and Part 2 in September. You can find both of those at www.pumpsandsystems.com/author/jim-elsey.
Open Impellers
True open impellers are not commonly used in industrial pumps because the demands of service require sufficient vane support (webbing or shrouds) to buttress the required torque loads and to maintain the relative geometric position of the vanes.
Be aware that sometimes the vanes on open impellers will move over time and service due to material stress relief issues and other operational force factors. This tendency to move (aka, spring) normally makes them unusable for robust applications. On the positive side, because there is no shroud or webbing either front or back on a true open impeller, there is little to no surface area for the pressure to act on, so minimal axial force is generated.
Semi-Open Impellers
American National Standards Institute (ANSI)-style (B73.1 / B73.2) and International Organization for Standardization (ISO)-style (5199/2858) pumps are single-stage end suction types that use semi-open impellers 98.5 percent of the time (author’s unsubstantiated estimate). Note that there are scores of end suction pump models using semi-open impellers that are not designed to ANSI or ISO specifications such as industrial stock and process pumps.
Semi-open impellers have a shroud on one side only. The simple geometry of this construction makes these impellers less expensive to manufacture. Semi–open impellers also possess the ability to pass through more and larger solids including stringy and fibrous materials than closed impellers.
Typically, an enclosed impeller is more efficient than a semi-open impeller of similar geometry, but it is possible for a semi-open impeller, held to a very tight casing clearance setting (aka, leakage) to be as efficient as a closed impeller, at least for that length of time before the effects of wear open the clearance.
High vs. Low Specific Speed Impellers
Axial flow pumps with impellers of high specific speed will not incorporate shrouds or web supports between the vanes and the impeller will appear more like a boat propeller than an impeller. Do not confuse these with open-style impellers in the low specific speed ranges.The consequence of the semi-open design is an impeller with higher unbalanced axial forces when compared to a similar size in the fully closed designs. Under normal operating conditions, there will be a much higher force on the back of the impeller than on the front. The resultant force exerts in a direction toward the suction and the pump’s thrust bearing counteracts that force. Please note that even in normal operation, there can be momentary forces acting in either direction, so the thrust bearing should be designed/selected to handle forces in both directions.
A new medium-sized ANSI pump will develop upwards of 850 pounds of axial force and as the pump wears that force increases. The axial force will be reduced proportionally as the suction pressure increases. These factors and more must be considered when calculating the required bearing size and design life span. A typical ANSI pump thrust bearing is nominally designed for a minimum of 17,500 hours.
A pump designer could simply install bigger thrust bearings and not otherwise address the axial force, but the bigger bearings require bigger shafts and that requires bigger frames and housings—all of those things result in a pump that has a bigger initial cost and a higher maintenance cost.
The more practical method used to reduce the axial thrust on end suction pumps and semi-open impellers is to reduce the axial force on the rear shroud by reducing the pressure. This is why the incorporation of balance holes, pump out vanes or both comes into play as axial force reduction methods. Pump out vanes are a design compromise and so there is a small, but acceptable, trade-off with efficiency and power consumption when using this approach.
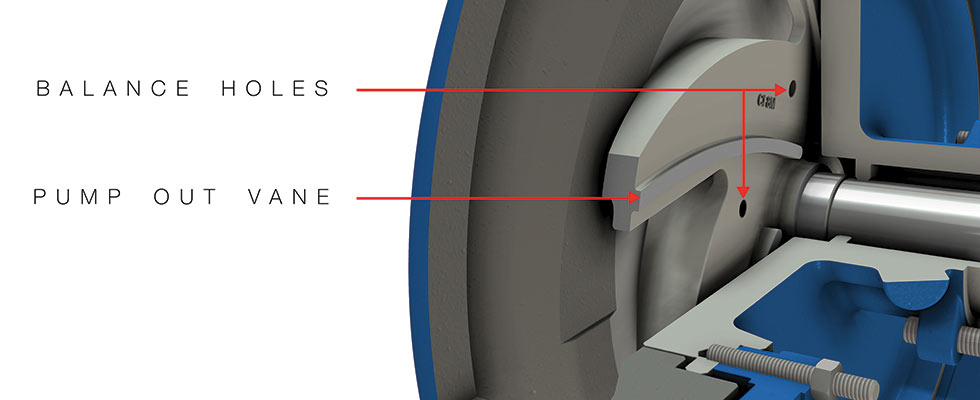
Pump Out Vanes
Pump out vanes are sometimes simply referred to as POVs, expellers, back vanes or back ribs and are just what the name implies: they are small vanes on the backside of the impeller shroud (Image 1). Pump out vanes are probably the most cost-effective method of axial force reduction.
As previously stated, the main purpose for pump out vanes is to reduce the pressure behind the impeller. Reducing the pressure in this area reduces the axial force pushing the impeller toward suction. The function of pump out vanes is similar to standard impeller vanes in that they impart a velocity to the fluid contained in the annulus area behind the impeller.
As the impeller rotates, the liquid that is adjacent to the impeller shroud will also gain velocity due to the simple phenomena of disc friction. Adding the pump out vanes to the rear shroud simply enhances the desired effect by increasing the angular velocity of the liquid. Increasing the liquid velocity reduces the pressure on the shroud and, therefore, the magnitude of the axial force.
A.J. Stepanoff conducted research and developed formulas based on his experiments with pump out vanes in the 1950s and ’60s. He determined that the angular velocity of the liquid in the annulus area will be about 50 percent of the impeller shroud speed (and pump out vanes). Liquid near the shroud is moving at almost the same speed, but it slows down fairly quickly as you increase the distance from the shroud. Subsequent research has demonstrated that the accurate determination of the true angular velocity is more complicated than my statement, but the basic premise is sound.
One area of contention is the distance from the pump out vane to the stuffing box/seal chamber (think nearest obstruction). The distance defines the axial gap of the annulus chamber behind the impeller. As the impeller moves away from the stuffing box, whether through wear or operator settings, the resultant gap will at some point become too great for the pump out vanes to exert their full effect. Most pump experts agree a performance drop will start to occur when the gap begins to exceed 0.060 inches (1.5 mm).
The pressure-velocity relationship, aka, Bernoulli’s principle: The first law of thermodynamics deals with the conservation of energy and states that energy is always conserved and that it can neither be created nor destroyed, but (and this is the important part) it can be altered in form. A liquid moving in a pipe or a pump casing is in a simple pressure-velocity relationship (energy conservation). If the velocity goes up, the pressure will be reduced and vice versa.
For the general purposes of this column, you can consider the description of pump out vane performance as a simple example of Daniel Bernoulli’s equation and the pressure velocity relationship (with sincere apologies to my Applied Fluid Mechanics 301 professor, Dr. R.G.).
The efficiency and effectiveness of pump out vanes is a direct function of at least six design factors. The first four factors are listed in order of importance:
- The radius (length) of the vane
- The height of the vane
- The number of vanes
- The clearance between the pump out vane and the nearest obstruction (stuffing box/seal chamber)
How these factors affect the efficacy of the pump out vanes to reduce thrust is sometimes a subject for debate among pump designers, CFD software developers and engineering researchers. Overlooking some questionable portions of the debate, there remains many aspects of the concept that are agreed on, as follows.
The longer the vane (radius length), the more effective it is to increase the liquid velocity. The caveat is that the longer the vane, the more power is required and it is a function at the fifth power. The bonus is that the manufacturing process of casting the impeller with pump out vanes remains both easy and economical. The height of the vane as it stands out in profile from the shroud (aka, proud) will make it more effective, but at some point you must trade off pressure reduction with the incremental loss of pump efficiency and the inherent increase in power consumption.
The number of pump out vanes is a direct factor in pressure reduction. The more vanes added to the shroud, the more effective the axial force reduction, up to an optimum number of approximately six. Adding more than six vanes will, in most all cases, have no positive effect and so adding a seventh vane will usually be a wasted effort of neutral results. Adding an eighth pump out vane to the design will start to reduce the benefits.
Up for argument: Other pump out vane design factors are the width of the vane and the shape or geometry—think angle, placement and curvature with relation to shaft centerline, i.e., is the vane curved or straight? At this time, the definitive effect of these factors remains both untested and confusing for me. Lastly, often the pump out vanes are where they are simply for economy of production and/or sweeping debris from the space, versus an axial force reduction method.
An additional benefit of using pump out vanes is that the pressure in the seal chamber/stuffing box will also be reduced. This pressure reduction feature works to prolong the life and reduce related costs for the packing or mechanical seal. The reduced pressure effect can sometimes create unintended problems if the product has a high temperature or if the pump is in a lift situation (due to vapor pressure issues).
Either way, there is a higher probability of flashing the liquid to vapor and caution should be exercised. These issues are easily solved with the addition of a flush/seal support system, like a plan 11 or 32, and adding a throttle or restrictive bushing in the bottom of the seal chamber/stuffing box. The portion of the pump world that is governed by API 610 does not endorse pump out vanes as an acceptable method of axial thrust force reduction (API 610 11th section 6.7.1).
Pump out vanes do not increase leakage (bypass) as a balance drum or back ringed impeller would, and they also do not affect the resultant thrust as impeller wear ring clearances inevitably open with wear.
Caution: It is possible to axially adjust the pump shaft such that the pump out vanes are too close to the stuffing box/seal chamber and unintentionally create a vacuum in the annulus and stuffing box area. The vacuum will cause product flashing issues and dramatically shorten the packing or seal life (see remedy above).
Balance Holes
Some impellers will have both balance holes and pump out vanes, others just balance holes or just pump out vanes. Regardless, the reason for the balance holes remains the same, and it is another acceptable method to reduce the axial force and resultant thrust.
Similar to pump out vanes, the balance holes will reduce the pressure in the stuffing box and so, again, be vigilant of the product vapor pressure. It is recommended that you do not use impellers with balance holes in lift situations as the potential for liquid product flashing increases. A lift situation is defined as when the source of liquid being pumped is below the centerline of the pump impeller—that is, the impeller is not flooded. Should the pumped liquid have solids, suspended or entrained, there is risk of clogging the balance holes/passages. Flow from the balance holes will create some level of imbalance and disturbance at the impeller eye, which adds inefficiency.
An impeller with balance holes will make the pump slightly less efficient and require more horsepower to operate. Consequently, the pump is more expensive when calculating the total cost of ownership (TCO). The antithesis is that without the balance holes, the bearing life is shortened.
Operating Tip
The magnitude of axial thrust in a centrifugal pump is a direct function of the differential head. Thus, where the pump operates on its curve will have a direct effect. The further left you operate from the best efficiency point (BEP), the more axial thrust will be generated.
Maintenance Tip
In all of these examples of balancing axial force, it is always important to ensure the pump rotors and impellers are centrally located (both mechanically and hydraulically) in their respective casings/volutes and diffusors. Due to casting variances, machining practices and machine “stack tolerances” (cumulative effect), there may be instances where an impeller will require the addition or removal of a shim and/or some axial position adjustment like a shaft sleeve nut. The purpose of these features is to ensure the rotating mechanical/hydraulic center runs true to the static center of the volute or diffusor. On a new pump, these centering procedure steps were completed during the factory assembly by a knowledgeable technician, but this is also why many better pump designs offer axial adjustment features or suggest and/or support the possible use of shims as required on rebuilds and rotor replacements in the field.
Compromises: Grandma Said ‘You Can’t Get Something for Nothing’
The most efficient and direct method for axial thrust compensation is to simply transfer it to the thrust bearing, which will work in smaller pumps but becomes proportionally expensive as the pump size increases.
Balance drums have a wasteful leakage rate. Semi-open impellers have efficiency robbing pump out vanes, balance holes or both. Cross-over castings are expensive and add another level of complication to the pump. Closed impellers with back rings and balance holes becomes less efficient and more expensive, additionally as the ring clearance increases, so does the axial thrust. Back rings are an added cost, both initially and in subsequent maintenance evolutions, and though seemingly a minor point, they make the pump physically longer.
If you do not purposely design for or add features to balance the axial forces, the thrust bearing will need to be really big, expensive and probably unreliable.
Remember These Two Things
In the end, two things are for sure in the pump world: the laws of physics are strictly enforced, and you can’t get something for nothing.
References
1. K.J. Zanker—Experiments with back vanes used for balancing axial thrust, British Hydromechanics Research Association, 1962
2. Lev Nelik—Pumps & Systems article, November 2013 www.pumpsandsystems.com/reducing-thrust-and-extending-bearing-life
3. Marek Szlaga—Balancing Axial Force, Institute Engineering, Warsaw, Poland, 2019
4. JF Gϋlich—Centrifugal Pumps, 2014
5. A.J. Stepanoff—Centrifugal and Axial Flow Pumps, 1957
6. Sam Yedidiah—Centrifugal Pump Users Guidebook, 1996