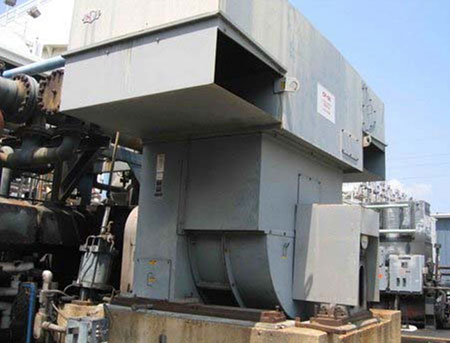
Motor sourcing can be as simple as a repeat order from a trusted vendor to a months-long process involving site visits, research and frustrating conversations between users and equipment suppliers. However complicated the process, the goal is always the same: to effectively procure a quality motor that bolts easily into place and reliably drives equipment for decades to come. Whenever motor sourcing misses the above points, it can lead to costly, slow and even dangerous situations.
While it is true that motors can be viewed as complex machines that bring together dynamic elements of electrical and mechanical engineering, this article will simplify the comparison of one motor choice to another and offer a different perspective on motor sourcing. Through examining the criteria by which motors can be compared to one another and looking at the typical process users take in sourcing them, the end user can avoid some of the costly pitfalls in motor sourcing that many have experienced.
Basic Sourcing Criteria
Whether viewing motors as mechanical devices using electricity or as electrical devices performing mechanical functions, the vital point for motor sourcing is that all motor users have electrical and mechanical needs from these machines. The electrical characteristics primary to all motors are their speed (number of poles), horsepower (hp), rated voltage, temperature classification (insulation and rise) and transient operating characteristics (breakdown torque, inrush current, etc). The mechanical characteristics that matter most to users include frame size (dimensions for motor mounting), enclosure (environmental protections), bearing type and characteristics including overall weight, to name a few. Even these most basic characteristics illustrate the innumerable combinations of electrical and mechanical features that can be created. When these combinations are coupled to the myriad sources available for motors, it is no wonder that finding the right motor for an application can feel like a tall task.
The Sourcing Process
To visually illustrate the motor sourcing process, the flow chart seen in Image 1 was created. Although the process taken differs between users, the flow chart shown is a suggested course of action that attempts to start with the broadest and most-fixed criteria, then working through the points that modify these “basic” specifications. One hope in illustrating this process is that users look “beyond the model number” shown on a nameplate and ensure future motor decisions have all of the true needs in mind. As shown, any sourcing process must begin with a motor need, followed immediately by gathering all information relevant to the motor.
It has been said that a picture is worth a thousand words, but in the case of motors, photos and other data are usually also worth thousands of saved hours and dollars. In particular, photos of an existing installation show vendors items that do not come through in basic motor criteria (i.e., frame size) including nearby obstructions like conduit runs or concrete fixtures, and this aids vendors in choosing correct placement of items including motor terminal boxes and enclosure components. An example of an installation where simply specifying the motor frame size would fall short of detailing all installation requirements can be seen in Image 2.
Though the initial request from a motor vendor for historical data on existing motors including maintenance issues, operating temperatures and amperages, driven equipment performance curves, and repair history might seem superfluous, this small amount of extra effort at the start of a process almost always pays dividends in avoiding otherwise overlooked sourcing mistakes.
Following gathering data, the sourcing process should next determine if an existing motor can be repaired or replaced or if a motor for a new application should be sourced. It is crucial in these initial stages to determine the broad category of the motor needed (squirrel cage induction, wound rotor induction, permanent magnet synchronous, wound field synchronous, direct current [DC], etc.), as well as if the motor must be new or whether some lower cost and shorter delivery option—including a rebuilt machine—would be suitable.
Once these choices are made, broad inquiries to vendors can be sought where the specification of the motor’s speed, horsepower, voltage, temperature characteristics and enclosure are set. How users typically rank these criteria can be seen in the results of a recent pilot study on motor sourcing decisions conducted by a motor design company. The results to one of the questions, “Rank the following criteria top to bottom in order of importance when sourcing motors,” given to a group of motor professionals can be seen in Image 3.
Interesting here is that when asked about motor criteria, most users rank horsepower as most critical, but it is arguable they are missing the preeminence of a motor’s speed in determining the actual torque delivered to the load. For example, an end user would never imagine that they could use the 2,250-hp, 240-revolutions per minute (rpm) induction motor shown in Image 4 in place of the 2,250-hp, 600-rpm induction motor shown in Image 5. Although they are both vertical 2,250-hp motors from the same OEM, the 600-rpm motor has less than half the rated torque of the 240-rpm machine and would not even spin the slower motor’s load. The relationship for this point is shown in the equation for a motor’s full load torque, shown in Equation 1.
Following specification of the base electrical characteristics comes the decision on the motor’s mechanical package, most basically described by frame size. The most straightforward case is a new installation where a vendor’s standard mechanical offering physically fits, but what often occurs is that a user has limitations including existing foundation features or installation interferences that make the basic electrical criteria not match standard offerings from vendors.
Regardless, what follows initial frame choice is an iterative process of selecting bearings, lubrication, and examining modifying requirements like end user specifications, industry standards, or performance requirements such as meeting an unusually high locked rotor torque that might force a change in the mechanical package (frame). These modifications can be as simple as going from antifriction to hydrodynamic bearings that change the exact location of the motor’s drive end shaft shoulder to special electrical performance requirements that force a redesign of the motor’s stator and rotor and cause drastic changes to overall machine size.
At this point in the process, a user should know the motor(s) that would work for their application and need to make sure they have both the technical and commercial information needed to support a purchasing decision. Unfortunately, these two items do present sourcing issues for users but are usually impossible to obtain without first fully defining the technical motor need. What follows evaluating these needs is either an iteration on the process to find more vendors or an end to the exercise, with an acceptable motor being sourced.
Other Considerations
Even when the process shown here is followed directly, there are always unique cases that bring up not-so-easily answered questions. What if a user wants to change from a single bearing wound field synchronous to a two-bearing squirrel cage induction machine to increase protection, simplify operation and simplify alignment? See examples in Image 6 and 7.
What if the motor is installed and the end user then has concerns about previously unspecified or uncovered items including unexpected motor noise or housing skin temperatures? What if a replacement motor interacts with the motor control center (MCC) in ways that differ from the previous machines but are not otherwise a maintenance concern?
The best advice here is the same as in many other areas of life: stay calm, work methodically and always collaborate with trusted vendors. Additionally, with motor sourcing, it is often the case that the simplest solution is the smartest solution and there is much to be gained in leaning on industry best practices and common sense.
Putting It to Work
By viewing motor sourcing as a straightforward, repeatable process based on a few set criteria that are modified by user-specific requirements, the “magic” often associated with this process has hopefully been demystified. If users are willing to evaluate how they have previously viewed motors, a new perspective might afford entire supply chains the opportunity to offer more value to motor users and avoid costly downtime associated with poor sourcing decisions.
There is more work to be done in this area but starting to look simply “beyond the model number” and into what users actually need will certainly improve both users’ and vendors’ motor sourcing experiences.