
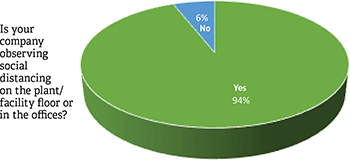
From additional personal protection equipment (PPE) to special safety training, pump industry companies have not taken the threat of COVID-19 lightly.
According to a Pumps & Systems survey conducted in May, 74 percent of the more than 100 respondents said PPE requirements have changed in response to the coronavirus outbreak. Ninety-four percent of respondents said they are required to maintain social-distancing requirements.
“We have found PPE and specific antiviral cleaning items in limited supply, but with some persistence and focused effort have been able to maintain adequate stock,” Pumps & Systems columnist Jim Elsey said in May about his workplace at Summit Pump Inc. “We are maintaining our normal working hours and note many of our employees utilize flex time schedules. We are practicing proper distancing of personnel and we are blessed with a large facility that allows us the space.”
PPE Requirements Differ
Chris Wilder, CEO of Sealing Equipment Products Co., Inc. (SEPCO), said that because the company is a critical supply manufacturer, it has remained in operation, but many procedures have changed.
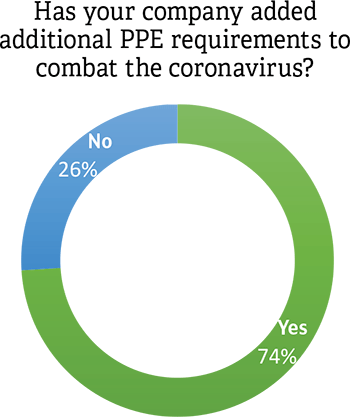
“While securing necessary PPE was initially a challenge, our sourcing team was able to procure the needed items and, as a service, has been able to offer some supply to our authorized distribution network,” said Wilder, a Pumps & Systems Editorial Advisory Board member. “Within our facilities, we have more tightly restricted access and access points, set up multiple hand-sanitizing stations, staggered shift and break times, and instituted 6-foot minimum distancing rules. We are also sanitizing work stations and areas nightly and, during the day, high-use touchpoints receive multiple sanitizations.”
How strict the PPE requirements are seems to vary from company to company. One survey respondent said a “medical-grade mask must be worn anytime in an area where you might come into
contact with another person.” Another said that in addition to the usual PPE, “cleaning supplies and processes, masks, gloves, dividers between work stations, dedicated pathways/doorways/restrooms” are all required.
A few respondents said they must receive a daily temperature check and are required to stay home from work if any illness symptoms are present.
“As our team begins to see more activity out in the general public, we definitely feel we are behaving in a much more secure and conservative manner than what we see in the general public,” Wilder said. “We’ve worked hard to develop new habits, and I believe so far it has paid off in the health and security of our SEPCO team.”
COVID-19 Safety Training
Special training sessions have become the new normal for many companies—in one example, a survey respondent said the CEO is leading weekly COVID-19 webinars/open discussions.
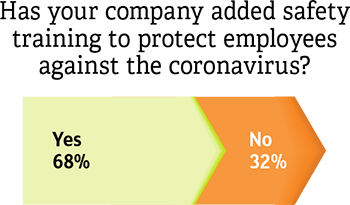
Many employees are receiving updates via email, and some have dedicated internal websites. One respondent said the internal website has the company’s own internal policies posted, but also recommendations from the United States Centers for Disease Control and Prevention (CDC) and links to other health resources.
While some respondents said employees are still mostly working from home, they do intend to put together safety training when employees return. Many respondents noted the CDC’s posters, which can be printed free of charge, as a helpful tool to have posted around worksites and facilities.
How Business Operations Have Changed
Travel is another part of doing business that has been affected. Todd Loudin, president/CEO of North American operations of Flowrox, said the company had issued a no-travel policy until at least June 2.
“If we have an emergency where a customer requires a visit to their facility, all requested travel requires senior management approval,” he said. “We are really trying to avoid any unnecessary travel.”
Elsey, of Summit Pump, said the same is true at his company.
“We are restricting visitors and nonessential meetings on our site. Our management and sales people are currently not traveling and are working from their home offices,” he said. “We are making good use of this time for both formal and informal training of our distributors and our own personnel via the common and normal internet and phone programs and apps.”
John Malinowski, Pumps & Systems Editorial Advisory Board member and an industrial motor consultant, said he already works from home, so this is not new for him. However, he does feel something can be missing when people are not able to meet face to face.
“I must say that groups can have teleconferences but they are not as productive as in-person meetings and conferences where additional side conversations can be held,” Malinowski said.
Survey respondents said that “all face-to-face contacts have been reduced to emails and phone calls where possible.” And in some cases, nonemployees are not allowed to enter offices.
One respondent said office employees are operating on staggered work schedules to reduce personal contact. Another, that vehicle use is limited to one person per vehicle only.
Read what our readers had to say about salaries and training here.
Read what our readers had to say about safety here.