Ray Hardee continues his explanation of process safety management.
Engineered Software, Inc.
08/08/2018
Editor’s Note: This is Part 2 of a series. Part 1, in Pumps & Systems, July 2018, introduced developing a model for process safety management (PSM).
There are 13 areas included in a process safety management (PSM) plan. The piping system model can be of value in all aspects of the PSM, but the areas of greatest impact are in:
- process safety information
- process hazard analysis
- operating procedures and practices
- employee training
- pre-startup safety
- managing change
- investigation of incidents
Process Safety Information
Complete and accurate information concerning process chemicals, process technology and process equipment is necessary to develop an effective PSM program. This information is used to develop the process hazards analysis, training programs, operating procedures, information for the contractors working on the project, pre-startup reviews, materials for local emergency preparedness planners along with insurance and enforcement officials. A major component of the process safety information is a diagram to help users understand the process. As outlined in 29 CFR1910.119, the diagram can either be a simplified block diagram, process flow diagram, or a piping and instrument diagram (P&ID). The piping schematic is the primary interface of the piping system model. It is provided in the form of a flow diagram or P&ID and offers the user a comprehensive view of the system. The piping schematic shows all the major items in the piping system including pumps, tanks and vessels, heat exchangers, control valves, along with the interconnecting pipelines. The various isolation and check valves are displayed for each pipeline. Every item in the piping system model has a user-defined name, which increases the usefulness of the piping schematic. The addition of text and notes on the drawing increases the presentation value.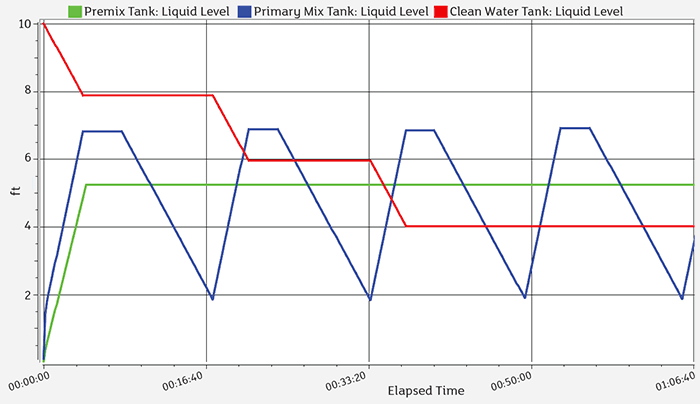
Process Hazard Analysis
The process hazard analysis is one of the most important elements of the process safety management program. It is an organized and systematic effort to identify and evaluate the potential hazards associated with the handling highly hazardous chemicals. It analyzes the potential causes and effects of fires, explosions, release of toxic and or flammable chemicals along with major spills of hazardous chemicals. The process hazard analysis is dependent on good judgment along with documentation stating the assumptions made during the study. It is important that the team understand the assumptions and the information, which can be reviewed and maintained for a future process hazard analysis. An accurate simulation provided by the model gives the team a clear view of how the piping system will work under any expected operating conditions. By opening and closing pipelines, turning equipment on and off, and setting the levels and pressures in tanks and vessels, the user can quickly see how the system will be operating at any moment in time. Using the dynamic simulation feature, users can include the logic for the system (equipment logic, instrument set point, control valve settings, etc.), and then the program simulates how the system will operate over an extended period. Since many of these conditions are highly unusual events, it is unlikely that any one individual has sufficient background to determine what will happen under extreme operating conditions. This is where the ability to simulate those conditions can provide crucial insight.Operating Practices
The plant operating procedures describe the steps that must be taken, date to be recorded, conditions to be maintained, samples to be collected and the safety and health precautions to be taken to successfully operate the process system. The operating procedures must be easy to understand, technically accurate and maintained to reflect the current operation of the system. The operating procedure should be reviewed by the engineering staff and operators to ensure accuracy. It should include sufficient detail on how the job duties are to be performed. Operating procedures should describe safe pressure limits, temperature ranges, flow rates and applicable alarms. Finally, procedures should clearly state what to do when an upset condition occurs.Employee Training
The PSM program requires all employees, including maintenance and contract employees involved with highly hazardous chemicals, to fully understand the safety and health hazards of the chemicals and processes. Since the piping system model consists of a detailed piping schematic along with information about the equipment, it provides much of the information needed to train staff. Each item of equipment in the system is detailed in the model along with much of the manufacturer’s name plate information and operating information. Hypertext links to manufacturer’s equipment manuals can also supplement the information about each item of plant equipment. Links to the MSDS data sheet provide detailed information about the chemicals used in the process.Pre-Startup Safety
Using a process hazard analysis will enhance the safe operation of a new process. Before startup, the creation of the piping schematics, the operating details and staff training is required. The software can assist engineers and designers in sizing individual pipelines, selecting pump and sizing control valves as well as simulating the operation of the total piping system. Since the piping system model is a life cycle design document (similar to CAD drawings and other design document), any changes made to the system design will be reflected in the piping system model. The operating company using the model in developing the PSM can use the most current piping system model available from the design firm. If the system is modified more than simple “replacements in kind,” the piping system model provides a starting point for the current operation of the system. This gives the engineers designing the modification a clear picture of how the system operates, and they can make changes to the model to reflect the proposed change. Once again, if the model is kept current during the design and construction process, it can be used by the operating company as the piping schematic, used to develop the operating procedures and assist in operator training as required by the PSM.Managing Change
Any changes to the system must be evaluated under the PSM program. This includes changes in the procedures, raw materials and processing conditions other than “replacement in kind.” These changes need to be properly managed by identifying and reviewing them prior to making the changes. For example, if the change affects the pressure limits, temperature ranges and flow rates, then the operating procedures must be changed to reflect these new conditions. Changes to the process fluid viscosity and/or density could have major effects on the operation of the total system. The viscosity and density changes will increase the head loss in the pipeline for a given flow rate. In addition, pumping a viscous fluid will tend to decrease the pump head and efficiency, while increasing the power needed to pump the fluid. By making the fluid changes in the model, one can quickly see the consequences of changing the fluid properties on each item in the piping system and how that affects the operation of the total system.Investigation of Incidents
Incident investigation is the process of identifying the underlying causes of incidents and instituting changes to prevent similar events from occurring. The PSM expects the company to investigate not only incidents that resulted in a release, but also near misses that could have caused serious consequences. Using both the steady state and dynamic simulation capabilities of the model, the in-house team can lead the piping system through the events leading up to and throughout the incident. Using plant-operating data, one can enter the fluid properties, valve positions, set points and tank levels to get a picture of what is happening during the event. Using the dynamic simulation capability of the model, one can also enter the system logic and event starting conditions. By running the time simulation, users can easily see what is happening in the system, set event notes and graph any calculated results to understand what happened. Once the cause of the incident is known, the recommended changes in system design, process or operating procedures can be tested using the system model to see how changes will mitigate future incidents.Conclusion
An effective PSM program requires a clear view of the entire process including the process design, operational and maintenance procedures, nonroutine activities, emergency preparedness, as well as training programs. A key element in the development of the plan is providing everyone involved with a clear picture of how the process piping system operates under any expected operating condition. Once the clear picture is available using the piping system model, this information is invaluable in developing an effective PSM program.
To read more Pump System Improvement columns, click here.