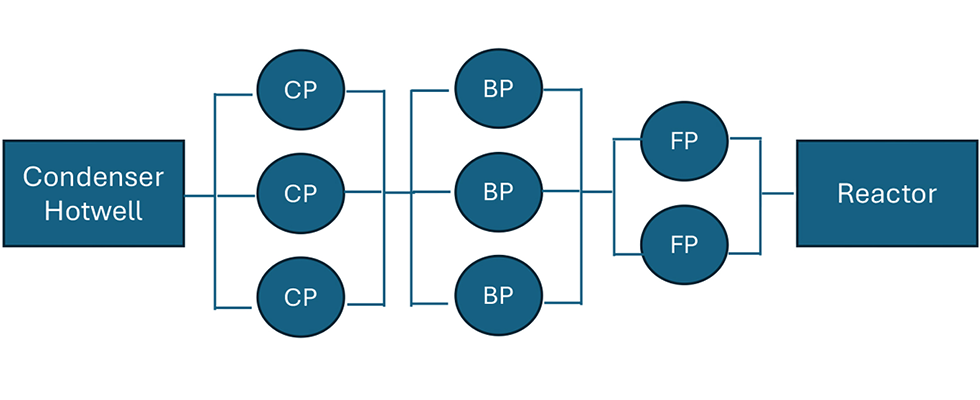
In 2024, the United States Department of Energy set a goal to increase U.S. nuclear power capacity by 200 gigawatts (GW) by the year 2050. This goal was established to ensure that a reliable, clean energy source exists to power anticipated future power needs, which have grown exponentially with the advent of artificial intelligence, electrification, cryptocurrency and other power-intensive data processing requirements.
While new reactor technology—such as small modular reactors (SMR)—is continuing to progress, a more immediate opportunity is present in increasing the output of existing operating facilities. For this reason, many nuclear power plants are in the analysis or implementation stages of extended power uprates (EPU), which increase the generation capacity of the unit. This increase in capacity is accompanied by an increased flow requirement into the reactor, which in turn requires greater flow and total developed head (TDH) through the reactor feed system.
The change in hydraulics required to meet the added flow and pressure needed for EPU provides users the opportunity to optimize applications and take advantage of the latest technologies and operating experience, thus realizing the lowest cost of ownership of the pumps and drivers comprising the feed pump system. This entails limiting the initial investment for new or modified equipment—and reducing maintenance costs and parasitic energy costs by upgrading designs and operating at the best efficiency point (BEP).
The customary approach for EPU is to contract an architect and engineering firm to determine the path forward on modifying equipment to produce the required additional flow and pressure. Their solution is often to add the additional percent flow and pressure to each pump in the feed pump train, thus requiring all new pumps and motors—an expensive initial investment.
Additionally, the specifications for new purchase rarely include upgrades in material and component design to mitigate and hopefully eliminate the generic failure mechanisms that pump experts understand via enhanced design tools and operating experience. These specifications usually mimic the original specifications, resulting in 1980s vintage designs and their inherent fatal flaws.
Another choice is to contract a pump company and utilize their subject matter experts to both optimize the system and incorporate state-of-the-art designs that extend operating life and increase the reliability and availability of each application. Many times, this can be done by reusing the existing equipment—both pumps and motors—which minimizes capital costs and maintains the existing footprint.
This was the challenge posed by a U.S. nuclear generating station that was approved for an extended power uprate. The plant contracted a pump aftermarket service company with a strong nuclear-focused engineering background to perform an assessment of the pumps in their reactor feed system. The resulting report provided recommendations for optimizing the existing equipment to meet the new demand reliably and efficiently.
Initial System Overview
The engineering study began with an overview of how the equipment was operating at the existing system demand. This overview helped the aftermarket service company understand how head was distributed between the applications and what additional head was required to meet the new system flow. The subject nuclear plant’s reactor feed system had three pumps operating in series: a condensate pump, a condensate booster pump and a reactor feed pump.
The existing alignment of the feed system pump train was three condensate pumps operating in parallel, feeding three booster pumps operating in parallel, discharging to two reactor feed pumps operating in parallel. The approved EPU required a 16.3% increase in flow and a 2.77% increase in TDH from the three applications acting in series.
The design of the subject pumps was:
- Condensate pump: 3-stage vertical can (VS6) pump with below ground suction, fixed speed, electric motor driven
- Booster pump: Single-stage double suction (BB1) pump with volute casing, fixed speed, electric motor driven
- Reactor feed pump: Single-stage, double suction impeller with diffuser casing, variable speed, steam turbine driven
The initial investigation uncovered that all pumps were operating back on their curve, away from the BEP. Further investigation uncovered that the TDH of the three applications acting in series based on the OEM design was significantly greater than the actual system resistance. This condition where the pumps had been “oversized” was most likely due to conservatism on the part of both the system designer and the pump OEM, a common occurrence within the industry.
The initial analysis also identified the main constraints on the system, which included horsepower limitations for the motor-driven condensate and condensate booster pump, net positive suction head required (NPSHr) margin for the condensate booster and reactor feed pumps, turbine speed and horsepower limitations for the reactor feed pump and pressure limitations of ancillary equipment, such as demineralizers, installed at various points within the system. These constraints would need to be taken into account when considering any head redistribution between the three applications.
Assessment of Current & Future Operation
Operational excellence of pumps is achieved by mitigating hydraulic instability at both the impeller inlet and exit. As stated previously, this is accomplished by operating each pump within -10%/+5% of its BEP. A study conducted by Waloddi Weibull demonstrates the impact on pump reliability when not operating at BEP. Another important consideration is the necessity of providing acceptable net positive suction head available (NPSHa) to NPSHr margin.
All these considerations were employed to optimize the hydraulic parameters of each application.
Test data was available for the condensate and booster pumps from the aftermarket service company’s certified pump performance test lab. Using this test data and the OEM factory test of the reactor feed pump, the following can be concluded regarding the above-stated reliability parameters:
- The condensate pump meets all conditions for EPU and EPU +5%.
- The booster pump meets the net positive suction head (NPSH) margin requirement for EPU and EPU +5% as well as the BEP requirement for EPU.
- The reactor feed pump meets the NPSH margin requirement for EPU and EPU +5%.
The study initially concluded it was probable that all reliability parameters could be met for all applications for EPU and EPU +5% if the booster and reactor feed pump impellers were redesigned to have BEP at the EPU flow condition. The redesigned impellers would fit into the existing casings, requiring no modifications to the existing foundations and structures. It was recommended computational fluid dynamics be employed to validate the interaction between the new impeller and existing casing would not cause flow separation and subsequent loss of performance.
Exploring Different Scenarios
While it was strongly recommended that the site choose to modify the hydraulics of the existing booster pump and reactor feed pump so they would meet the stated reliability parameters, the aftermarket service provider also analyzed two other operating scenarios and provided an unbiased report on the risks associated with each option.
Major considerations when assessing modifications included:
- The suction can diameter (cemented in place) limits the ability to increase the impeller diameter of the condensate pump.
- The electrical supply available at the condensate pump limits the ability to install a larger motor for the condensate pump.
- Pressure limitations of demineralizers installed between the condensate and booster pump limit the ability to increase the head of the condensate pump.
The options considered included:
- Option 1: Restoring the pumps to the original design with no modifications
- Option 2: Adding an additional stage to the condensate pump (from three stages to four stages) to provide more head while maintaining the original design of the condensate booster and reactor feed pumps. This modification would require a larger electric motor and shafting/bearing system for the condensate pumps.
- Option 3: Designing new custom impellers for the booster and feed pumps to be installed in the existing casings. The new design would have its BEP at the EPU flow and redistribute head between the two pumps to put more head into the booster pump, allowing the reactor feed pump’s turbine drive to operate at a reduced speed and horsepower.
The study showed that the pumps would be operable, but not optimal, for the EPU flow rates under both Option 1 and Option 2. The greatest concerns for normal operation were the NPSHa margin and operation relative to BEP for both the condensate booster pump and reactor feed pump.
Another Scenario Emerges
While evaluating the recommendations that were proposed by the aftermarket service provider, the site uncovered an additional set of conditions that changed the course of the analysis. Because the reactor feed pump arrangement used two 50% pumps in parallel, the loss of a single feed pump would have created a condition where the other pump had to deliver 68% of EPU flow to avoid shutting down the unit.
This new scenario made the previously supplied recommendations untenable. In this new condition, the single operating feed pump would increase speed significantly, and analysis showed that both the turbine overspeed limit and design turbine horsepower rating would be exceeded. American Petroleum Institute (API) 612 limits steam turbine overspeed limits to approximately 27% above the rated speed; the required speed in this scenario was approximately 39% of the design speed. The site reached out to the steam turbine manufacturer and confirmed that this speed would be unacceptable.
Additional head would need to be added to either the condensate or booster pump to reduce the head generation required by the single feed pump, placing the turbine back within its design parameters. Given the limitations of the current electrical supply to the condensate pump, the site decided to place the additional head in the booster pump.
Having done their due diligence to understand how the reactor feed system pumps would react under different operating conditions, the nuclear plant was able to choose a path forward that reduced risk and best suited their reliability goals and project budget. In lieu of supplying redesigned impellers within the existing casing, as had originally been planned, they opted to work with the aftermarket service company to custom-design new booster pumps and feed pumps to operate at their BEP and to deliver the required pressures.
This project demonstrates the importance of a rigorous system analysis when approaching an anticipated change in system demand, as with an EPU.