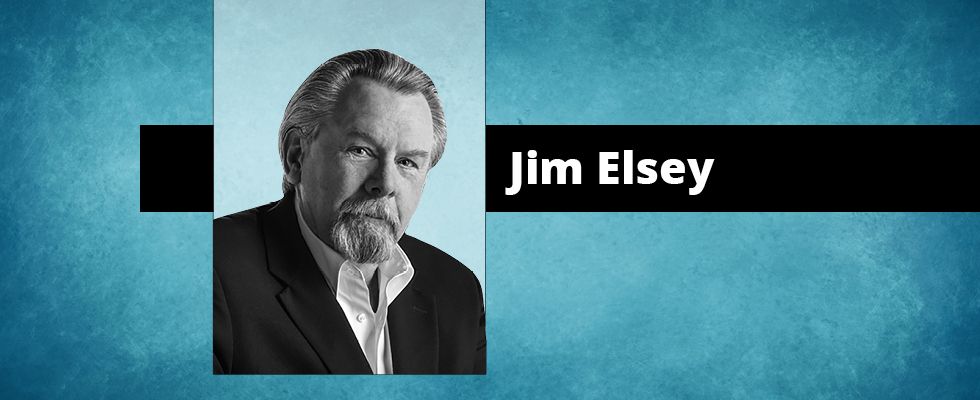
In my November 2020 Pumps & Systems column, we looked at efficiency and reasons why pumps may not be as efficient as we’d like. Now, let’s focus on how to make the pump more efficient.
A pump engineer can make several design changes that will increase the pump efficiency. Efficiency improvements are most often tradeoffs that may also sacrifice reliability and cost/price.
To make a pump more efficient, we can:
- Make the wetted surfaces smoother (reduce the roughness). The smoother the surface finish of the casing and impeller, the more efficient the pump will be—another valid reason why investment casings are a good choice especially for smaller pumps. Ceramic materials or coatings (if applied properly) are another step that can help increase the efficiency.
- Reduce the clearances. The smaller the clearance, the lower the leakage rate across the opening. This means more liquid is going through the pump only once, and it is not recirculating.
- Reduce or mitigate design leakage paths. Examples include impeller back ring leakage to suction and leakage rates for balance drums and discs (features that mitigate axial thrust).
- Reduce the liquid shock losses. Imagine what a drop of liquid experiences as it transits the pump—it involves several right angle turns at high speeds and at high rates of change. The addition of an inducer can add some prerotation “swirl” to the fluid to mitigate entrance losses. The optimum inlet angle of the impeller blade (vane) can be altered and, just as importantly, act as the profile shape of the leading edge of that blade.
- Change the curvature and rate of curvature for the impeller vanes to be more “backwards.”
- Add or remove impeller vanes in some impeller designs and/or reduce the thickness of the blade (vane).
- Remove diffusor vanes and the additional cutwaters required on dual volutes.
- Offset the casing centerline from the impeller centerline so the volute has an ever-increasing cross-sectional area for the fluid to exit.
- Increase the pump speed and size. The faster and larger the pump, the more efficient. The smaller the impeller, the more negative the effect of disc friction. It is just a simple case of proportionality.
Efficiency Over Reliability
Better surface finish and investment castings for impellers and casings will cost more money. Smoother surfaces on the wetted parts are not as effective in reducing efficiency as the viscosity increases because the flow regime of viscous fluids tends to be laminar.
The dual volute, diffusor vanes and concentric volutes all help the pump to be more reliable by mitigating the radial thrust. These features also aid in reducing shaft and bearing sizes.
Thinner impeller vanes reduce the amount of torque that can be applied, consequently reducing the workload capacity of the pump. There is an optimum number of impeller vanes for ideal pump/impeller efficiency, but that number may be at odds with the pump’s functioning and its ability to handle solids and fibers or a desired curve shape.
Closer wear ring clearances require more operator control of both the warmup and cool-down cycles (think: the rate of change of temperature).
Close clearances also require a more robust shaft to prevent deflection at off-design operating conditions and potential rotor sag at low speeds, especially when on turning gear and during startup evolutions. Close clearances do not handle suspended solids very well—galling and scoring will occur to the wear ring surfaces.
Maintaining closer clearances will require more frequent outages for maintenance and possibly more expensive materials—and gee whiz, it will also become imperative to turn the pump off when the supply source is empty.
The proper material selection for efficiency may be the wrong material to handle the liquid properties. An inducer will help reduce shock losses and help with net positive suction head (NPSH) issues, but it may reduce the head capability of the pump. A pump with close clearances is overall a less forgiving pump.
Steps To Help Efficiency
- Design and operate systems that allow for more efficient operation.
- Design for the long run, not justfor this quarter’s profit levels and stock performance.
- Monitor and manage the pump performance.
- Adjust the pump speed in lieu of impeller trimming or discharge valve throttling.
- For pumps with external impeller clearance settings, make sure the pump impeller clearance is set to the recommended clearance.
- On pumps with wear rings, monitor the pump hydraulic performance and renew the clearances when performance diminishes.
- Close bypass valves when not needed. Review and rewrite the program on the programmable logic controller (PLC) for three-way process control valves.
- Size the pump and/or the speed to match system requirements. Throttling the discharge valve should be a temporary fix, not a permanent solution.
- The effect of viscosity on a centrifugal pump is dramatic. Make sure that the pump is designed for the application, and that the liquid is up to design temperature (it should lower the viscosity) before starting the pump. Question if the liquid should be pumped with a positive displacement pump.
- Probably, the most important step the to take is to have the system curve available and compare it to the current pump curve to ascertain where the pump is operating on the curve, then make revisions as necessary
Many system designers attempt to solve three or more problems with one pump, though they could be better off with three different pumps in the same system. The three pumps could be different sizes and speeds. Perhaps it is as simple as pumps in series and/or parallel or the addition of a “pony” pump. One of the biggest energy mistakes I witness is the operation of two pumps in parallel when only one is needed.
Do What You Gotta Do
Not all pumps are designed to be efficient. Some pumps are designed for special purposes. Like special teams in a football game, they have a very specific job to do where function and reliability are more important than efficiency. Examples may be a slurry or trash-handling pump, a low-flow, high-head pump and/or a vortex or disc pump. When selecting the sump pump that prevents flooding in the basement of my home, I am more focused on reliability and functionality and not on efficiency. Note: I have two pumps installed.
In Conclusion: My Issue
For 50 years, I have witnessed increasing pressure to make pumps more efficient. This is something most users don’t want to pay extra for, and I appreciate that. However, I am a witness to a trend in which the careless pump operation renders the overall system inefficient. There are companies that have proactive programs, but there is a large percentage that do not.
The mission for increasing pumps efficiency must come from the top down (CEO and board)—not as a platitude or a poster on the bulletin board, but as a mandate, a priority and a proactive method of operation. Old paradigms must be changed, and the entire staff must be educated. There are incentive programs that will pay dividends to initiate these goals. At the end of the game, you will actually save money. Like grandma used to say: “What good is an efficient pump running at dead head?”
Read more Common Pumping Mistakes articles here.