Energy is a valuable commodity. This is why the world’s first high-efficiency circulator came to be in 2001. With the help of electronically commutated motor (ECM) technology, this efficient, functional and flexible pump for heating, cooling and air conditioning can reduce annual power consumption by up to 80 percent. This technology filled a gap in the industry to address energy efficiency and remainsl relevant today. Now more than ever, as technology continues to evolve, digitalization is omnipresent and changing industries worldwide, including how people think about energy. A “smart” pump is a perfect example of this evolving technology. Smart pumps are a new category of pump. A smart pump provides the ability to connect using a smartphone or a tablet and operate the pumps and receive useful information for diagnosis or operation. A smart pump application also offers a facility for downloading updates and trends. This technology is being used in the commercial and residential markets and goes beyond the high-efficiency pumps or intelligent pumps of the past. The combination of the latest sensor technology, innovative control functions through dynamic and multi-flow adaptation, bi-directional connectivity (i.e. Bluetooth, integrated analogue inputs and binary inputs/outputs), software updates and setup guide upon power-up are the features that make a pump “smart.” The on-board set up offers an intuitive, user-friendly operation. Innovative functions such as multi-flow adaptation and no-flow shutdown optimize energy efficiency. Multi-flow adaptation is a new energy-saving function enabling the pump to adjust its output to the precise demands of the circuit pump(s). The pump can automatically adapt its output to the varying system requirements with dynamic adaptation without setting a target value. No-flow shutdown controls the system by sensing the demand for flow and either starting or stopping the pump accordingly. New control modes ensure flexible and perfect adaptation for all applications. Setting a constant target temperature or constant differential temperature further enhances the efficiency of the pump and the overall system. In addition to the new control modes, the smart pump addresses the industry standard control modes, including:
- dynamic adaptation
- T-const (temperature constant)
- dT-const (differential temperature constant)
- Q-const (volume flow constant)
- index circuit evaluator
- PID (user-defined PID controller)
- dP-c (differential pressure constant)
- dP-v (differential pressure variable)
- N-const (constant speed)
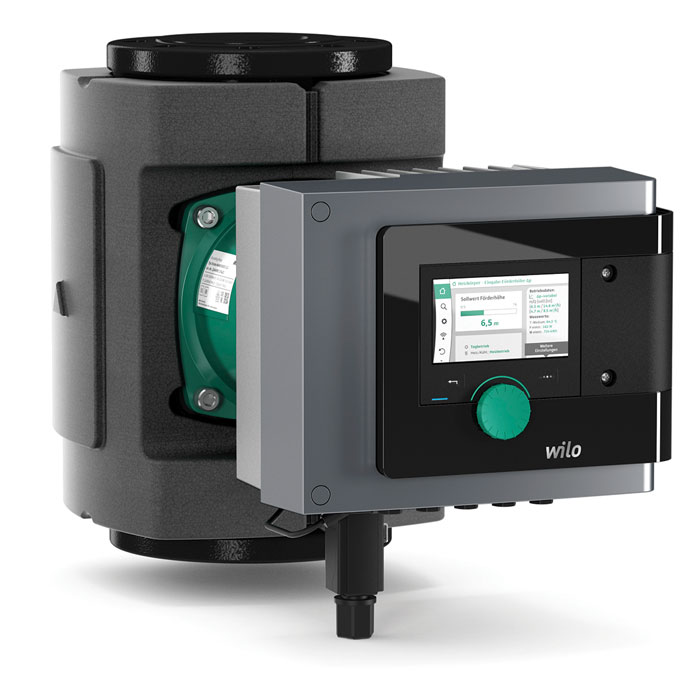
New Smart Pump Functions
- Configurable volume flow limitation via QLimit function (Qmin and Qmax)
- No-flow shutdown (automatic deactivation of the pump)
- Automatic venting of the rotor chamber
- Switchover between heating and cooling mode (automatic and manual)
- Separate heating/cooling quantity measurement
- Automatic setback operation
- Automatic deblocking function and integrated full motor protection
- Dry run detection
- Operating modes of double pumps: min/standby operation, parallel operation (efficiency optimized double pump management)
- Operation history recording (volume flow, heating and cooling quantities) per day and week