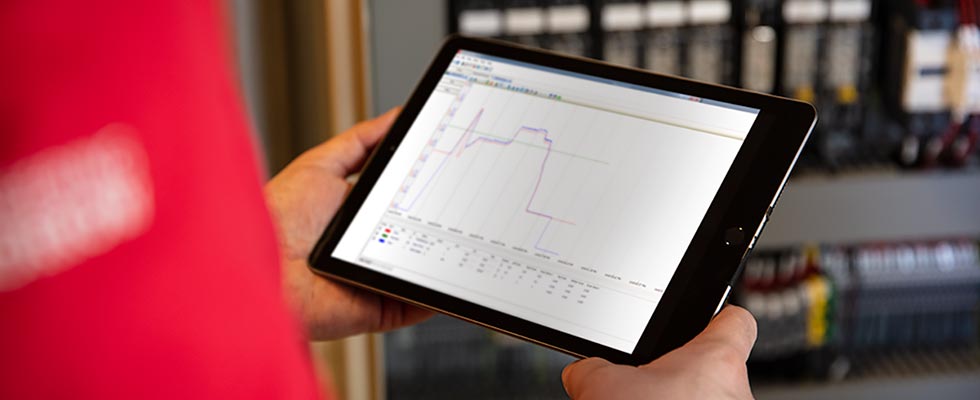
Rapid advancements in technology continue to alter the way the world is viewed. Over the past few hundred years, the world has transitioned through several different industrial revolutions and gone from work performed by steam, water or horsepower to electrical motors. Looking back half a century, process control primarily focused on variable direct current (DC), complicated multipole motors or many other mechanical and electrical variations.
To increase efficiency and performance, industries have since transitioned to variable speed three-phase motors. This has been made possible with pulse-width modulation (PWM) technology that provides variable voltage and frequency to operate electrical motors based on need, rather than at a fixed speed. Furthermore, through intelligent design, users have been able to integrate feedback loops to help increase performance and provide more efficiency.
Today, the variable frequency drive (VFD) comes in many different variations; from simple volts/hertz machines to more advanced, high- performance devices that have secondary functions and features integrated into their control structure. VFDs can now use external sensors and monitor more aspects of a process. Further, they can be connected to local or remote monitoring systems to have data logged and trigger warnings when performance appears abnormal.
These newer intelligent controllers can provide critical data about themselves and their connected motors or transfer information from other sensors to provide a more holistic picture of the integrity of the process. For a building or a plant, this frees up critical staffing resources to focus on other tasks and only attend to problems as they arise. Intelligent capabilities also reduce the need for multiple controllers, as functions are now being integrated into a single module—reducing space, costs and complexity.
Yet, many core systems today are often accepted to work as-is, without consideration for the possibilities yielded by newer, more efficient technologies. Existing equipment typically is on regular maintenance programs. The cost to operate is relatively fixed, and it is left to run unless and until it fails. Many of these systems are operating digitally, either fully on or off.
Intelligent Controllers for HVAC
By applying intelligent controls to a building’s heating, ventilation and air conditioning (HVAC) system, through new units or via retrofits, users now have more opportunities to improve energy and life cycle efficiency for the entire process. Take the addition of pressure sensors across air filters. This technology can intelligently advise when a filter needs to be changed based on filter integrity rather than at a predefined maintenance interval. Knowing when to change a filter based on need can prevent the extra operating costs that occur when a system uses partially blocked filters or when filters are changed prematurely.
Further, integrated condition-based monitoring for motors can continuously check the integrity of the motor windings and provide alerts before catastrophic failures occur. Because these units are often located in low-traffic areas, the addition of vibration sensors can help to detect problems in either the motor, fan or pump. Ultimately, this data can be fed back into the VFD and then distributed throughout the building’s automation network. It can quickly trigger warnings or alerts about potential problems and notify maintenance staff before a severe issue arises.
Intelligent Controllers for Water & Industry
As part of the most critical infrastructure, how we manage the supply and treatment of water is essential to daily life. Many water and wastewater facilities are small and spread out, with minimal observation. More advanced technologies today provide ways for operators to remotely manage and monitor these facilities. In fact, there could be several monitoring devices located on-site or near the electric motors that could also deliver data into the VFD. With the growth of IoT systems, some VFD manufacturers have the capacity to integrate remote monitoring systems that, through an internet connection, are able to feed information back to the cloud. This allows users to remotely check in on their equipment and quickly diagnose problems.
Remote monitoring can be set up so that external sensors are integrated into the VFD to provide auxiliary information about other aspects of the system such as temperature, pressure and tank levels. If an issue were to arise that required outside support, the cloud data could easily be shared with VFD technical support teams who could read and interpret it. This can mean faster dispatch of the resources required to address the problem, reducing the cost and time for diagnosis trips to the site, especially for remote locations.
When moving into a world characterized by bold energy transformation, new applications for VFDs beyond simple motor controls are becoming more relevant. New applications for VFDs are providing avenues to complement existing variable speed motors and are impacting the way users approach systems design. In fact, the same VFD components are now able to perform DC-DC conversion with a few ancillary parts. This allows users to connect batteries or capacitors into VFDs, so that they can continue to run, at least for a few minutes, during a brownout or power failure.
Further, DC-DC converters can store regenerative energy, like on a lift when lowering. Other applications are using PWM technology to push or pull energy from the grid with an active front end. It is even being extended to grid-interactive inverters that have the capacity to store energy in batteries for peak power shaving or ride through during brownouts or a grid failure. Combining these across a DC power network enables users to manage multiple energy sources such as wind, solar and storage.
With the rise of these technologies comes the need for more trained staff and experts to troubleshoot and maintain the equipment. Thankfully, with remote monitoring and cloud services, many VFD manufacturers are leveraging quick-response, digital tools like video calls or screen-sharing technologies to provide application support for installations. Using the convenience of a computer or phone, technicians now have access to specialists who can help them walk through the startup, commissioning and life cycle maintenance of the product. Simple apps are also now available to help users create a database of their VFDs and access specific data and information about them.
The key to unlocking and deploying these new technologies is finding the right partners who share the latest advances, support you through specification and startup, and help maintain products. For example, it is now possible to take some standard batteries, configure them with a DC-DC converter and apply them to a remote pump, so that any time the power browns out or fails, the pump will continue to run until a generator is turned on. By using these same PWM technologies, more opportunities exist to integrate renewables or store energy for future use, helping to reduce carbon footprint.