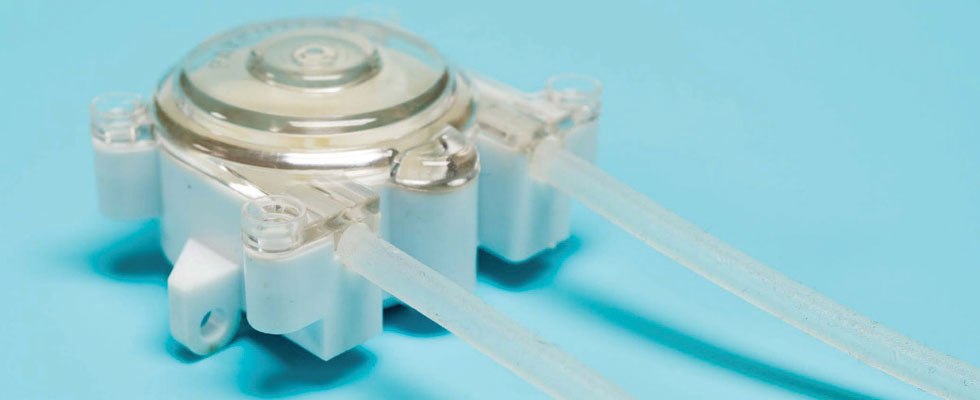
A life science company developing bioreactor systems for cell growing operations struggled to mitigate heat generated by open-loop step motors used in peristaltic pumps that control the flow of materials into the bioreactors.
Up to six pumps per bioreactor system supply various fluids and gases to grow cell cultures in the development of new medicines. Operators must closely regulate temperatures within the bioreactors to ensure optimal growing conditions. Excessive heat generated by the open-loop step motors was elevating the temperature of the fluids pumped into the bioreactor, increasing biological process times and reducing yields.
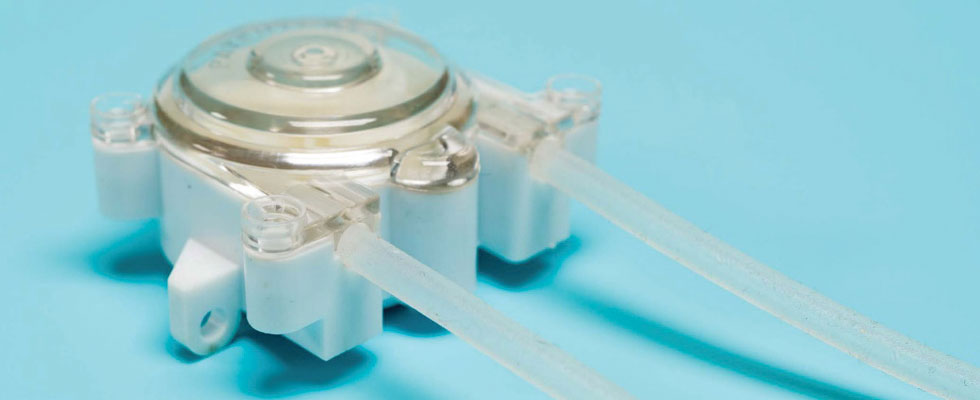
The Role of Step Motors
Peristaltic pumps (Image 1) are commonly used in sterile environments, such as bioreactors, as they feature internal tubing so the media does not touch pump components and become contaminated. Rollers attached to the shaft of a step motor compress and release the tubing in the peristaltic pump to efficiently move media into the bioreactor chamber. Step motors typically provide accurate position and velocity control of peristaltic pumps at a low cost. However, traditional open-loop step motors typically operate at high temperatures, which can lead to heating the pump and the fluids flowing through it.
While all motors generate heat during operation, open-loop step motors produce a significant amount because they continuously operate at full current, regardless of torque demand. Heat in step motors is caused primarily by the current in the windings. Because the open-loop step motor system continuously supplies current to the motor whether or not full torque is required, the excess current is lost as heat.
This excess current caused a problem for the life science company because the open-loop step motor’s heat would transfer through the pump head and into the materials dispensed into the bioreactor. The optimal way to reduce excess heat generated by the step motor is to reduce the current in its windings.
A Cooler Alternative
Using encoder feedback and servo-control firmware (Image 2), closed-loop step motor systems automatically adjust current in the motor windings in proportion to the required torque. As a result, closed-loop step motors run cooler and consume less power.
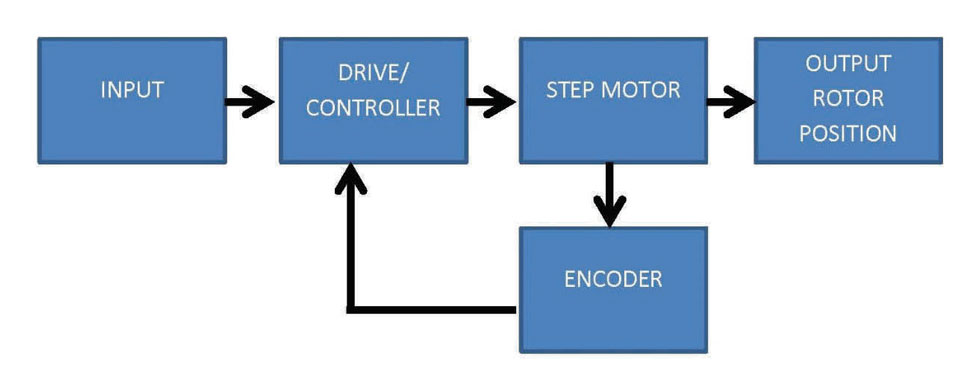
A closed-loop control scheme can reduce step motor heat by as much as 50 percent. When using a closed-loop step motor to drive a peristaltic pump, less heat is transferred through the pump head and into the pumped media.
Standardization of Motor Size
Before upgrading to closed-loop motors, the life science company considered alternative solutions, such as using different-sized, open-loop step motors for each tubing and media combination and adding a temperature regulator to cool the media after leaving the pump head.
To meet the varying torque demands from different combinations of tubing (diameter, material) and media (viscosity), the life science company needed to stock three different sizes of open-loop step motors. Different motor sizes better matched torque requirements without generating too much excess heat. In addition to increasing inventory requirements, the use of three motor sizes added complexity during field service work on the bioreactor systems.
Adding a temperature regulator to stabilize the temperature of the media in the tubing also made the system more complex by requiring another control system to operate the chiller. It also added cost to the system.
Switching to a closed-loop step motor offered a better solution than both alternatives. Because of the closed-loop step motor’s ability to accurately control current proportionally to the torque demand, a single-size National Electrical Manufacturers Association (NEMA) 23 step motor could run all combinations of tubing and media.
This one motor size now serves as the standard in meeting the diverse torque requirements from the smallest to the largest diameter tubing, without the worry of excessive heat generation.
The ability to use one standard motor also enabled the development of one generic pump head assembly that only requires operators and field service technicians to change tube adapters to dispense different materials to the bioreactor system.
Now, the life science company can stock one pump assembly instead of a range of pump assemblies outfitted with motors of different sizes.
Additionally, because the current control of the closed-loop step motor so effectively reduces the amount of heat generated by the motor, a separate temperature regulator operating in-line with the pump is not necessary.
Advantages of Integrated Motors
Implementing a closed-loop integrated step motor to run the peristaltic pumps, instead of using separate motor and drive components, offered advantages including:
- reduced componentry
- decreased space requirements in control panels
- lower expenses due to field service and maintenance
Integrated motors (Image 3) combine the step motor and encoder with an onboard drive and controller.
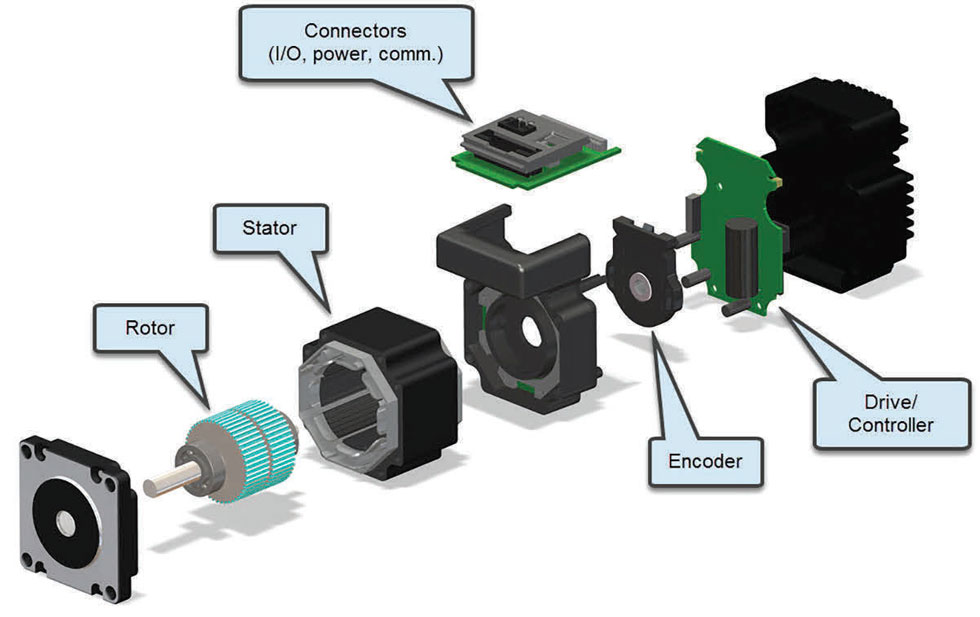
Using these motors, operators no longer need to separately test the motor, drive and wiring when troubleshooting systems. The company also can stock fewer parts.
Incorporating an integrated motor into the peristaltic pump assembly freed panel space in the small control panels of the bioreactor system and eliminated the need for cabling to connect separate (nonintegrated) motors and drives.
Another benefit of the integrated motors used was dual-port Ethernet. When installing pump assemblies into the system, daisy-chain connecting Ethernet cables between the integrated motors reduces the number of network cables routed around the equipment and back to the control panel.