A Kansas City motor repair shop developed a virtually foolproof process for protecting pump motors from electrical bearing damage caused by stray shaft currents. For six years, Scott Wilkins, the manager of motor shop operations, has overseen the reconditioning of hundreds of vertical motors through a process known as the vertical motor solution. None of them has had repeat bearing failure. After replacing the ruined, pitted bearings, his team installs a shaft grounding ring next to the motor’s guide (lower) bearing and, using proprietary techniques, applies ceramic insulation to the carrier that holds the thrust (upper) bearing in place at the motor’s drive end. Although destructive currents can occur in any motor, Wilkins reports that most of the bearing damage he sees is in motors controlled by energy-saving variable frequency drives (VFDs), also known as inverters or simply as drives. VFDs can save 30 percent or more in energy costs, but they often induce shaft voltages that discharge through the bearings, leaving fusion craters—pits in the bearing balls and race walls. Concentrated pitting at regular intervals along a race wall can form washboard-like ridges called fluting, which causes excessive noise and vibration. By this time, bearing failure is often imminent.
.jpg)
Case Study
Dan Biby learned it the hard way. An ordeal involving 13 vertical hollow-shaft pump motors made him a believer in the vertical motor solution. Biby, an electrical engineer with an engineering consulting firm in Wichita, Kan., helped design a new water treatment plant. The plant opened in 2009 but shortly thereafter, Biby found himself in charge of a motor remediation project that would last more than two years. One after the other, the motors—all controlled by VFDs to provide adjustability in flow rate and pressure—developed serious electrical bearing damage. The Kansas City motor repair shop’s proprietary process solved the problems, but only after months of frustration. The motor manufacturer provided minimal help, replacing only the first motor that failed. The first shop Biby tried was unable to make successful repairs on the other motors. Eventually, he found Wilkins’ shop. By the end of 2011, all the plant’s 17 pump motors were refurbished with properly installed shaft grounding devices. To date, they continue to operate without problems. “We’ve learned a lot,” says Biby, who explains that his firm has adjusted its motor specifications so that: All new motors that will use VFDs must be equipped with shaft grounding rings. Shaft grounding devices must be factory-installed or installed by a reputable motor shop with expertise in the proper installation of the devices. If the shaft grounding devices are not factory-installed, a third party shall be engaged to test the installation to ensure that no damaging shaft currents are present. A warranty against VFD-induced bearing damage or failure for the life of the motor is required.More Success Stories
One municipal water supply plant in New Jersey had six 150-horsepower, vertical solid-shaft pump motors that were plagued with recurring fluting of the bearings. A representative from an electric repair shop said that insulating the bearings on the top and bottom and other methods never worked. Then the shop tried something new—installing the shaft grounding ring at the lower end of a motor with a brass insert to make sure that the ring was centered and protected from bearing grease. The shop’s crew also applied an extra-thick ceramic coating to the carrier at the upper end of the motor. Two of the six motors were upgraded using this method and reinstalled early in 2012. To date, everything is operating well. When the company sells a new vertical pump motor and a drive together, it sells them with the insulated carrier and the shaft grounding ring. Based outside South Bend, Ind., another company sells and services electric motors and industrial electronics. For two ailing, vertical hollow-shaft pump motors (60 and 150 horsepower) at a municipal water plant, the company sent the carriers for the top (thrust) bearings to a bearing company, which shipped them to Wilkins’ Kansas City shop to coat and machine.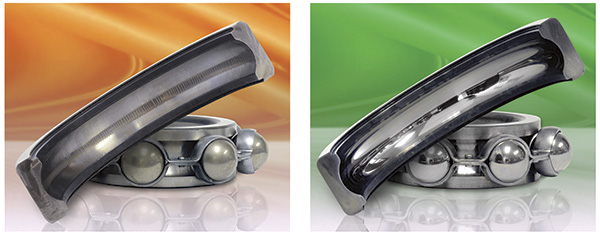
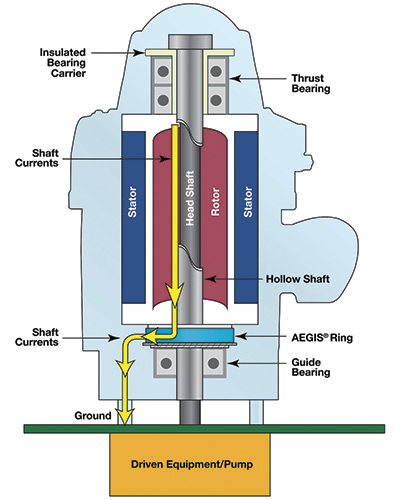