This article was written in response to the following question from a reader: Could you explain how an ANSI pump impeller’s clearance setting (both an open-vane impeller with back pump-out vane and a reverse-vane impeller with balancing holes) affects pump performance? What are the advantages and disadvantages of these impeller clearances? The main reason to use pump-out vanes (POVs) is to change the pump’s axial hydraulic thrust. In Figure 1, the impeller’s rotation results in dragging into rotation of the fluid in the gap between the impeller and casing walls. This is similar to the motion of a teaspoon in a cup or a disk spinning inside containment. The resulting motion is referred to as forced vortex. This type vortex sets-in in the front and back gaps—between the casing walls and the impeller front (shown on the right) and a back hub (shown on the left). The pressure distribution in the gap is parabolic—higher at the impeller’s outside diameter and gradually reducing toward the shaft center line.
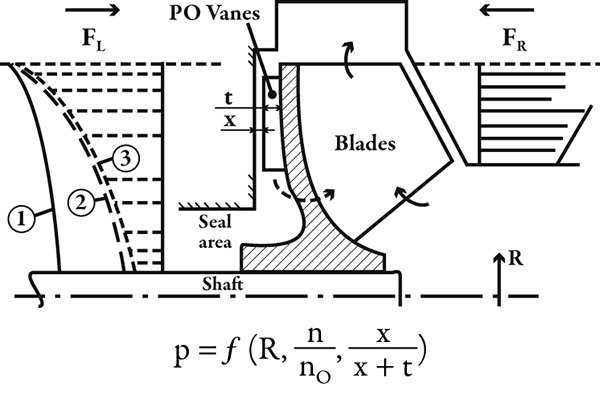