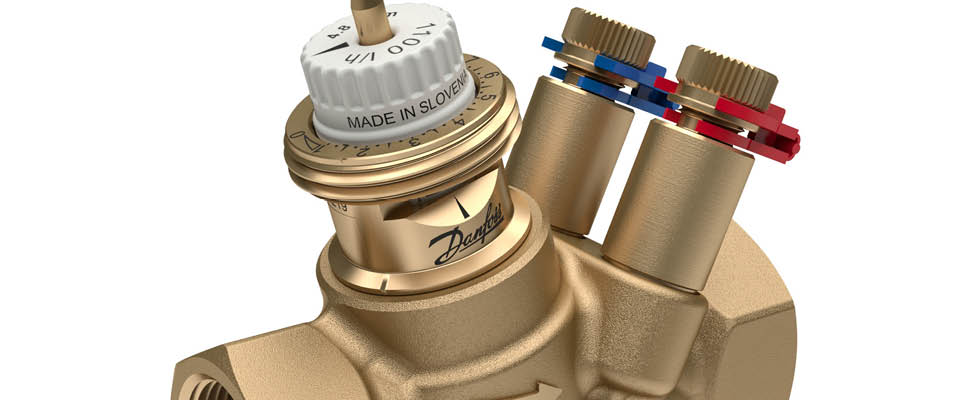
In hydronic heating, ventilation and air conditioning (HVAC) systems composed of traditional manual balancing and
control valve assemblies, system pressure is affected every time a valve changes its position. When the system pressure changes, the flow through all the valves reacts and affects the amount of heat transfer through each device, resulting in devices either receiving an excess or reduced amount of heat transfer.
To compensate for this effect, each device would signal the control valve to open or close appropriately, thus delivering the heat transfer requirement through the device.
Due to this chain reaction, HVAC systems with traditional valves can be inherently unstable, which leads to overflows and underflows at the terminal coils. In turn, this leads to wasted energy, suboptimal heat transfer, persistent system adjustments, premature failure of equipment and a less comfortable space for the building occupants.
If control can be maintained under these fluctuating and unpredictable system pressure conditions, there is no longer a need to worry about instability issues while meeting system demands. It so happens there is a valve that does exactly that: the pressure independent control valve (PICV), which is not subject to the normal pressure fluctuations in the system.
PICVs’ ability to maintain a constant flow rate, even with pressure differential fluctuations across the valve, is integral to building modern HVAC systems that efficiently regulate the flow of water or air in a building’s heating and cooling systems. PICVs are used to attain precise control and provide the opportunity to limit maximum flow in the system, regardless of whether they are installed on the supply side or the recommended location on the return piping. The PICV achieves this via multiple functions integrated in a single device—a motorized control valve, flow limitation and fixed differential pressure controller.
The pressure controller keeps a constant differential pressure across the control valve, and as a result, it automatically limits the flow. Mathematically, flow is defined as Cv x √∆P, and both the Cv (flow coefficient) and the ∆P (change in pressure across the control valve) are now constant values, which leads to the flow being constant. By opening and closing the control valve, the flow through the valve is controlled in a predictable manner.
Installation
Balancing the installation is now less intensive with PICVs due to its designed function as an automatic balancing valve (adapts to any system load) and the settable flow adjustment, which could be set without measuring. The setup process with these integrated functions helps to reduce the involved procedures that are necessary for manual balancing valves. The authority is also not relevant anymore because it is always one.
The installation of PICVs also improves the control valve authority both in the selection and its operation under varying system pressure. Authority is expressed as a ratio of the control valve’s differential pressure when fully open divided by fully closed and can be expressed as a percentage.
The authority of the control valve in relation to its location within the system will impact the control response to demand requirement. In terms of the PICV, authority is one due to the dynamic pressure controller maintaining a constant differential pressure across the control valve. This level of control and response translates to improvement in maintaining designed requirements and potentially reducing the amount of energy needed to meet the demands.
Costs
If you compare the PICV solution versus manual balancing valves and control valves, a PICV is competitive. The initial PICV investment might be slightly higher, but it can be earned back with savings on commissioning and lower energy consumption. Any maintenance needs due to unstable flow controls can also be diminished, reducing operational costs.
Case Study
A university wanted to investigate an alternate HVAC design that could improve the stability of their system. When a PICV functions properly, changes in system pressure will not cause flow changes through the valves, thus solving the instability issues.
The university installed one PICV in their facility and carefully monitored the results. They selected a hot water line supplying 240 F to two plate-and-frame heat exchangers that make hot water for a 160,000-square-foot academic building. This line has an existing two-way full port ball valve and a manual balancing valve on the primary side of the heat exchangers. In their previous experience, this line exhibited the classic characteristics of typical HVAC systems—instability issues, large swings in temperatures and valve “hunting.” For the purposes of the test, they replaced both the ball valve and the manual balancing valve with a single PICV and actuator. Their complete test setup comprised of the following items:
One 4-inch PICV (167 gallons per minutes [gpm]) with a matching modulating actuator (2-10 volts [V]).
The PICV was installed on the primary side of a plate-and-frame heat exchanger using medium temperature hot water (MTHW) at 240 F delivering hot water to the building.
An ultrasonic meter was installed on the pipe to measure flow rates. This meter has a rated accuracy of +/- 2%.
Their automated logic controls WebCTRL system was used to control the valve and record the flow meter measurements.
It is important to note the tests were conducted on a live system, not in a laboratory setting. The test PICV was used to control the temperature of the water to an occupied building under normal operating conditions.
The results of their analysis showed as long as the pressure across the valve body is within the stated pressure range and the valve position is more than 10% open, the flow through the valve is almost perfectly linear, regardless of system pressure. After several months of use, the performance was excellent. The control stability has been outstanding, as the valve maintains temperature well with little valve movement. Normal changes in the plant system pressure do not affect the valve operation, and this is especially evident at minimal positions where their traditional valves had been particularly unstable.
Ultimately, the result of improving the stability of their hydronic system will include energy savings, better temperature stability for their building occupants and less valve and actuator maintenance. At the university, they have made PICVs a standard in all their future new builds and renovations.
The PICV is a concept that has been designed from the ground up for variable-flow systems and the unique challenges such systems present. It is possible to solve these challenges by doing extensive calculations, precise engineering and time-consuming tuning of the control parameters. However, in the complex building process that involves many stakeholders and external decision-makers outside the engineers’ control, can it be ensured that precision engineering is
being implemented?
Pressure independent valves reduce the complexity of designing the system and can help reduce the risk of unstable controls and low ∆T (the difference between return air temperature and supply air temperature) issues, leading to simplicity and robustness of the design. The PICV has proven itself to be a reliable technology over the last decade.