Bearings in centrifugal pumps support hydraulic loads imposed on the impeller, the mass of the impeller and shaft, and loads caused by couplings and drive systems. They also keep axial and radial shaft deflections within acceptable limits for the impeller and shaft seal. Handling all these functions—often in difficult process conditions—bearings are subjected to adverse forces that can potentially reduce their service life and reliability. Radial shaft seals serve as critical elements within a pump’s bearing and sealing system. Seals will effectively offer a “first line of defense” for bearings in pump applications. They retain lubricants or liquids, exclude contaminants, separate fluids and confine pressure. With pump bearings and shaft seals continually tested as an integrated system, the industry responded to the many challenges with solutions engineered to withstand even the most difficult operating conditions.
Bearing Operating Conditions
Centrifugal pump bearings are typically subjected to high axial loads, marginal lubrication and high operating temperatures and vibration—all while attempting to minimize friction. Friction, if uncontrolled, can result in power loss, excessive heat generation, increased noise and/or wear, and premature bearing failure.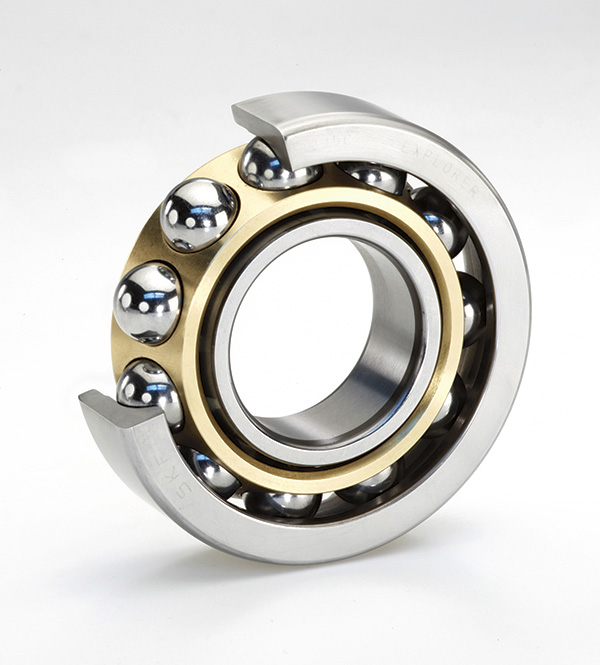
Angular Contact Ball Bearings
Single-row, 40-degree angular contact ball bearings represent the most popular American Petroleum Institute (API) pump thrust bearings currently in service. They are generally used in moderate-speed centrifugal pumps in which high thrust loads can be anticipated. The bearings are normally mounted in back-to-back paired arrangements to accommodate reversing thrust loads and to provide adequate shaft support. This promotes long mechanical seal life. Versions designed with robust, machined brass cages can run particularly well in applications in which thrust loads vary greatly during operation and periods of ball skidding are likely. These bearings also resist destructive vibration forces when cavitation occurs. Double-row, angular contact ball bearing arrangements are used extensively as the primary thrust bearing in American National Standards Institute standard centrifugal pumps and some older API-style pumps. The most effective types feature a Conrad-design; Annular Bearing Engineer’s (ABEC) 3 (P6) precision tolerances; 30-degree contact angle per row; one-piece, heat-treated pressed steel cages; and multiple sealing options. Because their contact angles diverge outwardly, the bearings exhibit greater rigidity and increased resistance to misalignment. Design variations of these types are increasing, including:- Steeper 40-degree contact angles to deliver increased thrust capacity
- Machined brass cages to impart robust performance in heavy-duty and poor lubrication conditions
- Reduced axial internal clearances to promote load sharing between the two rows of balls and a reduced possibility of skidding in the inactive ball set
- ABEC-3 (P6) tolerances to gain better control of the bearing’s mounted condition and promote smoother bearing operation
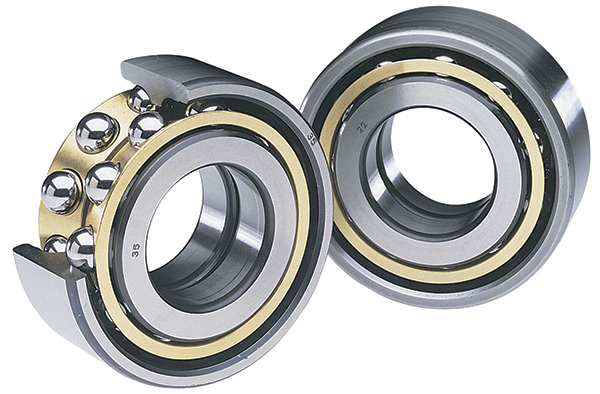
Advanced Materials
Other bearing solutions for pumps benefit from advanced materials. Hybrid bearings are equipped with balls or rollers made of silicon nitride, a ceramic material with characteristics that make it a good choice for pump applications requiring high speed, high stiffness and electrical insulation. Bearings with injection-molded, glass-reinforced polyetheretherketone (PEEK) combine strength and flexibility with resistance to high temperature, chemicals and wear. PEEK cages are ideal for pumps in which the bearings are lubricated with light hydrocarbons, liquefied gases (cryogenic) or fire-safe hydraulic fluids and will often be integrated with hybrid bearings or with super-tough stainless steel rings. The combination offers protection from damage caused by poor lubrication and exposure to chemicals, creating reliable, robust and low-energy pump designs.Sealing the System
Bearing seals in centrifugal pumps must prevent potential contamination and loss of effective lubrication or lubricant properties. Without effective sealing, contaminants (solid or otherwise) may infiltrate the area of a bearing, invade the lubricant and bearing, and shorten bearing life.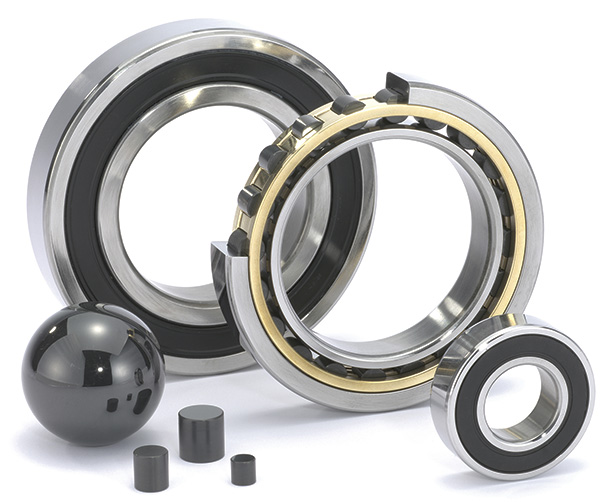