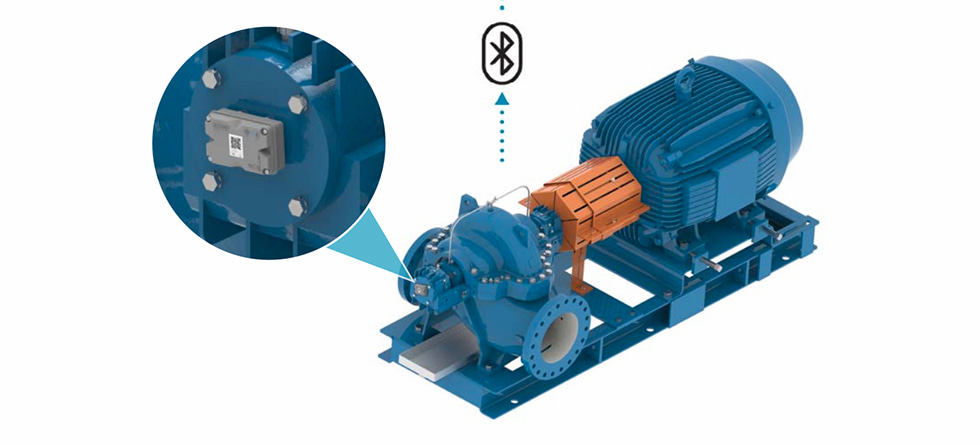
Professionals across the water pumping and application industry face significant challenges, many of which come from forces beyond their control. From climate- and weather-related issues, to increasing complexity in water system management, there is a growing need for digital solutions as an essential strategy to address these challenges and assist in the proper operation, optimization and maintenance of machinery.
According to the State of IoT–Spring 2023 report, there were more than 14.3 billion internet of things (IoT) devices connected in 2022, with this number projected to rise by 18% to 16.7 billion in 2023. It is unsurprising then that digital solutions like sensors, smart equipment and data analytics are becoming increasingly adopted by maintenance and operating professionals across their water applications.
In addition to providing real-time visibility into water management processes, IoT devices empower them to monitor performance, detect issues and make long-term, data-driven decisions that can extend the life cycle of their assets.
The latest industrial IoT technology enables even more advanced access to data for monitoring, diagnostics and predictions and presents an efficient, cost-effective method to optimize pump systems, leading to smarter water operation.
Condition-Based Monitoring Shifting System Optimization From Reactive to Proactive
Maintenance of equipment represents a significant aspect of the total cost of water operations, yet the hidden costs of such maintenance are often underestimated. These can include higher energy usage, decreased asset life span and increased downtime caused by failures. To effectively reduce hidden costs, a shift from the traditional reactive “fix it when it breaks” approach to a proactive condition-based approach is required.
To support this shift, professionals are increasingly turning to condition-based monitoring to support proactive and preventative maintenance. Condition-based monitoring uses sensors to measure a machine’s status while in operation to provide health guidance and maintenance advice.
Small changes in vibration or temperature will often serve as indicators that a pump is developing mechanical issues. Detecting these subtle changes early on allows operators to take preventative actions which can stop a failure from occurring. This approach can reduce the costs associated with unexpected downtime and make efficient use of the operator’s time and resources.
Considerations of Implementing Condition-Based Monitoring
Traditionally, condition-based monitoring systems have had implementation challenges such as high initial cost, software requirements and the need for extensive training to analyze the data correctly. Because of this, it is important to keep the following considerations in mind when purchasing a condition-based monitoring system.
Overall costs
Finding easily deployable systems can minimize installation costs and eliminate the need to prioritize which assets are monitored. Additionally, systems with wireless self-contained sensors and replaceable batteries save replacement costs over the product lifetime. In many sensors available on the market, a dead battery means discarding the entire sensor.
However, with a replaceable battery, the sensor can function for three to five years, and once the battery is dead, it can be easily replaced. This allows the sensor to be up and running within minutes without any data loss.
Minimum training
Sensors that can be installed, configured and begin monitoring assets within just a few minutes require minimal training. Additionally, systems that provide the analyzed data in a format that is easy to understand eliminate the need for operators to possess specific knowledge or training in vibration analysis or data analytics to maintain and optimize a pump system. Some sensors will give visual LED indication if a potential failure has occurred, like utilizing a traffic light system of green, yellow and red to indicate acceptable vibration. This allows potential failure modes to be identified almost immediately without the need to establish a baseline of data over time.
Bluetooth and mobile apps
Some digital asset management solutions come configured with Bluetooth and Cloud capabilities through a mobile app and can transmit the data of a potential failure to the operator’s mobile device when it is within range to enable even more powerful monitoring. What is more, a cellular gateway enables the transmission of data to an operator’s device even when outside of Bluetooth range. Systems with compatible apps provide convenient access to the health and status of an asset. Some allow for long-term data storage, contributing to health trends and maintenance logs for a pump system, as well as reporting features and reminders when maintenance is required.
Condition-based maintenance does not reduce the likelihood of potential failure, nor does it stop failure from happening altogether. Rather, it intervenes before a catastrophic failure occurs, enabling operators to perform maintenance and the opportunity to reduce life cycle costs and optimize the operation of their pump systems as a result.
IoT is a transformative technology. By harnessing the power of interconnected devices, data analytics and remote monitoring, operators are empowered to make informed decisions, optimize their water management processes and achieve their sustainability goals.
The ongoing implementation of industrial IoT will be key to future improvement in machinery operation and maintenance. It will integrate whole systems and various equipment to facilitate the most efficient ways for them to work together, ultimately optimizing the performance of entire buildings.