Flexibility and plenty of room for movement ensure successful, reliable sealing.
11/05/2014
The criteria for expansion joint selection for fluid piping applications focuses on the expansion joint’s quality, durability and capabilities. To ensure that the rubber expansion joint’s installation provides optimal service life, operators and maintenance personnel must consider specific conditions and take a systematic approach. Piping systems require some degree of flexibility. Inadequate flexibility can lead to a catastrophic, potentially life-threatening system failure, making flexibility an important consideration when selecting an expansion joint.
Joint Selection
Rubber expansion joints, which have all-directional movement capability, provide maximum flexibility based on the system requirements. Rubber expansion joints are designed to handle axial, bidirectional lateral, angular and torsional movements of a piping system. This movement may be caused by thermal growth or piping misalignment during the construction stage. Rubber expansion joints can also absorb vibration that occurs with fluid-borne noise or mechanical equipment rotation. The rubber expansion joint in a fluid piping system provides these benefits in the smallest space possible, keeping the piping system’s size and overall footprint at a minimum. Alternatives, including large pipe loops or metal expansion joints, cannot provide this space-limiting benefit. With the advent of piping systems that use more high-density polyethylene (HDPE) pipe or installations with lug-style butterfly or wafer check valves, operators must be mindful that rubber expansion joints seal better against full-face flanges (preferably flat-face flanges). For these reasons, reliability of the rubber expansion joint in the piping system is key. When selecting a rubber expansion joint, personnel should review piping and equipment attachments.Joint Installation
Sealing spool-type rubber expansion joints against HDPE pipe with metal flange adapters or pump flanges with lug-style connections can create sealing issues because the sealing area of the joint is reduced significantly. This sealing difficulty can also be amplified when the rubber expansion joint is installed in an offset condition. When installing rubber expansion joints against HDPE (see Image 1), leakage during operation or surge conditions and failure of the rubber element against the leading edge of the HDPE pipe can occur.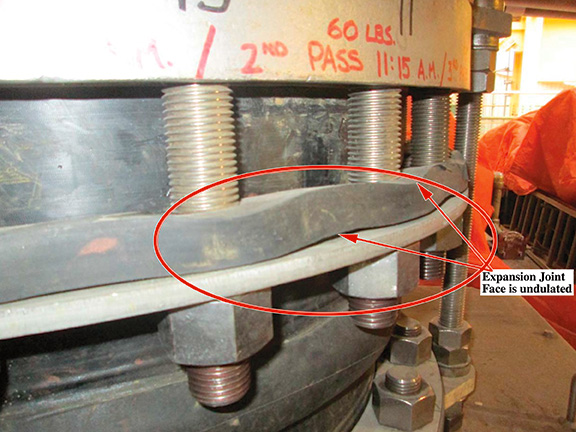
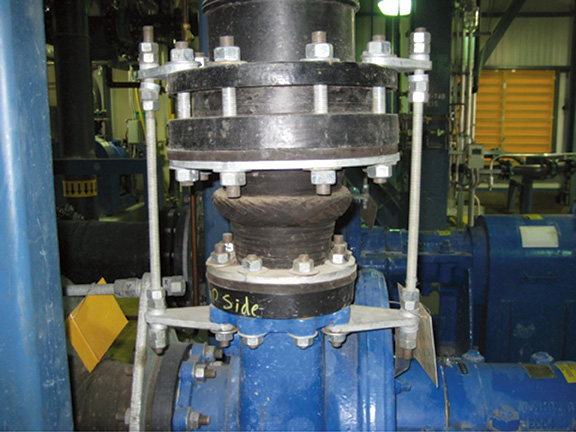
We invite your suggestions for article topics as well as questions on sealing issues so we can better respond to the needs of the industry. Please direct your suggestions and questions to sealingsensequestions@fluidsealing.com.