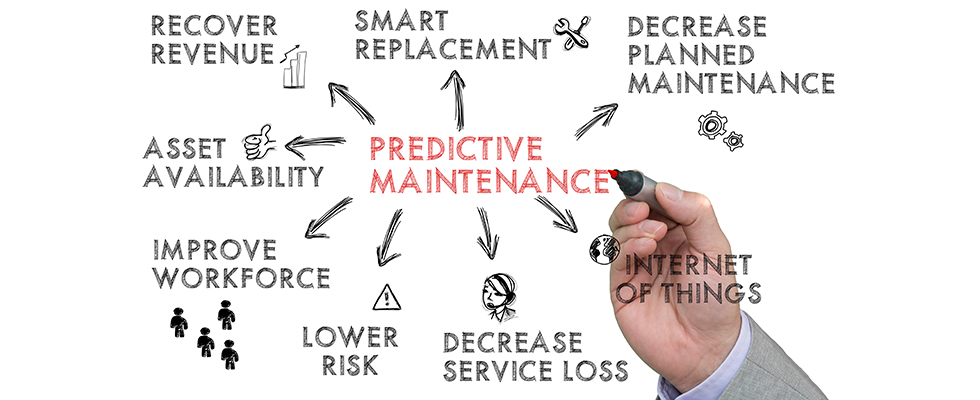
Predictive maintenance is nothing new to many facility managers. Today, building managers, facility operators and others are discovering how beneficial and cost-efficient it is to know what is happening inside their infrastructure and when disaster might strike. Shutting down operations for hours, days or weeks in the middle of peak production can be costly, and pinpointing the issue without automated help can turn into a long and tedious game of guesswork with multiple contractors, consultants and engineers.
The internet has ushered us into the future, and facility managers have not been left behind. Predictive maintenance has been making steady strides, progressing to help facility managers have a more comprehensive view of their systems and how operations can improve.
Why Facility Managers Need Predictive Maintenance
Better understanding of operations: The proper tools can offer in-depth insight into how infrastructure really operates on a level not visible to the eye. Every facility manager has a basic knowledge of the equipment under their governance. The best has a deep understanding of the functionality of their infrastructure.
Two steps ahead: A richer understanding of the ins and outs of a facility paves the way for management to foresee issues. Everyone has been in the position where some technology, be it a smartphone or an elevator, suddenly stops working without a clear reason. Being caught with a broken phone on an empty weekend is one thing, but being stuck in an elevator during an emergency is another. If facility managers could predict these issues far in advance so they could be tended to, the issue might never actualize. Nobody wants to be stuck with malfunctioning equipment on a Monday morning; every facility manager wants to be aware of potential failure with weeks’ notice if possible.
Optimization: We all push the gas a bit harder when we want to go faster. Facility managers want their systems running at full capacity, so their systems need to be optimized. When stepping on the gas, some people might not be aware their car is not made to handle going the speeds they want it to. Likewise, perhaps facility managers want to maximize the output of their system, but the system may already be running at its full potential. The right data from the right sensors can bridge this gap and inform users just how hard they can push their equipment and for how long this intensity can be maintained.
All these reasons have one common denominator: they help businesses earn more and spend less.
What Is the Future of Predictive Maintenance?
One hundred years ago, it was a farmer’s dream to have a machine that could pick and sort crops. Now, it is a reality. One hundred years in the future, facility managers will have the luxury of simplified, automated, intelligent technology that makes their work easier and more efficient. The advent of predictive maintenance is looming with the goal of removing guesswork and reactivity from operations. This translates to less time spent trying to deduce the source of an issue within any facility, thereby reducing costs.
Pinpointing an issue is being made into an exact science with the help of automated and artificial intelligence. Some companies focus on the predictive maintenance of tomorrow, eliminating the need to constantly upgrade. These companies are focusing their efforts toward hardware and software that can sense issues by measuring voltage and current.
Voltage and current waveform data can be analyzed to provide a range of useful information, not unlike an X-ray scanner for equipment. This data contains unique electrical signatures that provide information about the state of operations, the mechanical condition of equipment, the utility power quality and the functioning of any devices upstream from the point of measurement. From all this information, facility managers have a greater understanding of the granular details of their operations to better see the past, present and even future of their operations.
Preventative Maintenance Past
It is common to find predictive maintenance that relies on vibrational patterns in facilities. These devices provide insight into how equipment operates and can grant facility managers the opportunity to see how they can improve their systems or where they might encounter issues.
Vibration sensors can take a while to install and have a shorter warranty because they are mechanical in nature. They are good at condition monitoring but lack the ability to diagnose precisely if the vibration is originating from the source or load.
Though some predictive maintenance is better than no predictive maintenance, businesses of the future will be tracking data that is more granular, more in-depth and with greater capabilities and accuracy.
When it comes to innovation, engineers will often draw from their real-life experience to inspire change. Those who worked for decades alongside facility managers have seen all kinds of issues and are well aware of what facility managers want and need to improve their operations. They themselves have felt shorthanded with the technology available to their clients.
Putting trust in a company to detect system failure is a big demand; putting trust into known and established maintenance is easy. If a maintenance operator created a system that would ease their workload and provide users with the tools to constantly monitor, rather than perform regular and reactive maintenance, it would inspire more trust in these tools.