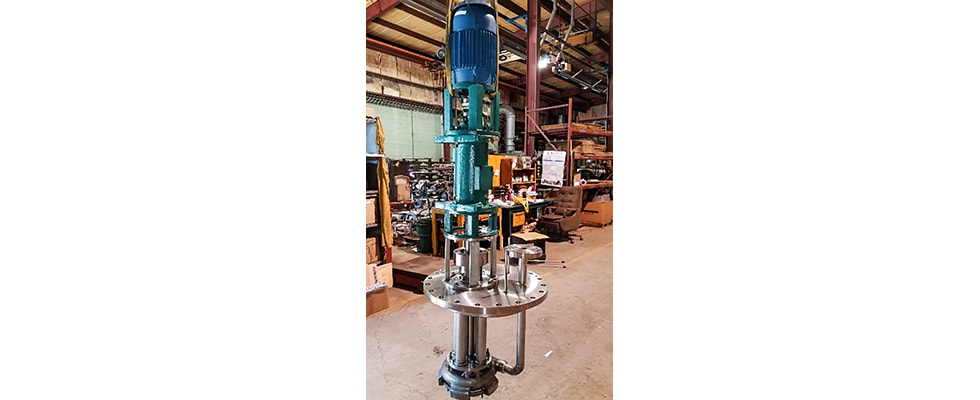
Probably no class of equipment for industrial application requires such a high degree of coordination between the design, materials of construction and experience in molten salt as do pumps used in high-temperature molten salt applications. It is only through experience and lessons learned that these three elements can be satisfactorily blended together.
Fully understanding the requirements of the application, temperatures and the salt blends being pumped will be the starting point for selecting the type of pump that will best meet all the criteria needed for a successful high-temperature molten salt system. Meeting the flow and head requirements for a given system is only a small part of understanding the requirements for a high-temperature pumping system. There are many details that must first be reviewed, researched and evaluated, as this single piece of equipment is the heart of the system. If it does not run properly, the system will not operate satisfactorily and may even fail.
It is critical the design and materials of construction support and strengthen each other. High-temperature applications take both these elements to their limits. From the standpoint of design, simplicity and ruggedness is needed to meet the longevity in life these critical pumps require. It is recognized the conditions under which high-temperature molten salt pumps will operate are difficult and no single design is adaptable to all of them.
Molten salt pumps must be designed to meet the individual requirements of the system they are used in. Many aspects must be considered when selecting a pump to handle high temperature molten salt. Understanding the total system requirements will ensure a safe and long life between rebuilds of molten salt pumps.
The high temperatures will weaken the strength of all materials. It is critical the correct materials and designs are looked at together. Often, the materials used can compensate for weaker designs, which have been required due to the space or type of pump used. The reverse is also true. There are times when the design will compensate for weaknesses in the materials due to high temperatures. Understanding this relationship is critical in selecting the right pump for the application.
Based on the operating temperatures of the system, the materials can be divided into four major categories. Image 1 is only a guideline and not respective of a specific application.
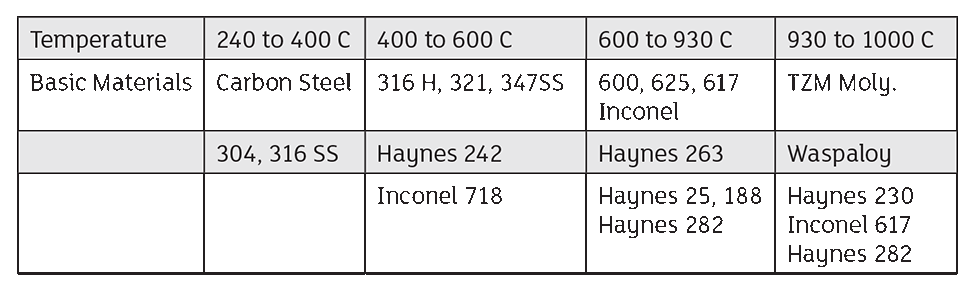
Molten salt pumps can be categorized into four major pump styles. Image 2 is just an outline of standard pumps not related to any specific application.
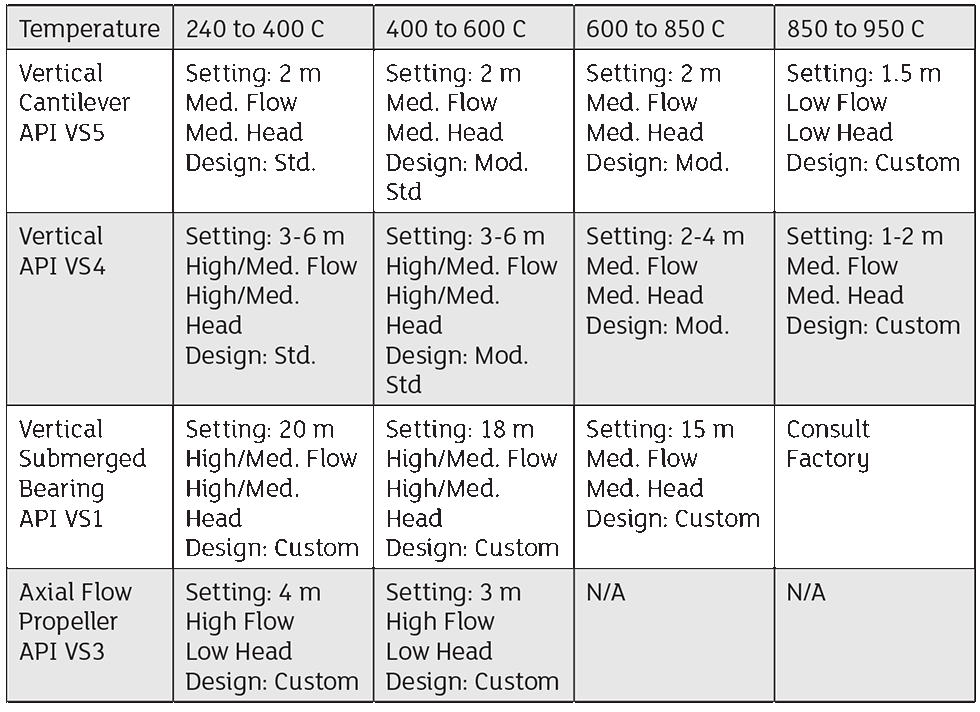
Vertical cantilever pumps: These offer many different features, including several types of mounting arrangements. The most common is a round design. In tank mounting, as well as mounting the pump outside of the tank as an inline pump, gives system designers great flexibility. Vertical cantilever pumps (VS5 vertical cantilever type pump according to American Petroleum Institute [API] 610) have no bearings below the main mounting plate. Cantilever pumps only offer single stage designs. The main disadvantages of the cantilever design are the limited pump setting lengths and the limited liquid levels for starting and operating the pumps. Cantilever pumps can be expensive based on the bearing pedestal and shaft size needed to reach a limited setting depth.
Vertical pumps: These have a lower radial or foot bearing. They also have several mounting arrangements, both inside the tank and outside the tank. Vertical single volute pumps are a VS4 line shaft pump type according to API 610, but can be offered with multistage volutes as an option. They have longer settings than the cantilever and are less expensive than cantilever designs.
Vertical submerged bearing pumps: These are the longest design offered. They can only be mounted in the tank. Vertical submerged bearing pumps can offer multistaged volutes. They are capable of matching many different application requirements and setting depths. There are two basic designs of this type of pump: the vertical turbine (VS1 wet pit diffuser pump type according to API 610) with a common discharge column in which the shaft is centered in the column or the vertical pump (similar to the VS4 line shaft according to API 610) with an independent discharge line.
Axial flow pumps: Axial flow pumps are an API VS3 design. Their applications are limited to low heads and high flows. Chemical reactors are one of the main applications for this type of pump. Their special design permits the rotating assembly to be removed from the pump shell without removing the suction and discharge piping. Axial flow pumps of this type can only be mounted with the shaft in a vertical up position. After disassembly, this pump is one of the easiest to rebuild.
5 Features of High Temperature Molten Salt Pumps
1. Sealing of the pump’s rotating shaft is critical
Moisture getting to the salt tank will cause many problems, such as solids forming and high corrosion. Egress of salt vapors can cause major corrosion problems or seizing of the shaft from frozen salt.
Standard sealing designs offer a combination labyrinth and packing with a double nitrogen purge. There are gas mechanical seal options from some OEMs. It is critical to understand the heat migration coming up the shaft to estimate the operating temperature of the seal. These seals may need to be elevated above the mounting plate to prevent overheating them.
2. Mounting plate design with thermal barrier
The mounting plate thickness is oversized to ensure adequate strength at high temperatures due to the reduction in yield strength and elastic modulus at temperature. Weakening of the mounting plate can cause discharge piping strain
and leaks. The sealing surface is machine-finished to ensure flatness and levelness, and for effective salt vapor and ullage containment
Note: The vessel must be designed to support weight of pump, mounting plate and motor at high temperatures.
3. Heat migration up the shaft and column assembly
Heat fans are required to reduce the temperature migrating up the shaft while the pump is running. However, when the pump is not running, the heat can migrate up the shaft quickly.
4. Capability to operate at shut-off for short period of time in case of a freeze-up in the system
Freeze-up in molten salt loops are one of the main problems. In vertical cantilever pumps VS5 designs, the bypass on the backside of the volute works as a pressure relief system.
5. Thermal and stress modeling of pumps and its mounting plate
It is critical to understand both the axial and diametral thermal expansion the pump will see during operation. These stresses can break structural welds, fasteners and discharge piping.
Thermal analysis can tell us where we need to monitor for cold spots that could freeze salt and hot spots where unwanted distortion could occur.
Additional Features Required in a Molten Salt Pump
- pump must be 100% self-draining
- pumps must rise to shut-off
- impeller must be adjusted with pump installed in molten salt
- right bushing sleeve combination must be selected for long shafted pumps
- critical speed is 25% above operating speed
- thrust bearing replacement may be done without pulling the pump
- vibration and temperature monitoring
When evaluating pumps that are the heart of a critical application, such as a molten salt system, the more proven experience in building and supplying molten salt pumps a vendor has, the less risk there is.
Keep in mind, long shafted pumps are built for difficult applications. High-temperature molten salt may be heavier than pumps built for water or chemical applications that are trying to be used for high-temperature molten salt. It is critical the design and materials of construction support and strengthen each other. High-temperature applications take both elements to their limits. From the standpoint of design, simplicity and ruggedness is needed, plus flexibility to meet the longevity in life these critical pumps require.
The marriage of the pump, motor and variable frequency drive (VFD) to a given application is not a simple task. The equipment costs versus operational cost versus maintenance cost versus risk must be researched in depth by both engineering and purchasing. The result may be that low price is not the best choice and risk can only be eliminated by experience and testing.
Only use proven components such as pumps, valves, heat exchangers and monitoring systems that have a history of being used in molten salt applications. Ask for reference lists from suppliers.