These advancements are important to the growth of biogas as an energy source.
KROHNE Inc.
02/17/2017
As interest in biogas grows, industry is paying more attention to measuring biogas flow, which has long been a challenge in process measuring technology. While high water and carbon dioxide (CO2) content makes biogas a demanding medium and a difficult measuring task, a new generation of ultrasonic flow meters is helping to make biogas measurements stable and manageable. One type uses the time transit differential method to guarantee flow measurement with a high degree of long-term stability regardless of the gas composition.
The Rise of Biogas Energy
According to the American Biogas Council, the U.S. has about 2,000 sites producing biogas, with another 12,000 considered ripe for development.1 In the country, biogas is promoted as an alternative to conventional fuels because it increases energy security and produces fewer greenhouse gas emissions while providing other environmental and economic benefits.2 Europe has more than 10,000 operating digesters. According to Germany’s Biogas e.V., more than 1,000 biogas plants were built in 2011 in Germany. More than 7,000 sites generate electrical power of more than 3,000 megawatts (MW), and that number is rising. Within a few years, biogas has reached a share of about 3 percent of the energy consumption in Germany. Traditionally, biogas in these plants is a product of the fermentation of sludge from wastewater treatment plants and landfills. Today, other bio feedstock such as waste from cattle farming and other agricultural operations is also used to produce biogas. This gas is generally used in combined heat and power plants to directly generate electricity and heat using a gas engine. Biogas is reworked to grid quality to supply into the gas grid. Biogas is also being used as an alternative vehicle fuel.Measuring Methane Content
Knowing methane (CH4) content is crucial when using biogas. Operating gas engines in a combined heat and power plant smoothly and efficiently can be guaranteed only if the biogas has the right minimum methane content. For this reason, the plant operator must be familiar with the composition and quantity of the biogas. This is especially true when biogas deliveries to gas grid operators are used in custody-transfer applications. Because the methane content of biogas can vary greatly, plant operators rely on continuous and accurate information about the biogas. But this dependence on data is exactly what creates a challenge for many operators today. Generally, these operators take multiple measurements in a biogas plant—for example, before and after the storage tank. However, successfully mastering the measuring task is no easy feat. This is largely because of the demanding measuring parameters associated with biogas applications.Measuring Challenges
Depending on the bio feedstock and process, biogas contains only about 50 to 70 volume percent methane. The remaining portion is made up of 30 to 50 volume percent CO2 and smaller amounts of oxygen (O2), hydrogen sulphide (H2S) and nitrogen (N2). In addition, the biogas can contain up to 5 to 6 volume percent free liquid water because during fermentation the biogas is saturated with water, which then gets into the pipeline after cooling down and leaving the fermentation tank. When dissolved in water, H2S creates a corrosive solution in the pipeline. In addition to high moisture, operators must consider resistance to corrosion when selecting a measuring device. Another concern is bacteria can be deposited in the flow meter during biogas measurement. The temperature ranges from slightly above the ambient temperature to 122 F, and the pressure is typically 20 to 25 inches H2O. Process conditions, however, can vary greatly. For example, sudden temperature drops can occur when new sludge is fed into the fermentation tank. Depending on what is required, a measuring device should cover the widest possible measuring range. Most biogas plants—in the wastewater industry, for example—have a pipeline diameter of 2 to 8 inches. Larger sites for biogas production can require larger nominal sizes (12 to 16 inches). Flow measurement technology companies have attempted to meet these special measurement requirements with a variety of measuring methods, but a satisfactory solution is still difficult to find for many plants. For example, orifice plates often are not suited for biogas measurements under the outlined pressure conditions because they cause pressure losses and may interfere with the process, and the use of vortex flow meters is limited to measurements at low flow velocities. Thermal mass flow meters are still the most commonly used measuring devices in the biogas industry, but these measuring instruments also suffer from a considerable handicap: Water in the biogas line considerably restricts its performance. Based on their design, ultrasonic flow meters are well-suited for biogas applications because they guarantee a full transit without loss of pressure or any negative effect on the flow, and they can cover a wide measuring range. In the past, however, they have been challenged by high water content. In addition, the high CO2 content typically present in biogas flows had a negative effect on measuring stability because CO2’s molecular structure can significantly decrease the dispersion of ultrasonic signals. Finally, the cost to purchase these devices is still comparatively high, which has made the use of ultrasonic flow meters unattractive in many cases.State-of-the-Art Technology
Early experience with biogas applications has taught the industry much, especially in the area of ultrasonic flow measuring technology. Through investment, research and development, leading measuring technology manufacturers have produced a new generation of ultrasonic flow meters that specifically targets the requirements of biogas applications while remaining affordable. This measuring instrument, which functions according to the time transit differential method, guarantees flow measurement with a high degree of long-term stability regardless of the gas composition. The solution is maintenance-free and immune to deposits. It has a special signal converter design and features high signal strength. The National Association of Corrosion Engineers (NACE)-approved Grade 29 Titanium transducers provide excellent corrosion resistance against H2S. An enhanced digital signal processor (DSP) also allows for better detection of small acoustic signals strongly dampened by high CO2 content. Meter construction eliminated effects from water on measurement. The device does not have limitations such as regular recalibrations, pressure loss or flow range restrictions. To make various measurements comparable, the standard volume can be measured based on temperature and pressure inputs to the converter. Experience has shown that the device can perform stable and accurate biogas measurements, which is what plant operators need to ensure the viability of their biogas operations.Calculating Methane Content
The measuring device features an integrated calculation of the methane content, which is critical to efficient gas engine operation when biogas is used. The calculations are taken from an actual wastewater treatment plant application example.The molar mass (M) of a gas is determined according to Equation 1.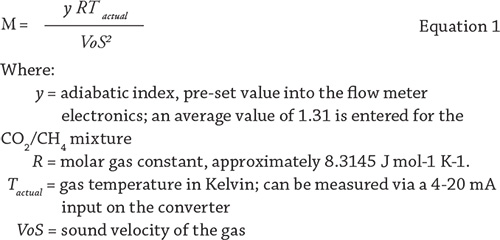
References
1. Current and Potential Biogas Production, American Biogas Council, http://www.americanbiogascouncil.org/pdf/biogas101.pdf , retrieved 8/12/13.
2. Renewable Natural Gas (Biogas), Alternative Fuels Data Center, U.S. Department of Energy, http://www.afdc.energy.gov/fuels/emerging_biogas.html, retrieved 8/12/13.
See other Flow Meters articles here.