Standards, better computational power and VFDs are creating more efficient and customized solutions.
IPC
09/30/2016
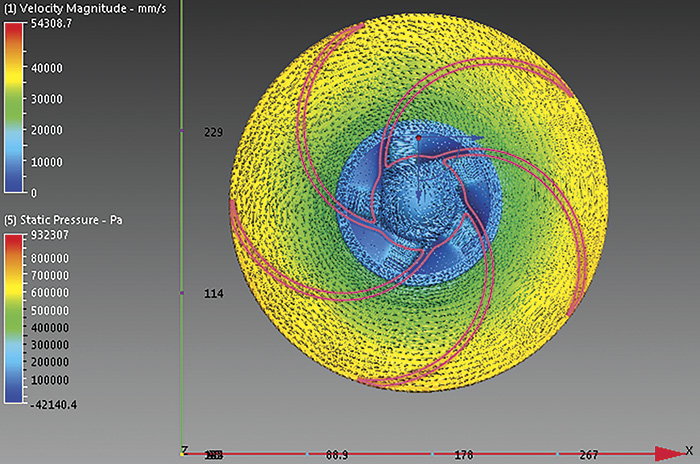
Massimiliano Di Febo is an operation manager at IPC. He may be reached at massimiliano.difebo@ipc-eng.com.
Pasquale Paganini is a technical manager at IPC. He may be reached at pasquale.paganini@ipc-eng.com.