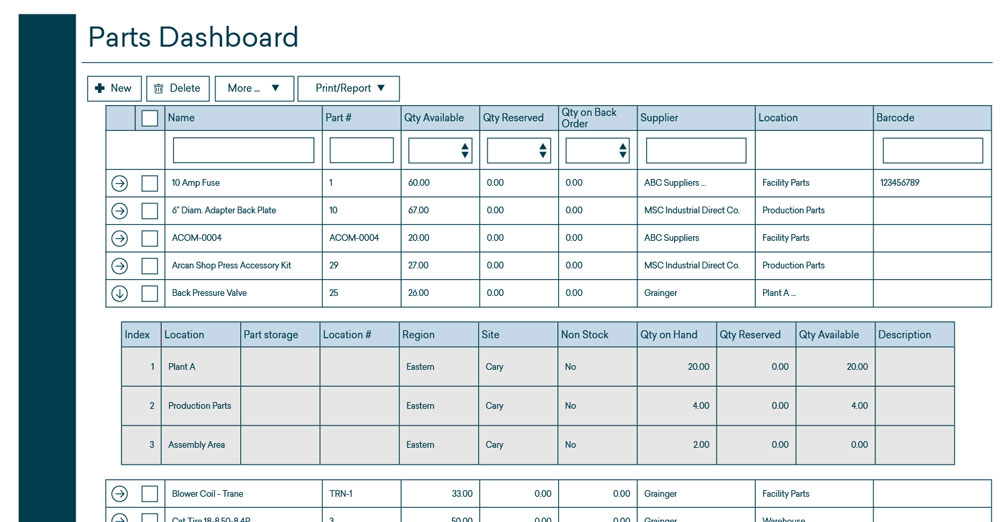
Having control and readily available spare parts and raw materials just when they are needed is a profitable proposition when it works. However, these days there are industrial, societal and market factors way beyond users’ influence that make it difficult to achieve this goal. Manufacturers can mitigate these challenges by creating lean, efficient and intelligent operations and adapting to the unprecedented and constant disruptions brought on by events like the COVID-19 pandemic, Suez Canal blockage and the United States/China trade war. While there will always be some level of supply chain disruptions, this perfect storm of disruptions forced manufacturers to reconsider how achievable just-in-time (JIT) manufacturing is.
Right now, JIT manufacturing is not about being fast—it is about being intelligent, realistic and proactive about the time it takes to receive vital parts and materials. This all starts with an asset management plan that analyzes overall maintenance operations and ensures organizations can retain production and business continuity in these uncertain supply chain times.
There are numerous benefits to lean JIT manufacturing processes in more stable times and with relatively lower levels of parts and materials, like saving valuable space, simplifying ordering and lowering materials holding costs. JIT manufacturing can be a powerful tool. Organizations need to consider supply chain issues, variability and uncontrollable delays. In good times, and even more so in bad times, organizations need to have visibility into their parts and procurement processes, starting with solid parts management. Manufacturing organizations should always have visibility into the following: a complete catalog of parts, where parts are stored, where parts are ordered from, what is on order or on backorder, parts with low supply (with ordering buffers that can accommodate the difficulties of finding parts) and what parts are needed for upcoming preventive, predictive and possible corrective maintenance.
Spare parts management is a key part of a computerized maintenance management system (CMMS), which helps manufacturers achieve an effective JIT manufacturing process. A CMMS optimizes maintenance operations through a combination of features including managing assets, preventive and corrective maintenance work orders, safety, compliance and spare-parts inventory. If users manage and optimize overall maintenance operations aided by CMMS, the impact of a poorly functioning supply chain can be reduced.
In general, a well-implemented CMMS system will move organizations away from firefighting corrective maintenance and toward a smoother and more controllable preventive maintenance environment to support when the supply chain is challenged. In maintenance operations, a stockout is where an asset is down for maintenance—preventive or corrective—and the necessary spare part for remedy is not in-house, extending downtime. This is a frustrating and profit-killing problem that is exasperated in today’s supply chain climate, and organizations need to avoid stockouts wherever possible.
Knowing the spare parts needed for upcoming preventive and possible unexpected maintenance is vital. Building out the steps of a preventive maintenance (PM) process should include the spare parts needed. Creating a spare parts bill of materials associated with each asset being maintained can greatly help, and as a result, all CMMS users will have visibility into needed parts and receive alerts for low-stock parts needed for upcoming work. When a team adopts a preventive mindset, it will have a more accurate knowledge of parts to stock. If an organization is more reactive, the buffers will be higher given the reduced predictability of corrective maintenance.
Beyond having good visibility into on-hand parts, automation and better use of data enable smarter decision-making. Day-to-day, normal maintenance operations will create insightful data to make more informed decisions, increase efficiency, control costs and drive profitability. This is for all aspects of maintenance operations but especially helpful for managing spare parts. By harnessing big data and analytics, manufacturers can perform smarter decision-making built for the long term. Users may not be able to make the supply chain go faster, but they can accommodate these tricky timelines to better prepare and reduce unplanned downtime that cuts into the bottom line.
A CMMS helps ensure that manufacturers have the right parts at the right cost just when they need them. Within an inventory module, there should be a catalog of all parts including suppliers and vendors, current quantities (on-hand, on-reserve, on-order, backorder, etc.), as well as detailed information on where these parts are stored.
At any time, maintenance technicians should have insight into the number of available parts from their desktop or mobile device, which reduces the time spent searching for a part that may not be in stock. Taking the time to build out part kits and robust preventive maintenance plans helps organizations implement an effective JIT manufacturing process. Additionally, these processes are aided by mobile devices and barcoding technology. By scanning barcodes, manufacturers can get a more accurate account of the parts used and needed, achieve greater visibility and ultimately collect data to predict what will be needed in the future.
As manufacturers get low on parts, technology must aid and inform organizations automatically. A CMMS allows organizations to establish a minimum or maximum count for all parts, and as teams move through parts, the technology automatically keeps track. As parts get low, email alerts, mobile device notifications or dashboard alerts can warn teams before risking stockouts. A modern, well-implemented CMMS will make this possible and provides instant insight all before a technician walks across the plant and searches for parts in vain.
Given current conditions and supply chain disruptions, manufacturing companies could more easily fall into unplanned downtime. Intelligent tools and technology, like a CMMS, can help manufacturers not only create and use a more measured JIT strategy but also build lean operational processes.