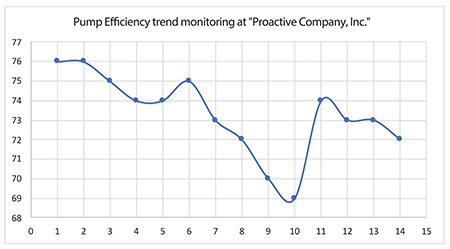
A recently released standard1 on repairing vertical turbine pumps is a first in a set of standards for the repairs and upgrades of various pump types as defined by the Hydraulic Institute. These standards answer not only how to repair a pump, but also when and why.
A good standard must be an educational tool for plant engineers and maintenance and procurement specialists to better understand the best practices to apply for a repair or an upgrade. It must also connect the economic impact of the repair-or-not decision to pump reliability and dependability.
The life of a pump depends greatly on the application. A pump handling coal slurry will likely not have the same life span as a pump handling clean, cold water. Likewise, a pump racing all over its performance flow to satisfy a wide range of flow requirements will not survive as long as a pump steadily pumping the same set flow for years. The best indicator of when to repair a pump is by analyzing its performance: Has its flow reduced over the years so that it simply cannot satisfy the flow demand? Has its efficiency dropped to a point that it “burns money” and costs more to operate than to repair it and restore it to efficiency? Is it beginning to vibrate excessively, making seals leak and failing frequently?
As a rough indicator of when to expect an upcoming repair and in order to schedule it to coincide with the next plant outage, each plant should maintain some history and statistics of their pumps’ average life in order to minimize disruption and additional expenses. At a municipality with several plants, a comparison of meantime between repairs (MTBR) of similar pumps at similar applications at their various sister plants might be an additional factor in learning what is done right at one plant versus another. This could also uncover where deficiencies might be that could lead to a reduced MTBR or meantime between failures (MTBF).
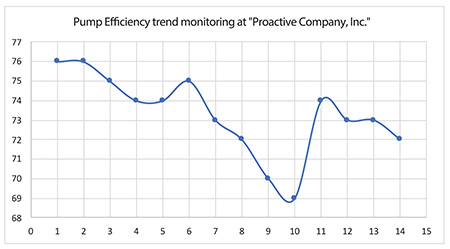
A before-and-after-repair comparison of pump efficiency and vibrations is a good and relatively simple way to assess the effectiveness of a repair. Doing periodic efficiency testing like this, perhaps yearly, will help a plant determine when and how to do the next repair or upgrade. The exact value of the pump efficiency would not particularly matter in this approach, but what will matter is the trend (Image 1).
Take the efficiency test, for example. For comparative purposes, it does not need to be as exact and sophisticated as it would be if the efficiency of a recently installed new pump was somehow a suspect. Even a small change in the efficiency of a pump that is not operating as an OEM guaranteed can cost a plant a lot of money. One percent of efficiency degradation of a 100-horsepower (hp) pump, operating continually throughout the year, would cost under $1,000 and is unlikely to signal a need for repair. A 5,000-hp unit that costs $30,000 per year is another story.
Efficiency is not measured directly (unless using specialized instrumentation2), but instead is derived/calculated from the measured parameters: flow, pressures (discharge minus suction), current, voltage and power factor of the motor. Obviously, we are talking about measuring the efficiency of the entire unit (pump plus motor), with the ratio of hydraulic power to the electric power as the unit efficiency.
Ultimately, from the standpoint of comparison and information gathering informing the decision to repair or not, the before-and-after-repair comparison, as well as periodic (perhaps yearly or so) data taking, would serve as a good and practical method to help maintenance departments decide to act or not act on the data. Obviously, there are exceptions to this rule and approach, but in most cases it will work fine and it gives recently hired young engineers a chance to learn the ropes and the opportunity to perhaps become the “efficiency captain” of the plant.
Fluid power is flow x head x specific gravity (SG)3. That is the “good” power. Electric power coming to the motor is current x voltage x √(3) (for a three-phase motor, or use 1 for a single-phase motor) x the power factor. The difference is “parasitic” power loss inside the unit (friction, rubs, leakage, etc.). By applying the proper unit (U.S. customary units used here) we get:
Fluid power (FP) = Q x H x SG, where [Q] is flow in gallons, [H] is head in feet (differential pressure converted to pump head—remember the formula?), and [SG] is fluid specific gravity.
The ratio of fluid power to electric power to the motor is the efficiency of the total system (pump plus motor). In our previous articles, as well as in our periodic Pump School sessions (live and virtual presently), we cover these details and definitions scrupulously, but for this article, we will allow you to brush up on these details on your own homework time. And so, by measuring the above parameters and calculating efficiency—before and after the repair—you can evaluate the effectiveness of the repair job.
Let’s do a little homework quiz, and your answer will be published in one of my follow-up articles: A vertical turbine pump handling clean water at a municipal station pumps 3,000 gallons per minute (gpm), with discharge pressure showing 80 pounds per square inch gauge (psig). There is no suction gauge installed, but the pump takes water from the intake basin with the water level roughly 30 feet below the discharge gauge location elevation. The measured current is 170 amps at a three-phase 480 volts motor. Originally, as plant records show, the motor amps used to draw only 160 amps for the same conditions. A visiting repair shop salesman proposed a $22,000 repair due to what he felt was a significantly reduced efficiency and, thus, “money into the drain,” as he put it. Question: Should the plant proceed with the proposed repair? (Assume this operates an average of eight hours a day.)
Download and take a look at a VPRS spec.1 You will find it is a good learning tool and a practical guide to your repairs and upgrades work. We look forward to hearing from you.
References
1. Vertical Pumps Repair Specification (VPRS), rev. 6: www.pump-magazine.com/pump_magazine/specifications/specifications.htm
2. Pumps Reliability and Efficiency Measurement System: www.pumpingmachinery.com/consulting/PREMS-2A/prems-2a.htm
3. Pump School Training: www.pumpingmachinery.com/pump_school/pump_school.htm
To read more Pumping Prescriptions columns, click here.
Read the second part of this article here.